Betoneinbau auf dem BBI
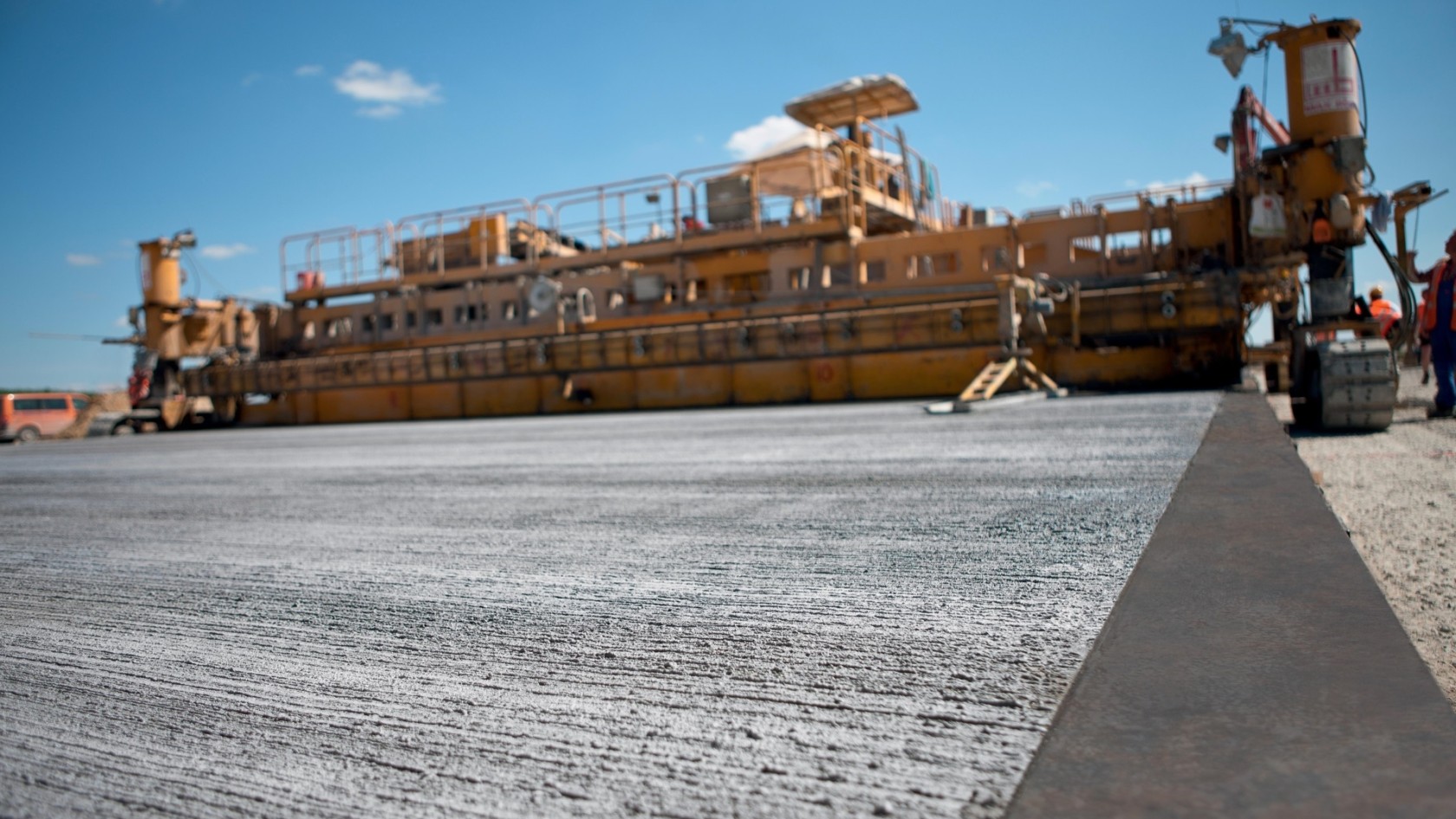
In der Metropole Berlin, mit 3,5 Mio. Einwohnern die größte deutsche Stadt, gibt es historisch bedingt mehrere Flughäfen. 1996 beschlossen die Gesellschafter der Berliner Flughäfen, die Länder Berlin und Brandenburg sowie der Bund, den Bau eines internationalen Flughafens für die Region Berlin-Brandenburg. Seit dem Sommer 2006 werden die Pläne Realität: Der Flughafen Schönefeld wird ausgebaut zum neuen Flughafen Berlin Brandenburg International, kurz „BBI“ genannt. Wesentlichen Anteil an den Bauarbeiten hat eine ganze Flotte von Wirtgen-Gleitschalungsfertigern. Sie bauen die „luftseitigen Flächenbauwerke“, das heißt Taxiways, Rollfelder, das Vorfeld sowie die Start- und Landebahn Süd mit einer beeindruckenden Gesamtfläche von 1,5 Millionen Quadratmetern.
Megaprojekt für die Hauptstadt
Mit den Airports Tegel und Schönefeld sichern die Berliner Flughäfen die Luftverkehrsinfrastruktur für die Hauptstadtregion Berlin-Brandenburg. Der Ausbau des Flughafens Schönefeld zum zukünftigen Hauptstadt-Airport bietet eine positive ökologische Gesamtbilanz gegenüber dem aufgrund der historischen Teilung Berlins zersplitterten Flughafensystem – sowohl beim Flächenverbrauch als auch bei der Lärm- und Verkehrsbelastung.
In einem ersten Schritt wurde der Flughafen Tempelhof Ende Oktober 2008 geschlossen. Die Schließung Tegels erfolgt 2012 mit der Eröffnung des BBI. Seit Sommer 2006 sind die Bauarbeiten unmittelbar hinter der Stadtgrenze Berlins in vollem Gange. Die südliche Start- und Landebahn des existierenden Flughafens Schönefeld wird als Nordbahn des neuen Flughafens fungieren. Dazu kommt ein komplett neues Terminal mit Anbindung an das Straßen- und Schienennetz sowie eine zusätzliche, vier km lange Start- und Landebahn im Süden. Modernste Technik und eine hervorragende Infrastruktur bieten Geschäftsreisenden und Touristen künftig alles, was Fluggäste sich wünschen.
Am „alten“ Flughafen Schönefeld starten und landen noch Flugzeuge. Gleichzeitig stellen die Einbauzüge von Wirtgen rund 2 km weiter südlich die Betonflächen in den südlichen Rollbahnsystemen Taxiway A und B mit Arbeitsbreiten von bis zu 15 m her.
Berlin weltweit unter den Top 50
Für Mitte 2012 ist die Eröffnung des neuen Flughafens geplant. Dann wird der BBI mit einer Kapazität von anfangs bis zu 27 Millionen Passagieren pro Jahr den Betrieb aufnehmen. Schwerpunkt des BBI werden Ziele in Europa sowie ausgewählte Langstreckenverbindungen sein. Berlin bietet dafür eine strategisch optimale Lage: Von dort sind die Flugzeiten nach Osteuropa und Asien eine Stunde kürzer als von etablierten Drehkreuzflughäfen im Westen des Kontinents.
Berlin ist schon heute der drittgrößte Flughafenstandort in Deutschland. Ziel ist es, die Region Berlin-Brandenburg mit dem BBI in den Top Ten der europäischen Flughafenstandorte zu etablieren. Die heutigen Konzepte sehen sogar schon Möglichkeiten zur Erweiterung vor: Die Kapazitäten können bei entsprechender Entwicklung auf bis zu 360.000 Flugbewegungen bzw. bis zu 45 Millionen Passagiere jährlich erweitert werden.
Flotte von Wirtgen Gleitschalungsfertigern im Dauereinsatz
Zur Abwicklung des Großprojektes gründeten die Firmen Gebrüder von der Wettern, Eurovia VBU und Eurovia Beton die „ARGE BBI GU II“. Sie vergab die Ausführung der Arbeiten an die „ARGE BBI GU II – Luftseitige Flächenbauwerke“, eine Arbeitsgemeinschaft der Firmen Eurovia VBU, Max Bögl Bauunternehmung und Eurovia Beton. Die Unternehmen waren bereits im Besitz großer Wirtgen-Gleitschalungsfertiger vom Typ SP 1500, SP 1500 L bzw. SP 1600. Seit Mai 2008 sind die Maschinen im Dauereinsatz und bauen Tag für Tag und Nacht für Nacht auf den großen Flächen Beton ein. Parallel dazu arbeiten zwei Gleitschalungsfertiger vom Typ SP 500 an der Vervollständigung kleinerer Flächen und an Stellen, wo besonders starke Gefälle gefordert sind.
Ein starkes Team: In der ARGE „BBI GU II – Luftseitige Flächenbauwerke“ stellen die Firmen Max Bögl und Eurovia Beton für jeden Wirtgen-Einbauzug eine Bedienmannschaft. Nach der 12-Stunden-Schicht erfolgt die Übergabe im fliegenden Wechsel.
6.000 Kubikmeter Beton an einem Tag
„Es ist außerordentlich beeindruckend, an einem solchen Großprojekt mitzuarbeiten. So eine Chance hat man nicht oft im Leben“, berichtet Oberbauleiter Dipl.-Ing. Christoph Hofmeister (Max Bögl). „Insgesamt verbauen wir ca. 600.000 Kubikmeter Fahrbahndeckenbeton über die gesamte Projektlaufzeit. An einem guten Tag verarbeiten wir in 24 Stunden 6.000 Kubikmeter Beton mit einem großen Wirtgen-Fertiger“, beschreibt Hofmeister die Dimensionen. Solche enormen Tagesleistungen erfordern eine präzise Planung und perfekt eingespielte Bedienerteams. Keine einfache Aufgabe bei einem Großprojekt, denn in Spitzenzeiten arbeiteten täglich bis zu 350 Personen aus den Reihen der Arbeitsgemeinschaft „BBI GU II – Luftseitige Flächenbauwerke“ auf der Baustelle. Davon waren rund 90 Mitarbeiter unmittelbar mit dem Einbau befasst: Darunter sind neben den Kolonnen mit etwa 15 Personen pro Einbauzug auch Mitarbeiter, die zum Beispiel die stehenden Schalungen auf- und abbauen, Fugen schneiden oder Dübel anliefern, sowie das Personal für die Planung und Qualitätskontrolle.
Rund um die Uhr sind die Wirtgen-Gleitschalungsfertiger der ARGE „BBI GU II – Luftseitige Flächenbauwerke“ in Betrieb. Mit einer Einbaugeschwindigkeit von etwas mehr als 1 m/min bauen sie die 40 cm dicke, zweilagige Betondecke aus sehr steifem Beton mit höchster Präzision ein.
130 cm hoher Aufbau
Die neue Start- und Landebahn Süd umfasst eine Fläche von 240.000 qm und beeindruckt mit einer Länge von 4.000 m und einer Breite von 60 m. Damit am Flughafen BBI später Kolosse wie der A 380 problemlos landen und starten können, wurde im Bereich der Start- und Landebahn Süd sowie auf allen anderen Flugbetriebsflächen in Betonbauweise ein 130 cm hoher Aufbau realisiert. Auf den untersten 50 cm hat man zunächst den teils nicht-bindigen, teils bindigen Boden gezielt mit Zement verbessert und verdichtet. Die nächste Schicht setzt sich zusammen aus 15 cm eines verfestigten Gemisches aus hydrophobiertem Zement und frostsicherem Sand. Für diese Arbeiten vertrauten die ausführenden Firmen übrigens auch auf Wirtgen-Technologien: Es waren mehrere Bodenstabilisierer vom Typ WR 2500 S im Einsatz.
Darüber liegt eine 25 cm starke HGT. Zu guter Letzt haben die Gleitschalungsfertiger eine 40 cm dicke Betonschicht in stehende Schalungen mit Sinusprofil eingebaut. Die Planung und Ausführung sah eine bewehrungslose Betonbauweise mit der Ausbildung von Längs- und Querfugen vor. Die Querscheinfugen sind generell im Abstand von 25 cm verdübelt, die Längsschein- und Längspressfugen sind in Randbereichen verankert. Im Bereich von Einbauten wie Schächten und Fundamenten wurden die Dübel und Anker auf Körbe verlegt. In Zwickeln und bei geometrisch ungünstigen Plattenabmessungen sowie in Bereichen von Einbauten legte man zur Vermeidung von Rissen auch außerhalb der Sollbruchstellen zusätzlich eine Bewehrung ein.
Hochleistungsbeton für den Hauptstadt-Airport
Die Qualitätsanforderungen für Materialien und Verarbeitung sind sehr hoch. „Als Baustoff verwenden wir für den BBI besonders belastbaren Splittbeton der Druckfestigkeitsklasse C35/45 mit Luftporen. Dieses Material hält die enormen mechanischen Belastungen durch die großen Flugzeuge ebenso aus wie die hohen Temperaturen bei der Landung oder die Beaufschlagung durch Enteisungsmittel im Winter“, erläutert Dipl.-Ing. Patrick Stryj von becker bau bornhöved (bbb) die Materialauswahl. Er ist verantwortlich für Europas modernstes Betonmischwerk in unmittelbarer Nähe der Baustelle. In bis zu 6 Hochleistungsmischanlagen, die rund um die Uhr in Betrieb sind, können täglich bis zu 11.000 Kubikmeter Beton für den Flächen- und Hochbau produziert werden. Um die Straßen und die Umwelt zu entlasten, werden Zement, Sand, Kies und Splitt per Bahn angeliefert.
Planung bis ins kleinste Detail
Dieses Großprojekt erfordert eine beachtliche Logistik und Planung. Auf Basis monatlicher und wöchentlicher Bedarfsplanungen werden die Rohmaterialien für den Beton geordert. Aufgrund einer täglichen Feinplanung unter Beachtung der aktuellen Wetterprognosen wird dann der Beton produziert und in der gewünschten Qualität an den Fertiger geliefert. Hierfür stehen bis zu 50 Lkw zur Verfügung. Ein Qualitätssicherungsplan gewährleistet die Betonqualität durch mehrfache begleitende Materialprüfungen. Überprüft werden zum Beispiel Temperatur, der Wasser-Zement-Wert, das Verdichtungsmaß und der Luftporengehalt. Nachdem dem Betoneinbau erfolgen weitere Prüfungen, zum Beispiel auf Biegezug- und Druckfestigkeit.
Die Logistik ist eine der großen Herausforderungen beim Bau des neuen Flughafens. Rund 50 Lkw sind alleine für den Betontransport vom nahe gelegenen Mischwerk zum Einbauort erforderlich.
5 Gleitschalungsfertiger für 1,5 Millionen Quadratmeter
Für die Einbauqualität stehen die Mannschaften am Gleitschalungsfertiger gerade. „Wir verarbeiten hier relativ steifen Beton. Das hohe Gewicht der Wirtgen-Maschinen und die hervorragende Verdichtungsleistung kommen diesem Umstand sehr entgegen“, erklären die Einbaumeister Michael Lakotta und Hero Sauer.
Auf den Start- und Landebahnen und den Taxiways waren zeitweise bis zu drei Großfertiger – ein SP 1500 L, ein SP 1500 und ein SP 1600 – gleichzeitig im Einsatz. Sie bauen den Beton einschichtig zweilagig ein. Das bedeutet, beide Lagen (33 cm Unterbeton und 7 cm Oberbeton) bestehen aus dem selben Beton. Dazwischen positioniert der automatische Dübelsetzer (DBI) die Dübel in immer gleichen Abständen. Für die Ebenheit sorgen Quer- und Längsglätter. Dahinter bringen zwei Nachbehandlungsgeräte vom Typ TCM 1800 den Besenstrich und eine Dispersion als flüssiges Nachbehandlungsmittel auf. Diese beiden Tätigkeiten wurden, je nach Witterung, durch den Einsatz von zwei Geräten voneinander entkoppelt. Dadurch konnte der optimale Zeitpunkt für jeden Teilschritt gewählt werden.
Der Besenstrich verleiht der Betondecke direkt nach dem Einbau eine definierte Textur. Dadurch erhält die Fläche die geforderte Griffigkeit.
Mit einer Rautiefe von mehr als 1 mm verfügt der Beton über eine gute Griffigkeit. Eine Lage von etwa 220 g Dispersion pro qm verhindert das verfrühte Austrocknen des Betons. Ständiger Wind und die hohe Rautiefe erforderten diese großen Mengen, denn nur so können Risse sicher vermieden werden.
Flexibles Maschinenkonzept
Ein wichtiger Punkt für die Effizienz einer solch großen Baumaßnahme ist das Umsetzen und Umbauen der Fertiger. Beim Umsetzen überzeugte insbesondere der SP 1500 mit seinem 2-Ketten-Konzept durch einfaches Handling. Die Betondecke wurde an den verschiedenen Bereichen in unterschiedlich breiten Bahnen eingebaut. Daher waren mehrfache Umrüstungen auf Arbeitsbreiten zwischen 12,50 m und 15 m erforderlich. Diese Arbeit erledigten die Teams auf der Baustelle, um Zeit und Kosten für die Maschinentransporte zu sparen. An dieser Stelle bietet Wirtgen mit der modularen Bauweise und verschieden großen Modulbreiten den Baufirmen maximale Flexibilität.
Perfekte Ebenheit
Der Beton wurde zwischen stehenden Schalungen mit Sinusprofil eingebaut. Auf diese Weise konnten die extrem hohen Anforderungen an die Längspressfugen optimal erreicht werden. Für die korrekte Höhe und Neigung nutzen die erfahrenen Flughafenbauer Drehgeber am Leitdraht bzw. Schlittschuhtaster auf der bereits gefertigten Betondecke. Damit erfüllten sie die Vorgaben für die Ebenheit gemäß der ZTV Beton sowie die Querneigung zwischen 0,7 und 1,5 %, wie regelmäßige Messungen mit dem Planografen bescheinigten.
Zuverlässigkeit zählt
Beim 24-Stunden-Betrieb, verbindlich georderten Betonmengen und eng gesteckten Terminen ist die Zuverlässigkeit der Maschine das „A und O“. Deshalb vertrauen die Arge-Partner auf Wirtgen-Geräte. Überzeugen konnte in Berlin auch der schnelle und kompetente Service. „Die Zusammenarbeit mit der Niederlassung Wirtgen Windhagen funktioniert hervorragend. Das können wir bei bis zu 2.000 Maschinenstunden pro Jahr und Fertiger bestätigen“, berichtet der MTA-Leiter, Dipl.-Ing. Hakon Schalk von der Eurovia VBU. Oberbauleiter Dipl.-Ing. Frank Zimmermann (Eurovia Beton) ergänzt: „Wir erreichen die sehr hohen Tagesleistungen, weil die meisten Checks sowie Instandhaltungs- oder Reparaturarbeiten bereits auf der Baustelle erledigt werden können. Hier nutzen wir zum Beispiel das Zeitfenster während der regelmäßigen Maschinenreinigung am Ende der Nachtschicht. Unsere gut geschulten Mitarbeiter erledigen vieles selber. Bei weitergehenden Arbeiten an den Maschinen hat uns Wirtgen immer perfekt unterstützt.“
Service vor Ort: Kompetente Wirtgen-Servicetechniker begleiten den Einsatz und unterstützen die Teams bei Bedarf auf der Baustelle.
Kompetenz schafft Effizienz
„Ein weiterer wichtiger Baustein für das Gelingen eines solchen Projektes ist das Training der Mitarbeiter in kleinen Gruppen“, beschreibt Oberbauleiter Frank Zimmermann die Philosophie seines Hauses. Martin Datzert, Servicetechniker und Gleitschalungsfertiger-Spezialist der Niederlassung Wirtgen Windhagen, hat das Team im Laufe des langen Winters intensiv geschult: „Die Bediener kannten die Maschinen schon vorher sehr gut. Durch die Trainings konnten wir das Wissen noch vertiefen.“ Insbesondere der regelmäßige, selbstständige Maschinencheck und eine schnelle Fehleranalyse sind ihm wichtig. So können verschlissene Bauteile rechtzeitig getauscht werden, bevor aufwändige Reparaturstopps notwendig werden. Damit erreichen die Teams eine hohe Verfügbarkeit und einen zügigen Baufortschritt.