Brechtechnik
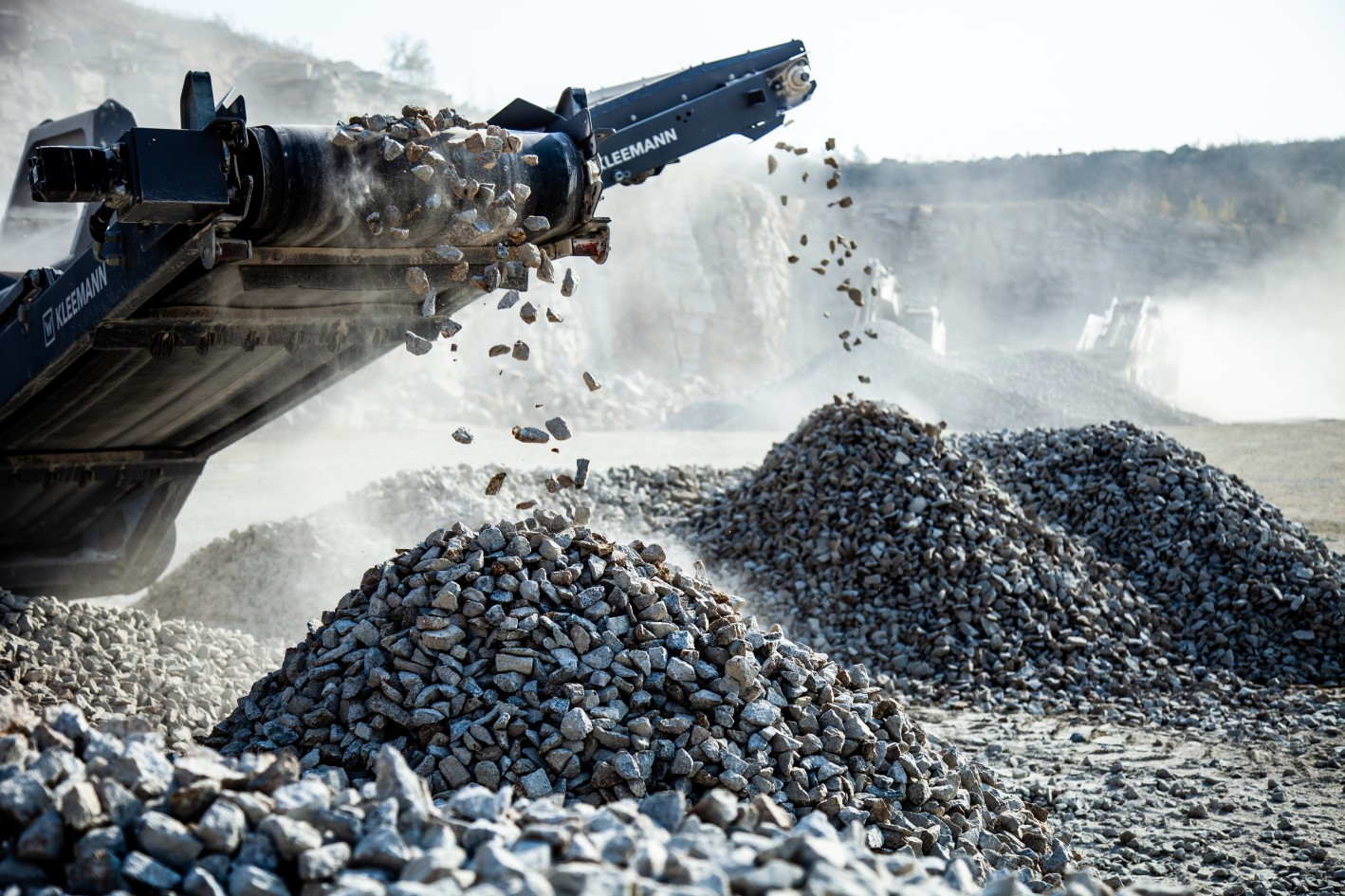
Aufgabematerial, erforderliches Endprodukt und Wirtschaftlichkeit beeinflussen die Wahl der Brechtechnik.
Der Abbau natürlicher Gesteinsarten ist verbunden mit dem Einsatz von Maschinen, die Material mit hohen Druckfestigkeiten gezielt und wirkungsvoll zerkleinern. Backenbrecher eignen sich ideal für den harten Einsatz in Steinbrüchen und werden vorwiegend als Vorbrecher eingesetzt.
Backenbrecher arbeiten nach dem Prinzip der Druckzerkleinerung. Die Zerkleinerung des Brechguts erfolgt im keilförmigen Spalt zwischen der festen und der von einer Exzenterwelle bewegten Brechbacke. Durch den elliptischen Bewegungsablauf wird das Brechgut zerdrückt und fällt durch die Schwerkraft nach unten. Dies geschieht so lange, bis das Material kleiner ist als der eingestellte Brechspalt.
Die Zerkleinerungsenergie wirkt dabei mit großen Kräften und mit geringer Geschwindigkeit auf das zu bearbeitende Brechgut. Der Name Backenbrecher leitet sich aus den für die Zerkleinerung notwendigen Brechbacken und der kauenden Bewegung ab.
Backenbrecher werden zur Grob- und Vorzerkleinerung von spröden, mittelharten und harten Gesteinen eingesetzt. Sie werden am häufigsten als Primärbrecher verwendet.
Seltener sind Backenbrecher in der Lage ein normgerechtes Endprodukt zu erzeugen. In einigen Recyclinganwendungen können mit kleinen Backenbrechern Schottertragschichten für den untergeordneten Straßen- und Wegebau hergestellt werden.
Kegelbrecher werden in mittelhartem bis hartem sowie abrasivem Naturstein und zur Rohstoffaufbereitung in Mininganwendungen eingesetzt. Die Kegelbrecher liefern in der 2. und 3. Brechstufe normgerechte kubische Endkörnungen.
Kegelbrecher gibt es in verschiedenen Größen, Ausführungen und für unterschiedliche Anwendungen.
Bei Kegelbrechern findet die Zerkleinerung in einem sich umlaufend öffnenden und schließenden Brechspalt zwischen Brechmantel und Brechkegel durch Druckzerkleinerung statt. Das Öffnen und Schließen erfolgt dabei gleichzeitig auf den gegenüberliegenden Seiten des Brechraums.
Kegelbrecher gibt es in unterschiedlichen Bauweisen. Bei den von KLEEMANN eingesetzten Kegelbrechern ist die Brecherachse in den Unterrahmen eingepresst. Der Brechkegelträger ist auf einer exzentrischen Antriebseinheit verlagert. Durch die Rotation der Antriebseinheit öffnet sich der Spalt zwischen Brechkegel und Brechmantel umlaufend. Die zu produzierende Körngröße wird durch Heben bzw. Senken des Brechmantels verändert.
Kegel- und Kreiselbrecher werden hauptsächlich dann eingesetzt, wenn eine Prallzerkleinerung auf Grund hoher Druckfestigkeit des Brechgutes nicht mehr möglich ist oder die Höhe der Verschleißkosten wegen der Abrasivität des Gesteins wirtschaftlich nicht mehr zu vertreten ist.
Bauartbedingt sind Kegel- und Kreiselbrecher hinsichtlich Aufgabegröße und dem erreichbaren Zerkleinerungsverhältnisses limitiert.
Auf mobilen Anlagen werden Kegelbrecher hauptsächlich zum Nachbrechen in der sekundären und tertiären Brechstufe verwendet.
Kreiselbrecher unterscheiden sich aufgrund ihrer Bauart von Kegelbrechern.
Im Gegensatz zum Kegelbrecher, der über eine feststehende Welle verfügt, auf welcher die Antriebseinheit und der Kegelträger rotieren, besitzt der Kreiselbrecher eine hydraulisch in vertikaler Richtung verfahrbare Hauptwelle, auf die der Kegelträger fest aufgeschrumpft ist. Die Welle ist am unteren Ende axial auf einem Drucklager abgestützt, das wiederum auf dem Verstellkolben verlagert ist. Die Brechspaltverstellung erfolgt durch Heben und Senken des Verstellkolbens und damit auch der Hauptwelle. Am oberen Ende werden die horizontalen Brechkräfte über das Kopflager, das in einer Quertraverse, dem sogenannten „Spider“, integriert ist, in das Oberteil des Brechers eingeleitet.
Bauartbedingt ist die Höhe eines Kreiselbrechers generell deutlich größer als die eines vergleichbaren Kegelbrechers.
Die leistungsstarken Allrounder
Ob im Steinbruch oder auf der Baustelle - mit Prallbrechern wird Gestein effizient so zerkleinert, dass Kornform, Kornverteilung und Sauberkeit den strengen Normen für Beton- und Asphaltzuschlagstoffe entsprechen. Dabei erreichen Prallbrechanlagen neben einer erstklassigen Produktqualität auch beachtliche Durchsatzleistungen.
Im Gegensatz zur Druckzerkleinerung wird beim Prallbrecher nach dem Prinzip der Prall- und Schlagzerkleinerung gearbeitet. Dabei wird das Brechgut von einem schnell drehenden Rotor erfasst, stark beschleunigt und auf ein feststehendes Prallwerk, die Prallschwingen, geschleudert. Von da aus fällt es wieder in den Schlagkreis des Rotors zurück. So wird das Brechgut immer weiter gebrochen, bis es den Spalt zwischen Rotor und Prallschwingen passieren kann.
Der eigentliche Brechvorgang findet bei Kontakt des Gesteins mit den Schlagleisten und den Prallschwingen statt. Zusätzlich findet eine Zerkleinerung durch Kontakt der Steine untereinander 3 statt.
Prallbrecher finden als Primär- und Sekundärbrecher Verwendung. Als Primärbrecher finden Prallbrecher ihre Anwendung im Kalkstein; vor allem dort wo hohe Feinanteile, gute Kubizität und Bruchflächigkeit sowie eine hohe Leistung gefordert sind.
Im modernen Recycling von Beton, Asphalt und Bauschutt sind sie heute dank ihrer hohen Leistung und der hervorragenden Endproduktqualität nicht mehr wegzudenken. Im Gegensatz zur Druckzerkleinerung sind sie in der Lage, Bewehrungseisen sauber aus dem Beton herauszulösen und damit ein weitgehend eisenfreies Endprodukt herzustellen.
Als Sekundärbrecher werden sie häufig hinter Backenbrechern zur Erzeugung von normgerechten Endprodukten eingesetzt.
Von Prallmühlen spricht man in der Regel, wenn das damit zu produzierende Endprodukt nur eine Korngröße bis ca. 10 Millimetern haben soll. Prallmühlen werden als Nachbrecher oft in der dritten und vierten Brechstufe verwendet, da die Aufgabegrößen entsprechend klein sein müssen.