A1 final products for National Route 1A
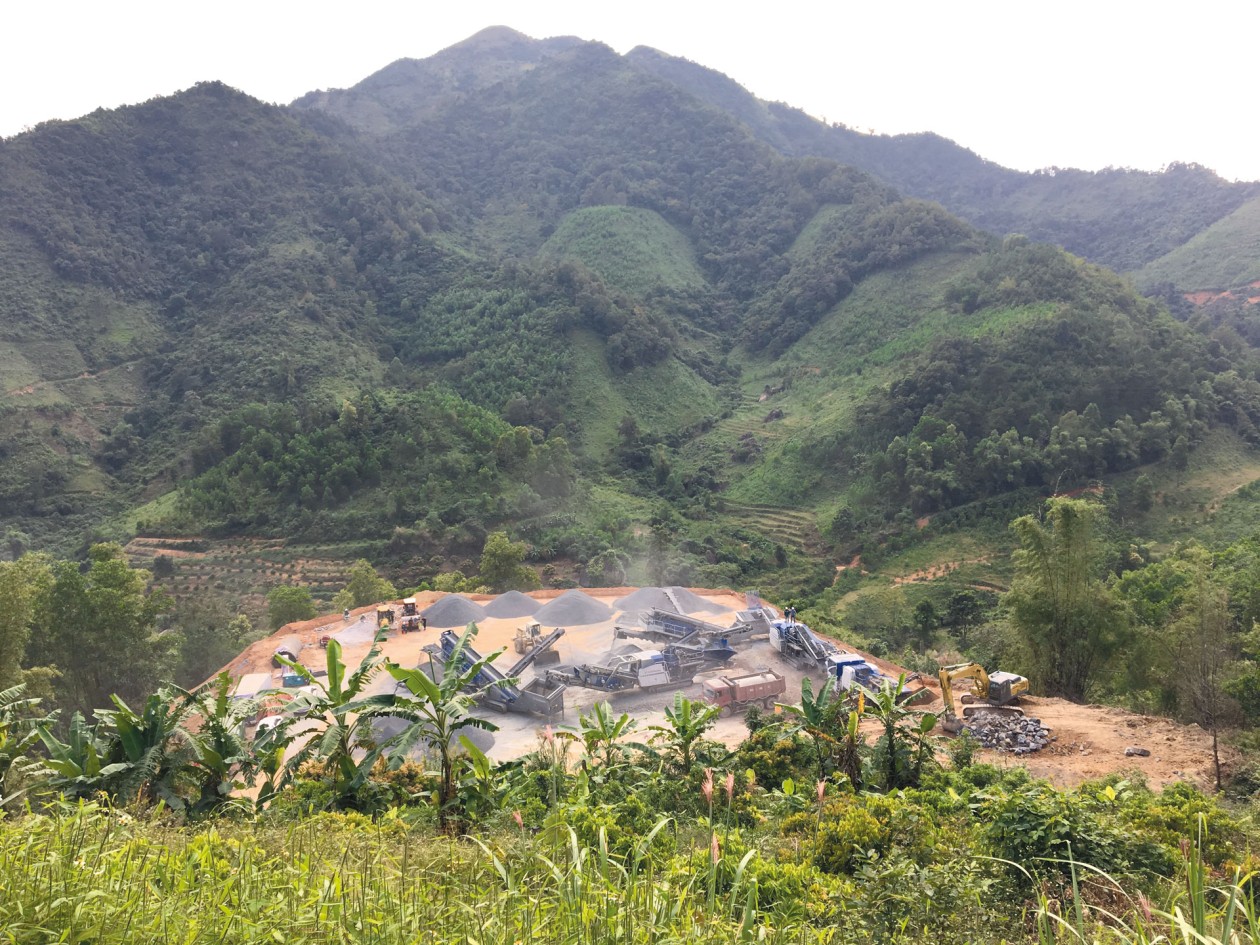
In the north of Vietnam lie the emerging city of Lang Son, located on the border with China, and National Route 1A, the heavily congested motorway to the capital, Hanoi: a KLEEMANN plant combination was brought in to eliminate this bottleneck.
A total of 5 interlinked plants – 3 crushing and 2 screening plants – processed the basalt, a particularly hard rock, for the surface course, fulfilling high quality requirements.
In action eliminating a bottleneck
With an immense total length of 2,236km, National Route 1A is particularly heavily trafficked along the section between kilometre 16 (Lang Son) and kilometre 170 (Hanoi). The stretch, which is narrow, steep and winding in some sections, is used by lorries, cars, countless scooters and even pedestrians. It was therefore high time the performance and safety of National Route 1A were improved. Licogi 16 JSC – one of Vietnam’s largest construction companies with 20,000 employees and a firm foothold in almost all sectors of the construction industry – won the contract for an approximately 100km section of the 154km-long project.
Vietnam’s first interlinked KLEEMANN plant combination
Licogi 16’s highly dynamic Civil Engineering division is carrying out a number of road and bridge construction jobs and maintains close business relations with Vitrac, the WIRTGEN GROUP’s dealer in Vietnam. Spurred on by their very good experience with the technologies of the other product brands, the company opted for a track-mounted interlinked plant combination from KLEEMANN. The blue crushing and screening plants are thus making their debut in Vietnam, an event which is attracting close attention across the region and beyond. The interlinked plant combination comprises 5 units. Listed in the order of connection, the plants concerned are an MC 110 Z EVO jaw crusher, an MCO 9 EVO cone crusher, an MS 703 EVO screening plant, an MCO 9 S EVO cone crusher and an MS 19 D screening plant.
Licogi 16 JSC quarry team
High-precision crushing of the hard rock basalt
In the quarry 40km south of Lang Son, the Licogi 16 team found itself facing two challenges: firstly, they needed to crush the hard and abrasive basalt and to classify it into clean aggregate fractions. Secondly, they had to fulfil very high quality requirements.
Armed with their new KLEEMANN plant combination, the team from Licogi 16 was able to meet the required criteria with astonishing ease. The team discovered that the crushing and screening plants take care of everything almost completely autonomously, once you know how to coordinate them. The automated Continuous Feed System (CFS) played a key role in making the work easier. The crushing plant in the first crushing stage – in this case, a KLEEMANN MC 110 Z EVO jaw crusher – only draws as much feed material into its crushing chamber as the entire line-coupled plant combination can process. This prevents overloads and, to the greatest possible extent, material blockages, too. After all, the KLEEMANN plants are tough performers.