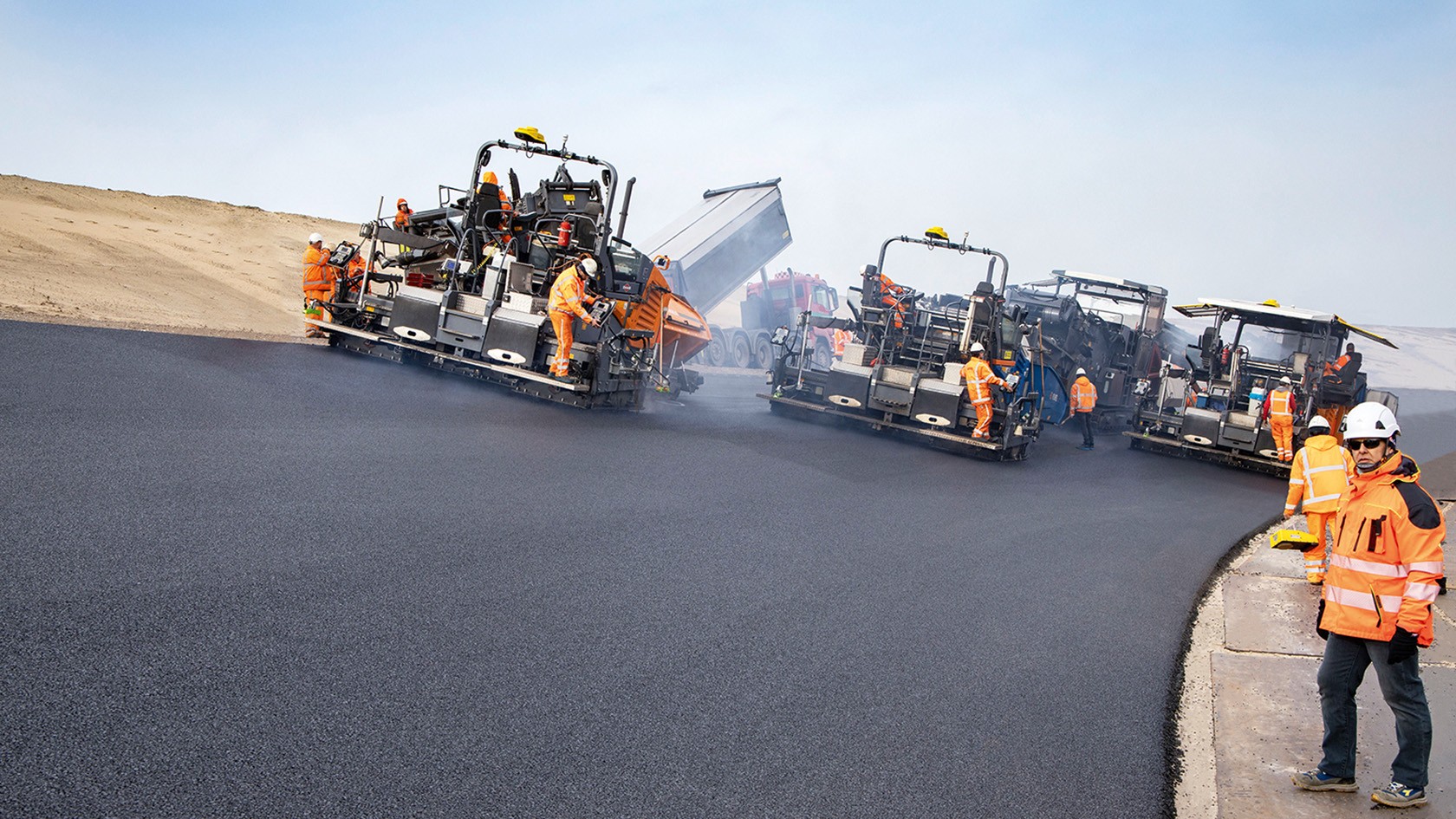
Some projects are so specialist that there are hardly any construction companies with significant experience to draw on - another reason why it is so valuable to have a partner with the expertise and experience to take things forward. The rehabilitation and modification of the race track in Zandvoort was a project like this.
How do you get hold of and process prescribed specialist mixes to satisfy the most stringent regulations of the FIA, motor sport’s world governing body? How do you pave sloping bends with an incline of up to 32%? And how do you satisfy requirements which Filippo Piccoli, technical manager at experienced engineering firm Studio Dromo, describes as “the most extreme race track construction I have ever seen and been involved with”?
To get successful answers to these questions, construction manager Mark van Kessel from contractor Gebr. Van Kessel involved his contact Roel Vissers from the WIRTGEN GROUP’s Netherlands subsidiary right from the outset. After all, construction and rehabilitation of race tracks are always a bit special. So it was for contractors Gebr. Van Kessel B.V. and KWS Infra B.V., too, both of them part of Royal VolkerWessels N.V.
The contract was to partly rebuild the track in the area of the two sloping bends and also to complete associated rehabilitation and modernization work. The aim was for the two sloping bends to enable high-performance racing cars to achieve higher speeds on the bends and thus return to the straight more quickly. These modifications to the track layout are intended to encourage overtaking and were implemented in line with plans from renowned Italian race track engineering firm Studio Dromo, whose experts also kept a close eye on the job site.
The most famous race track in the Netherlands hosted the Netherlands Formula 1 Grand Prix a total of 30 times between 1952 and 1985. This premium motor sport event is now returning to Zandvoort. The track, located between the dunes and the sea on North Holland province’s North Sea coast, is nicknamed the “rollercoaster in the dunes”.
It quickly became clear during initial discussions on the project with experts from the WIRTGEN GROUP that a trial paving run should be carried out to ensure everything went smoothly on the race track itself. After all, the two sloping bends with an incline of up to 32% are even steeper than the bends of high-speed oval tracks in the US. It was therefore important for success that the paving team knew exactly what mattered during the process and what settings to make to the machinery.
Compaction was just as demanding as paving. It was completed by HAMM rollers of the HW, HD, HD+ and HD+ CompactLine series.
Tolerance just ± 2mm: the three SUPER 1900-3i machines had to deliver precision work on the sloping bends, too, and were equipped with the Big MultiPlex Ski sensor system from VÖGELE for the purpose.
Planned for the job site in Zandvoort were three VÖGELE SUPER 1900-3i-type pavers with an AB 500 TV Extending Screed. As is usually required on race track job sites, paving had to be performed by the “hot to hot” method.
André Felchner, head of application technology at VÖGELE, personally accompanied preparations and asphalt paving operations. “It’s for precisely these kinds of complex task that we are here. With such an extreme race track as this one, of course, there are a great many things to take into account to ensure that asphalt paving and compaction are successful,” says Felchner. “Which makes it all the better when you meet such competent and motivated paving teams as this one. The guys soon grasped what was important.”
“We were perfectly aware that we can rely on VÖGELE technology, but paving would not have been possible without the consulting services and on-site support provided by the WIRTGEN GROUP.”
Mark van Kessel, Construction Manager at Gebr. Van Kessel B.V. (on the right, with Roel Vissers and Ivo Lakerveld, both from WIRTGEN Netherlands, and André Felchner, Head of Application Technology at VÖGELE)
In spite of the spectacular profile, the VÖGELE machine needed only minor modifications to pave the sloping bends. “In order to achieve a high-quality, precompacted result at this extreme incline, we simply had to produce a slightly negative crown”, commented André Felchner from VÖGELE, demonstrating one of the benefits of the AB 500 Extending Screed. In this process, the Screed Assist option, which can be separately adjusted electronically, ensured that there was sufficient pressure acting on the mix in the upper outside paving area. Screed Assist is one of the functions of SUPER pavers which allows a high-quality result to be achieved even in complicated paving situations.
The fact that all those involved in the project were extremely pleased with the outcome of the asphalt work made it a complete success for the whole Royal VolkerWessels team. An even greater compliment was the smile on the faces of the drivers participating in the first race on the modernized Zandvoort track just a week after the sign-off inspection. “Everything worked exactly as we had anticipated in cooperation with our partners from the WIRTGEN GROUP. That makes us feel as if we can count on this kind of support when we next undertake a comparatively difficult project”, says construction manager Mark van Kessel.