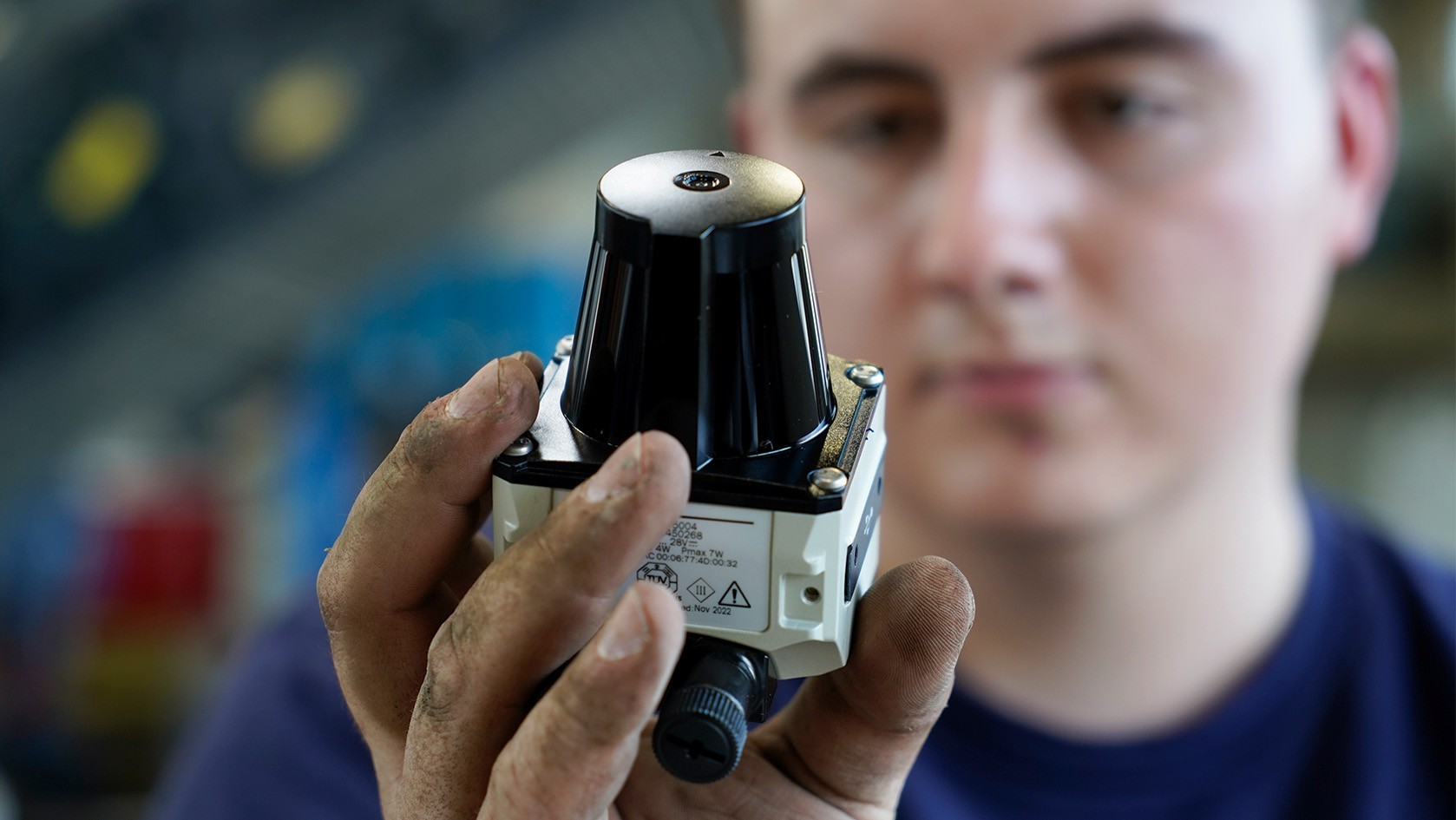
Technology upgrade for automatic tracking of milling performance
The Wirtgen Performance Tracker now allows the precise assessment of machine efficiency with the aid of relayed job information. Already operational compact and large milling machines can now also be retrofitted with innovative performance tracking technology – and that in a remarkably short time. Thanks to smart hardware and software solutions, retrofitting can be completed within a single working day.
The innovative WPT – Wirtgen Performance Tracker is a comprehensive system for the measurement and documentation of the area performance achieved by cold milling machines. The tracking system uses a laser scanning to determine the cross-sectional profile to be milled. The area milling performance and milling volume are then precisely determined using GNSS positioning and other sensor systems. Users benefit from the continuous analysis and clearly structured presentation of the measured data. In this way, WPT delivers valuable information about ongoing construction projects in real-time. The panel on the operator’s platform shows the machine operator the milling data determined by the system. After completion of the milling work, an automatically generated report with all relevant performance and consumption data is emailed to the machine owner in Excel and PDF format.
The compact and easily integrable design of the system makes it possible to quickly and easily retrofit already operational machines.
With the Performance Tracker, Wirtgen has developed a solution that, for the first time, makes it possible to precisely and reliably document the actual milling work performed in the course of a project. This brings enormous benefits for both operators and machine owners With regard to monitoring in the course of a milling job and as proof of performance after project completion, many users can now hardly imagine ever having worked without WPT.
WPT also helps to make processes such as job costing and billing faster and less time-consuming. As a rule, these processes take much longer without the Performance Tracker, while, in contrast, WPT delivers the desired results on the same day. All relevant data are available and billing can take place only a very short time after completion of the work on the construction site.
And this saves time and money. Thanks to WPT, manual measurement is no longer necessary after completion of the milling work.
WPT enables an extremely precise assessment of machine efficiency on the basis of the relayed data and information:
We are seeing increasing interest in retrofitting machines with WPT throughout the construction industry. For instance, STRABAG and SAT Straßensanierung GmbH, two members of the STRABAG SE company group, are already taking advantage of the benefits of Wirtgen technology. The European construction services provider is planning group-wide digitalisation of its existing fleet of cold milling machines to ensure that it is ready to take on all the challenges the future has in store. All new milling machines operated by STRABAG are therefore already fitted with Performance Tracker. A retrofitting programme for their existing machines has also already been initiated.
René Bordt’s team also uses the Performance Tracker. ‘It has already helped me to clear up a couple of misunderstandings here and there’, explains the Branch Manager at SAT Straßensanierung GmbH.
‘It has already helped me to clear up a couple of misunderstandings here and there.’
René Bordt, Branch Manager, SAT Straßensanierung GmbH, reporting on his experiences with the Performance Tracker.
In the past, the integration of WPT was offered as an optional extra when purchasing a new milling machine. Today, however, all compact and large milling machines can be retrofitted with the Performance Tracker at any time in a simple and uncomplicated process. The WPT system features precisely coordinated system components – a TCU (Telematic Control Unit), a receiver for GNSS satellite-based positioning and one or two laser scanners. In addition to this hardware, the full WPT package includes a comprehensive software suite, a licence for the use of GNSS data and authorisation for accessing the Wirtgen Group telematics system.
WPT is available for milling drum assemblies with milling widths from 1,000 mm.
Ideally, retrofitting WPT can be carried out at times when operational demands on machines are not so high. This enables the optimised machines to make a fresh start in the new season. As retrofitting involves only relatively short machine downtimes, it can actually be performed at almost any other point in time. In general, the installation of WPT can be completed within the space of just one working day, which means that retrofitting can be carried out at relatively short notice.
Would you like to learn more about the numerous advantages of using the Wirtgen Performance Tracker? If you would, arrange an appointment with your local or regional Wirtgen Sales and Service organisation or dealer now to discuss your specific needs. Click here for our list of contacts
A quick and easy technology upgrade with enormous benefits for you. WPT enables extremely accurate assessment of your machine’s efficiency, the performance it delivers, and precise information on ongoing progress in the course of your project.
WPT is now also available for WR series machines
The advantages of the Wirtgen Performance Tracker are now also available to users of WR series machines. In addition to recording all job-relevant parameters such as the working width and depth, a particular advantage is the precise documentation of the quantities of binding agent and water added during milling at each location and the registration of the cuts already mixed, including overlaps with adjacent cuts. WPT enables fast, precise, and time-saving job costing in combination with these models, too.