- Construction company
- Kutter GmbH & Co. KG
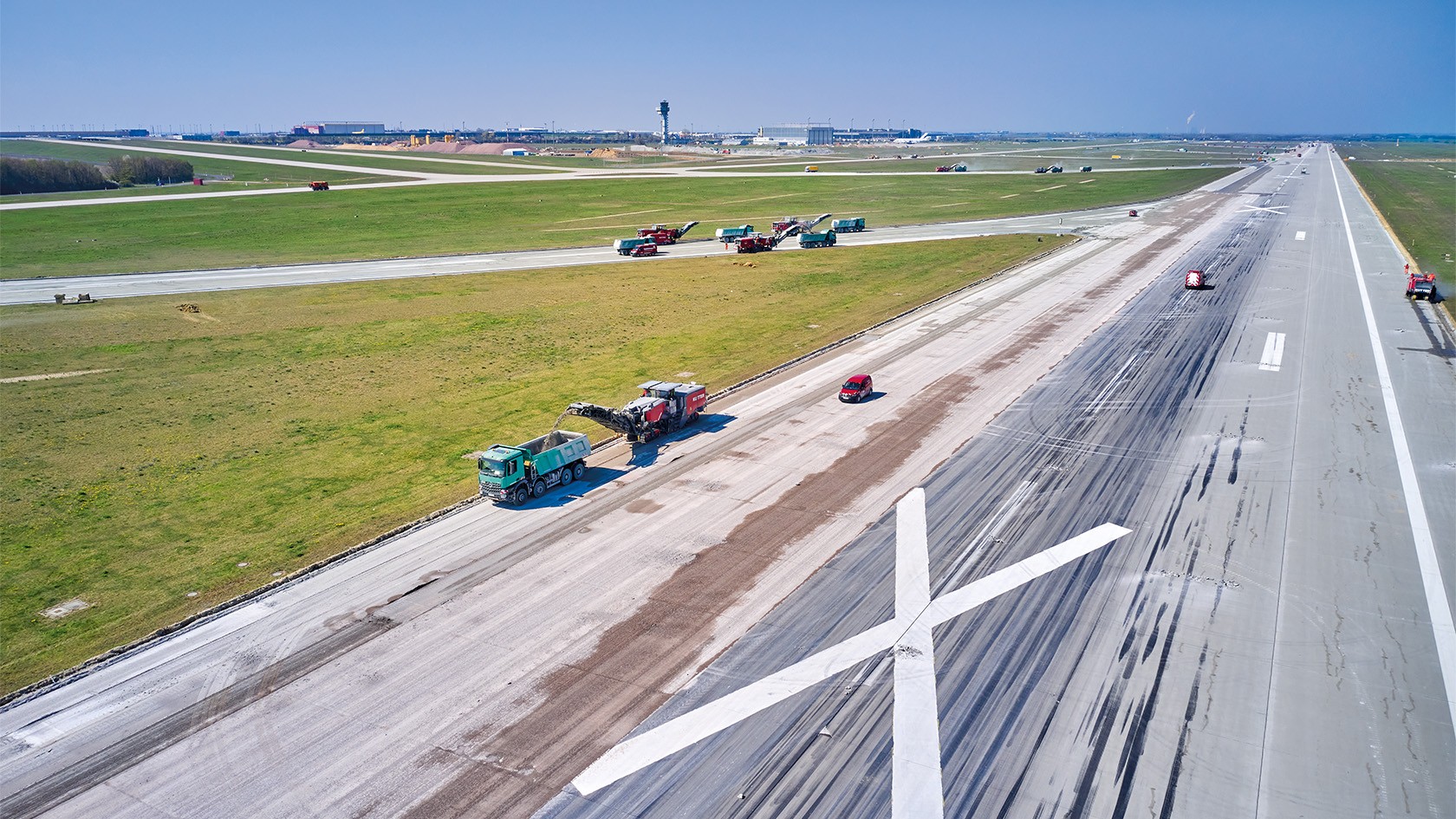
A total of 15 cold milling machines were deployed on one of the world’s biggest ever milling projects
Leipzig | Germany – a project of this magnitude is anything but normal, even for the experts from German contractor Kutter GmbH & Co. KG. In the course of the refurbishment of Leipzig/Halle Airport by Kutter GmbH & Co. KG, the first phase of the project involved the complete removal of the concrete of the north runway and the associated taxiways within 30 days. The resurfacing could only begin after the completion of this first phase. 350,000 tonnes of extremely hard concrete reinforced with steel rebar mats (Continuously Reinforced Concrete Pavement - CRCP) had to be removed by this cutting method – a battle against time and tonnage.
Concrete milling is already an established technology on projects around the globe. These days, thanks to technological advances, almost all hardnesses and grades of concrete pavement can be cost-efficiently removed. This has been clearly demonstrated in countless successfully completed concrete milling projects. Specially modified cold milling machines and many years of systematic development in the field of expendable cutting tools guarantee high productivity and efficiency when milling in hard concrete. The removal of reinforced concrete pavements containing tie-bars, dowels and rebar mats is also possible. At the same time, selective removal enables the separation of concrete layers with different properties and, consequently, also the reduction of contaminated material. What’s more, the method offers further benefits in terms of environmental protection: As a rule, milled concrete can be recycled without any further treatment. The vibration-free procedure is characterised by low noise and low dust emissions and fulfils all official building regulations, economic provisions and other relevant requirements.
The complete removal of the surface of the north runway at Leipzig/Halle Airport in spring 2021 is one of the world’s largest known concrete milling projects. The reason for the need to resurface the 3,600 m of runway and associated taxiways was so-called ‘concrete cancer’: This is an alkali-silica reaction, as also encountered on older concrete-paved motorways, which irreparably destroys the concrete from within. The reaction occurs when aggregate constituents used in the production of the concrete come into contact with water and release too much silica. The silica reacts with the cement contained in the concrete and forms a gelatinous mass. The reaction causes expansion of this mass to the extent that it begins to exert pressure within the concrete. After some time, this ultimately leads to explosive destruction in the ‘infected’ parts of the concrete.
Removal of the concrete surface layer irreparably damaged by ‘concrete cancer’ with a Wirtgen W 250 Fi.
A project of this magnitude requires high-performance machines and optimal cutting tools for the milling drum. With over 1,000 hp, the Wirtgen W 250 Fi class always has sufficient power reserves when the going gets tough. The large milling machines were equipped with additional ballast weights to ensure optimal exploitation of their performance for the cutting process. The higher operating weight leads to greater traction of the track units and optimal cutting performance of the milling drum. The large milling machines for the Leipzig Airport project were also fitted with ECO milling drums and special picks. ECO milling drums are fitted with up to 50 per centfewer picks at larger tool spacings than is the case with standard milling drums. The lower number of cutting tools reduces cutting resistance, which also makes it possible to mill harder concrete pavements.
The powerful and efficient milling fleet removed 350,000 t of concrete in only 30 days. This meant that each machine had to mill off an average of over 1,100 t concrete a day. The first step here was the fastest possible removal of the concrete surface in layers. After this, machines equipped with extremely accurate 3D levelling technology were used to mill to the specified target height with sufficient precision to achieve an optimal base for the subsequent resurfacing. It must be said that a project like this needs more than just the right fleet for the job and efficient logistics – namely a perfectly coordinated and extremely capable team. A total of around 60 employees from Kutter worked on the project in two shifts to ensure a successful outcome of the battle against time and tonnage and meet the deadline.
‘In order to get through this challenging project and deliver within the tight deadline, we constantly had ten (and sometimes fourteen) W 250 Fi class large milling machines working simultaneously in two shifts. We also always had another five identical backup machines on-site as reserves.’
Bernhard Fischer, Project Manager and Branch Manager at Kutter
Hard at work – even on rainy nights.
The planning of the project began at an early stage to assure a smooth and seamless process chain. In August 2020, a whole eight months before the project start, the specialists from Wirtgen and Kutter began conducting a series of practice-oriented tests. The technical experts agreed on the type of round-shank pick required to achieve optimal milling performance and long service life of the cutting tools. This enabled precise consumption estimates for picks and other wearing parts and the procurement of sufficient stocks that were stored at the site. This enabled the minimisation of machine idle times for changing picks and maintenance, which, in turn, assured maximum productivity.
‘The Wirtgen Customer Support team lived up to its excellent reputation. From day one, the advice they gave us here covered all aspects of the project, and they worked hand-in-hand with us to arrive at the perfect solution.’
Bernhard Fischer, Project Manager and Branch Manager at Kutter
Granulated concrete produced by recycling is a valuable building material that can be fully reused. The 350,000 t of concrete removed during the airport project in Leipzig was temporarily stockpiled close to the project site and completely recycled for use in the subsequent project phases as the base layer for the new runway. Short haulage distances and simultaneously minimal new material requirements enabled low specific diesel fuel consumption and, in turn, a favourable carbon footprint.
On top of this, the Wirtgen cold milling machines themselves offered a broad spectrum of environmentally friendly machine technologies. Consumption-optimised speed ranges in milling mode controlled by Wirtgen Mill Assist and engine-temperature-controlled fan speeds, for example, help protect the environment and conserve valuable resources Automatic activation and deactivation of the water spraying system and milling-performance-dependent water metering considerably reduce the specific water consumption.
The temporarily stockpiled milled material was fully reused for the base layer of the new runway.
The large-scale runway rehabilitation project at Leipzig/Halle Airport delivered optimal results and was successfully completed within the allotted timeframe. The preconditions for this were the timely completion of the concrete milling phase and optimal milling results.
Project Manager Bernhard Fischer expressed his satisfaction with the successful completion of the project: ‘In contrast to milling in asphalt, the enormous hardness of the concrete here meant that we had to take slower milling speeds into account. The wear on the milling tools was also significantly higher. In spite of this, our previous experience from similar projects enabled us to continuously optimize the process. And, thanks to the outstanding evenness of the milled surface, it was ready for resurfacing right away. The additional costs of increased wear on material was more than compensated by the rapid progress we made and the precision of the results. Removal of the concrete by cold milling was the ideal method for this project’.
You can find more information about Wirtgen cold milling machines on our product pages.
Press/media kit
Click here to download a ZIP file containing the press release in the available languages in Microsoft Word format and the images in 300 dpi resolution.
Download