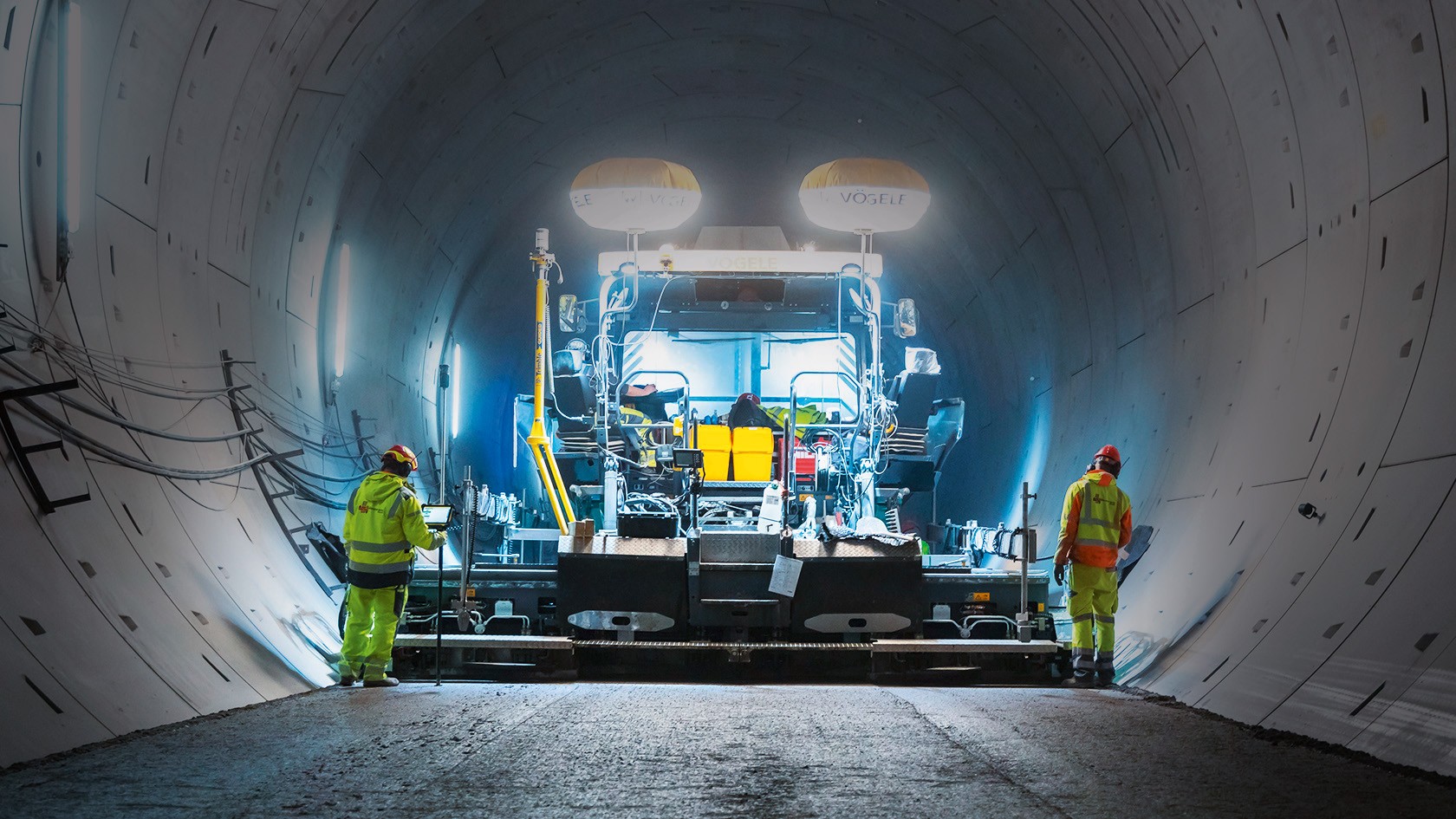
Large-scale project in one of the longest rail tunnels in Germany: in combination with the MT 3000-2i Offset material feeder the SUPER 2100-3i Road Paver built a slab track on the Stuttgart-Ulm section. The requirements on this 6-layer structure were demanding.
Five water-bound base layers, stringent requirements on evenness and logistical challenges: paving a slab track in two 8 km-long tunnel bores of the Deutsche Bahn’s Stuttgart-Ulm project was tough. The paving team met the challenge with the SUPER 2100-3i including the AB 600 TP2 High Compaction Screed and 3D control system. An MT 3000-2i Offset material feeder supported job site logistics.
Road construction projects in rail tunnels are particularly demanding. On the one hand, the cramped job site situation requires perfectly integrated logistics. On the other, the requirements on the track bed are huge: high-speed sections have to be absolutely even and withstand extreme loads. This is because Deutsche Bahn trains are not only running at higher and higher speeds, they are also becoming longer and running more frequently.
This is why a slab track was to be paved in the Albvorland Tunnel, which is 8.176 m long and is a section of the Deutsche Bahn’s Stuttgart-Ulm rail project designed for a speed of 250 km/h. Slab tracks generally consist of an anti-freeze layer, a water-bound base and a layer of concrete or asphalt; they can withstand much higher loads, have a longer service life and are virtually maintenance-free compared to ballast beds.
Layers built up to a total thickness of 137 cm: the SUPER 2100-3i paved the slab track in six passes consisting of water-bound base and a roller-compacted concrete layer.
The structural requirements for the Albvorland Tunnel slab track were even more stringent than usual: construction service provider Implenia Construction GmbH München appointed contractor Kurt Gansloser GmbH to pave five water-bound base courses each 25 cm thick and a roller-compacted concrete layer 12 cm thick in the two single-track tunnel bores and in another section some 3 km long. Pave width was 6.5 m. The aim was to raise the base of the tunnel to the desired level and to create a particularly low-settlement foundation for sleepers and rails. At the same time, this also helps Deutsche Bahn ensure that rail operations cause no damage to the cables underneath.
The six layers form a total thickness of 137 cm
“On projects like this, each cog needs to mesh with the next. Precise planning, a competent team and powerful machines are essential”, says Christopher Gansloser, managing director of Kurt Gansloser GmbH. “Of course, the subject of emissions plays an important part on tunnel job sites, in particular.” This is why the civil engineering specialists put their faith in Vögele’s SUPER 2100-3i large paver. This Highway Class machine has a laydown rate of up to 1,100 t/h and with its modern drive concept, is perfect for projects involving tunnels. The engine is fitted with a multi-stage exhaust emissions after-treatment system including a diesel particulate filter, and thus meets the strict guidelines of European exhaust emissions standard stage V. Intelligent engine management and the so-called EcoPlus package furthermore reduce fuel consumption and emissions by up to another 25%.
The SUPER 2100-3i also scored as a result of its straightforward operation and clear controls. In spite of the cramped conditions and meagre tunnel lighting, drivers and operators had a good view of all the relevant areas of the machine and the job site. This is on the one hand due to the glare-free backlighting of the ErgoPlus 3 consoles; whilst on the other, LED lights in the machine’s hardtop, additional light balloons and LED spotlights in the screed operator’s consoles ensured comprehensive illumination of the entire area of operation.
“On projects like this, each cog needs to mesh with the next. Precise planning, a competent team and powerful machines are essential.”
Christopher Gansloser, Managing Director of Kurt Gansloser GmbH
To guarantee a high-quality paving result, Kurt Gansloser GmbH relied on the AB 600 Extending Screed. The screed can be extended hydraulically up to 6 m and had bolt-on extensions added to reach the width of 6.5 m required by the tunnel bores. In order to achieve maximum precompaction in all five layers, the team used the TP2 variant of the AB 600 with tamper and two pressure bars. Vögele pressure bars controlled by pulse hydraulics are unique in the market and allow precompaction values of up to 98% to be achieved. This allowed the paving team to achieve high paving quality and efficiency across all layers and to save time in the subsequent passes with the HD 10 VT and HD 13i VV tandem rollers from HAMM.
The quality standard required for the track bed also demanded the grade and slope control of the screed to be accurate to the millimetre. The tolerance range for the absolute position of the 12 cm-thick roller-compacted concrete layer was just ± 10 mm. In order to maintain this accuracy exactly, the contractor relied on the Navitronic Basic 3D control (which does not use a tensioned wire) for paving the water-bound base layers. The Vögele system has an open interface to which positioning systems from a variety of manufacturers can be connected.
Kurt Gansloser GmbH used the Trimble control system. A tachymeter control measured the positions and angles of the screed and calculated deviations. The interface passed these on to the Vögele Niveltronic Plus System for Automated Grade and Slope Control which made the necessary corrections. To even out the final undulations, the team used the Big MultiPlex Ski sensor system from Vögele for the roller-compacted concrete layer. “This enabled us to maintain the tolerance easily and we are very pleased with the result,” said Gansloser.
“The material feeder increased efficiency and quality enormously and saved us a lot of time.”
Christopher Gansloser, Managing Director of Kurt Gansloser GmbH
Delivery of mix was a particular challenge. Approximately twelve trucks a day, each carrying around 20 t of mix, had to reverse into the tunnel bore to transfer the mix. Complex engineering work was being performed on the tunnel in parallel, making the logistics even more complicated. “In some cases, these were situations which were difficult to plan, so we had to get used to it all first,” said Gansloser. “After just a short time, though, we were able to pave virtually without interruption.” This was due on the one hand to the short distances to the mixing plant on site and on the other, to the Vögele MT 3000-2i Offset material feeder. The PowerFeeder has a conveying capacity of up to 1,200 t/h and ensured a continuous, smooth transfer of mix to the paver. “The material feeder increased efficiency and quality enormously and saved us a lot of time”, says Gansloser. “The job site ended up being the ideal interaction between client, planner, paving team and machines.”
Highlights of Vögele’s SUPER 2100-3i Universal Class paver