The motorway section between Mandal and Kristiansand is part of a gigantic construction project for better access to the west coast of Norway. The new Benninghoven RPP 4000 plant is located directly at the Mandal Fjord in Brennevinsmyra and has its own jetty. Norway’s most innovative, environmentally friendly and modern asphalt mixing plant has been in operation since August 2021. Equipped with a recycling drum with a hot-gas generator using counterflow action, it allows for up to 100 % recycling material to be added while complying with the standard emission limits. A stroke of luck for the owner Velde Produksjon, as the new plant with these features is pioneering for the future of asphalt production in Norway and therefore particularly economical.
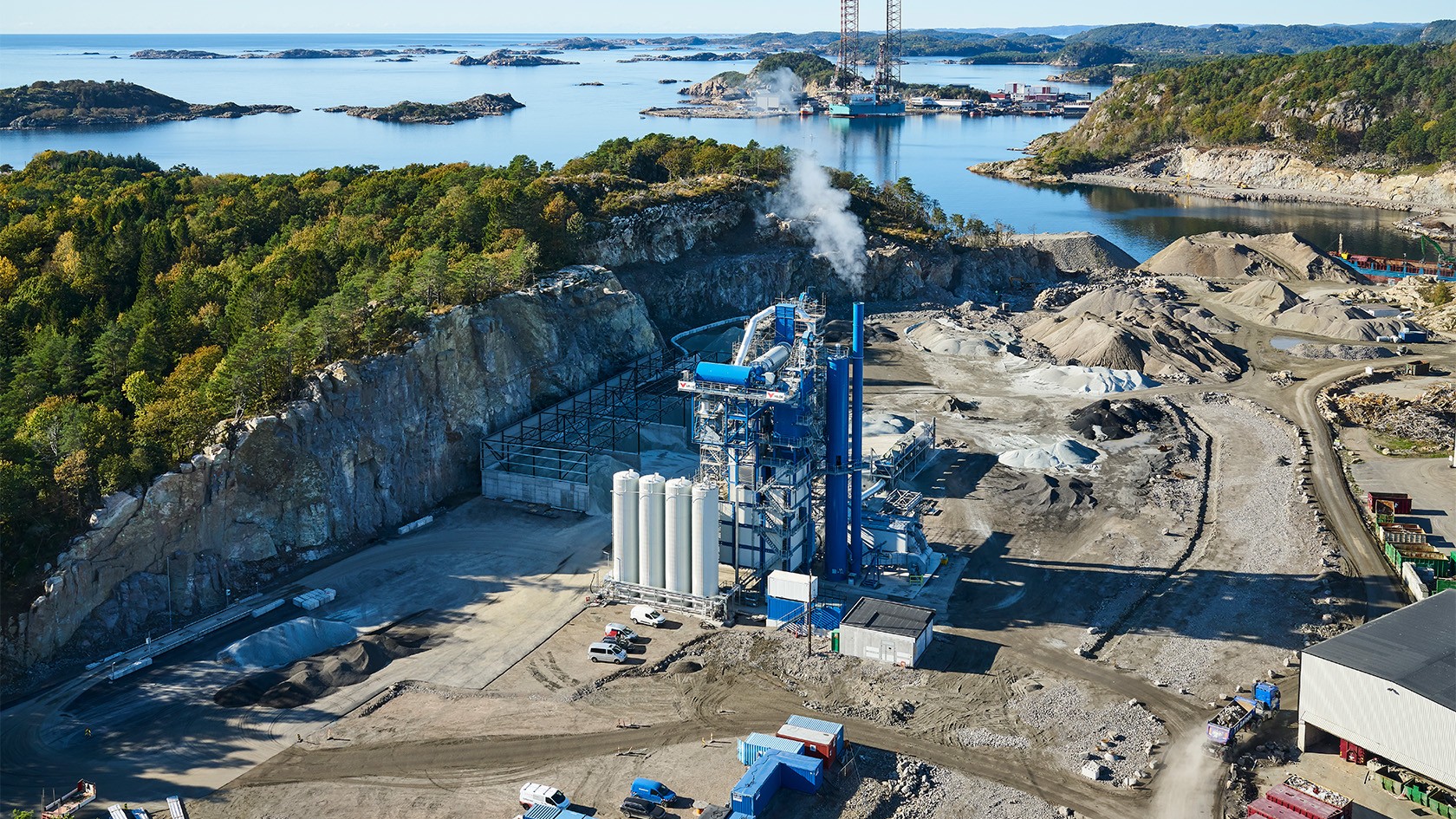