The Abuja-Kaduna-Zaria-Kano Road (AKR) is a part of ‘Trans-African-Highways’, a network comprising transcontinental road construction projects in Africa. The aim of the project is the stimulation of the African economy through the construction of a well-developed network of road-based trade corridors. The redevelopment of the highway establishes better connections between the economically weaker north of the country and the stronger regions in the south.
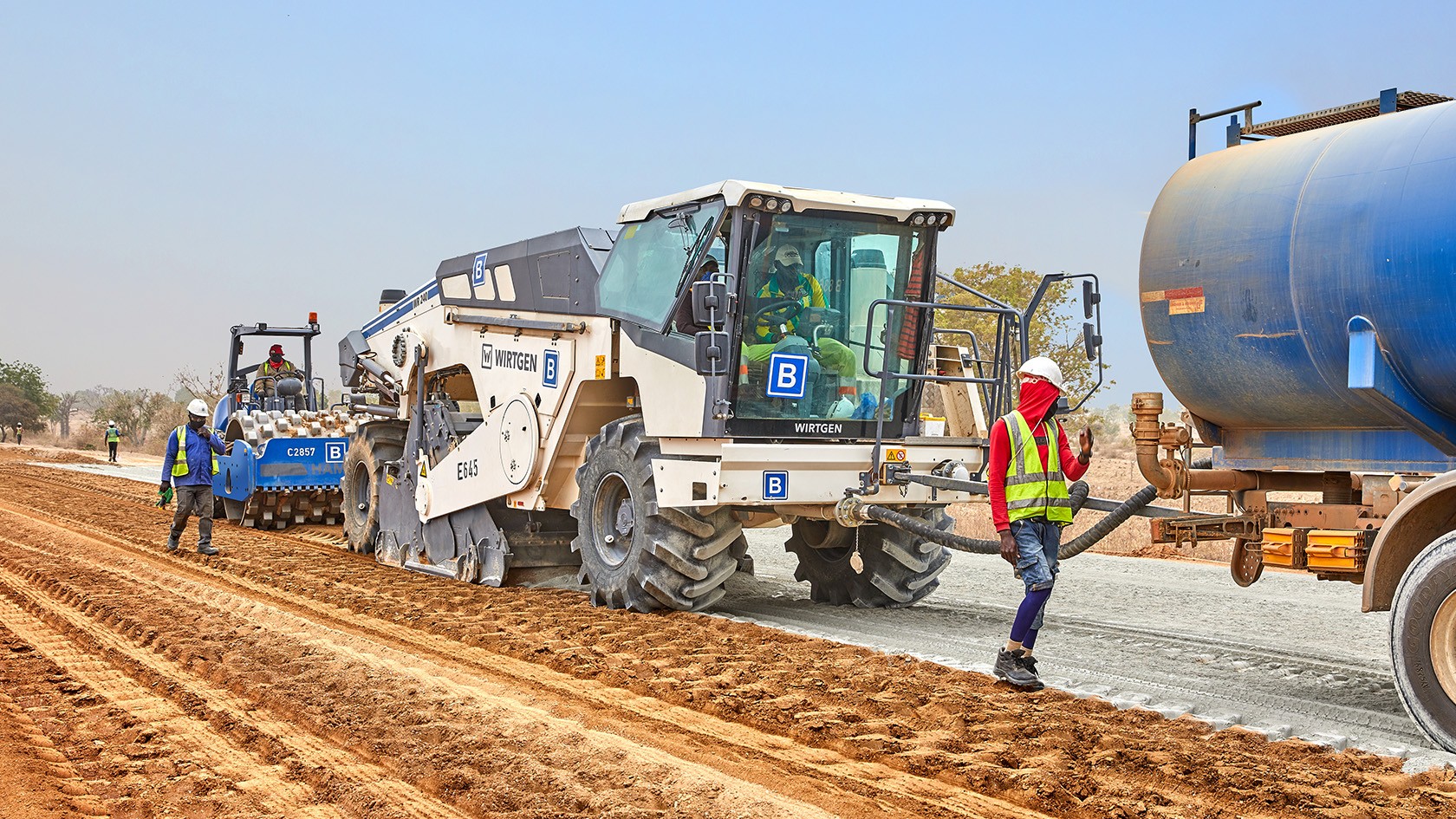