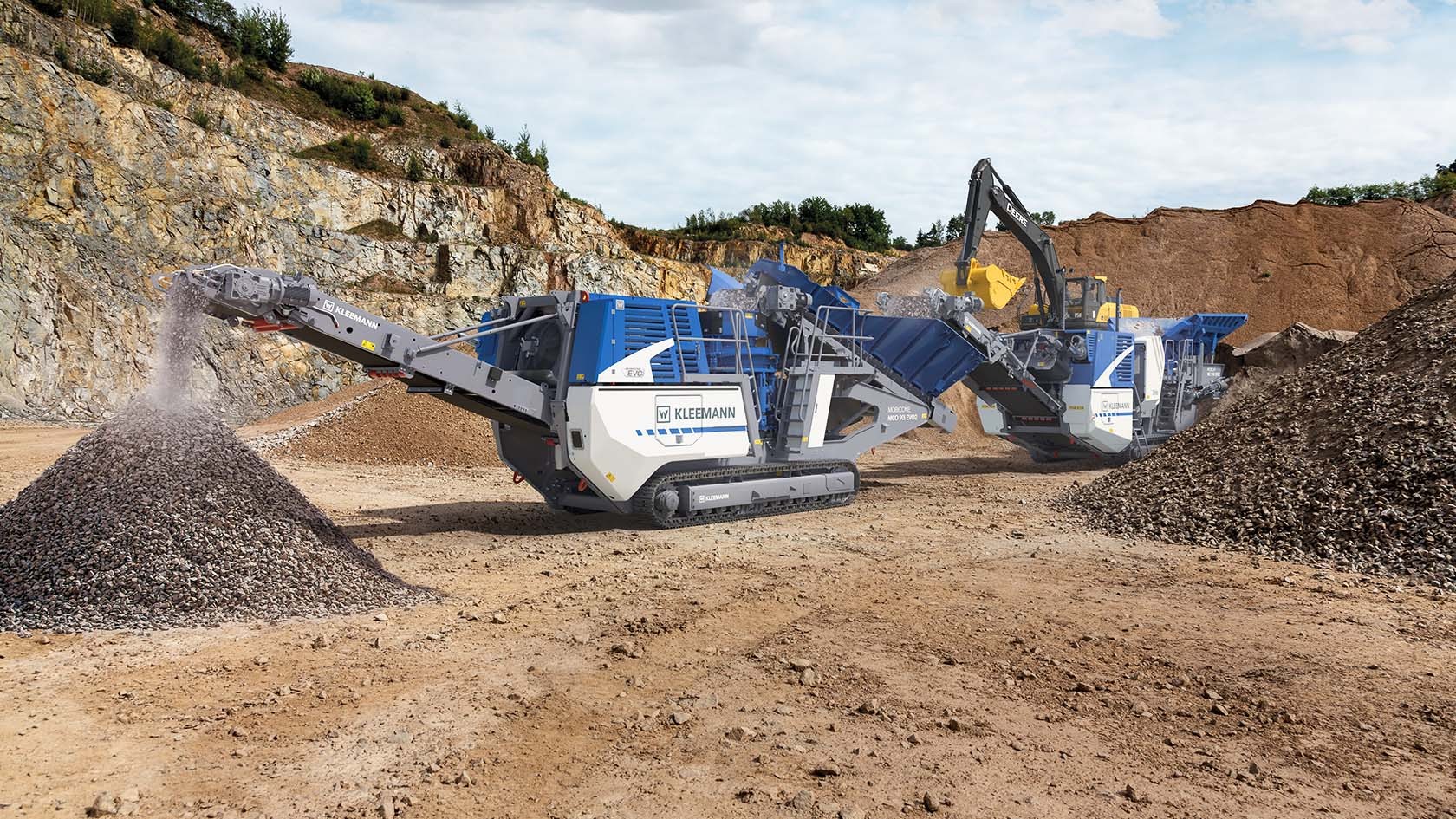
Kleemann presents two new crushing plants of the EVO2 generation: the jaw crusher MOBICAT MC 110(i) EVO2 and the cone crusher MOBICONE MCO 90(i) EVO2. The mobile crushers are often used together in the first and second crushing stage. Thanks to innovative features such as the optimised operating concept SPECTIVE and innovative overload systems, they now operate even more efficiently and economically.
The mobile plants have been developed for applications in the medium output segment in quarries or in recycling and contracting companies. During the development, Kleemann placed an emphasis on intelligent support for users – and created digital innovations with added value. Whenever rapid readiness for operation, efficient crushing and flexible use is required – this is precisely where the MCO 90(i) EVO2 and the MC 110(i) EVO2 demonstrate their strengths. There is a good reason why they line up as a team in natural stone applications all over the world: the coupling and the output levels tuned to one another.
Mobile plants have gained the reputation of being particularly economic. Particularly in the most important discipline - the efficient handling of fuel - the two crushing plants both raise the bar higher once again. The reason: the improved diesel-direct drive concept.
The cone and jaw crushers work efficiently together thanks to the innovative line coupling. The coupling combined with the tuned output levels guarantee a smooth, continuous material flow through both plants. The technology behind this: Continuous Feed System (CFS). It uses ultrasonic sensors to monitor the crusher level and other parameters and, at the same time, optimises the performance – for both plants simultaneously thanks to the line coupling.
Kleemann has also integrated a whole series of innovations in the crushing plants of the EVO2 generation which make operation even more economic and user-friendly. Apart from the new overload systems and the SPECTIVE operating concept – new with the digital application SPECTIVE CONNECT – the improved diesel-direct drive with output-dependent fans guarantees cost-effective operation. It improves the cooling capacity, only runs when required and reduces the fuel consumption for both increased economy and ecological efficiency.
Kleemann has significantly simplified operation once again with the intuitively structured SPECTIVE operating system for the new EVO2 generation.
From the starting procedure to the elimination of malfunctions and on to maintenance – on its 12" touch panel, SPECTIVE provides users with all important plant information in a clearly arranged manner and makes all plant settings from a single location possible. The further developed version optimises user comfort through the arrangement of the buttons below the display. The lockable operating mode cabinet protects against misoperation.
The new overload systems of the EVO2 machines pursue an important goal: increase in the operational readiness of the plant in a sustainable manner by guaranteeing a process that is as continuous as possible. The cone crusher MOBICONE MCO 90(i) EVO2 uses the Ringbounce Detection system. This protects the crusher against damage. The cone crusher itself always places the focus on product quality. Operating companies and users still can decide, however, whether more oversize grain is permitted in favour of a higher output. The software-supported overload system has two modes – one for high output and one for top quality.
In the jaw crusher MOBICAT MC 110(i) EVO2, the overload system intervenes with uncrushable material. If the feed material contains uncrushable objects such as metal parts, the overload system becomes active to prevent damage to the plant. It thus counteracts a blockage without any form of operator intervention. In case of such overloads at selected points, the crushing gap (CSS) opens automatically within its setting range. The optionally available active overload system ensure an even faster reaction and opens the crushing gap for a short time at a speed up to 40-fold faster.