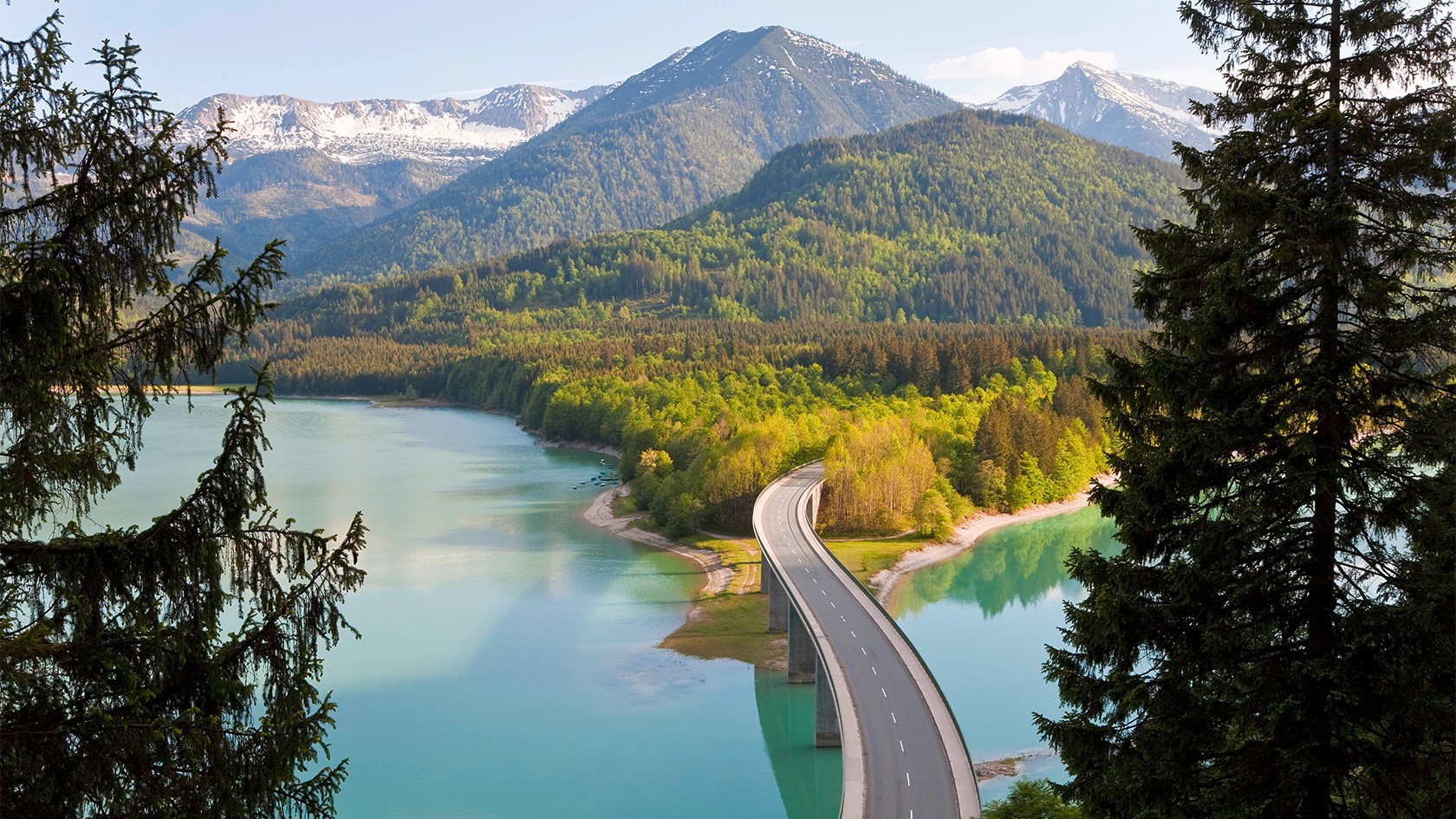
Machine manufacturers and construction companies around the globe are currently searching for ways to achieve the ultimate goal of climate-neutral construction. The challenge here is to successively reduce CO₂ emissions as well as other harmful gases (expressed as a CO₂ equivalent: CO₂e) to zero globally over the coming decades. In the road construction sector, this transformation is inextricably linked to the improvement and further development of production and working processes. In the future, machines and construction materials will also be assessed on the basis of the climate-harmful emissions arising from their production and use. The focus is, however, not on individual machines, but on the entire process leading up to the finished product – a road. Ultimately, it is the emissions generated per mile of newly built or rehabilitated road – CO₂e per unit of work done – that are decisive.
Sustainable development goals
In 2015, the United Nations adopted Agenda 2030. With the agenda, the global community aims not only to enable people on all continents to live a life in dignity but also to sustainably conserve vital natural resources. Economic, ecological, and social aspects all play a critical role in this. Governments around the world, civil society, and private enterprise are called upon to make a contribution to the realisation of the Sustainable Development Goals set out in Agenda 2030.
The construction industry already faces specific on-site requirements with respect to the use of non-fossil fuels or the deployment of machines with local zero emissions – in the Nordic nations, for instance. In the light of this and their obligations to future generations, many leading players in the construction sector and numerous small and mid-size companies are currently setting their own goals to mitigate climate change.
The Greenhouse Gas (GHG) Protocol has established itself globally as a holistic calculation method for CO₂e emissions. In a similar way to business accounting, it enables companies and institutions to systematically determine their emissions with harmful effects on the climate and to identify their sources.
As a manufacturer of road construction machines, the Wirtgen Group has also set itself concrete goals, broken down into specific steps. For example, Wirtgen, Vögele, Hamm, and Kleemann will further increase the availability of machines powered by hybrid or fully electric drive systems by 2026. In addition, all Wirtgen Group product brands, including Benninghoven, will offer machines and plants that can be operated with non-fossil or climate-neutral fuels. Last but not least, the digitalisation of machines will make a significant contribution to process optimisation and, in turn, lead to a further reduction of harmful emissions.
Benninghoven asphalt mixing plant with a hot gas generator for the production of asphalt from up to 100% milled material.
The ultimate goal of all these measures is a considerable reduction in the carbon footprint of Wirtgen Group machines, plants, and systems by 2030. In concrete terms, the aim is to reduce scope 1 and scope 2 emissions by over 50%. For scope 3, we plan to reduce upstream and downstream emissions by at least 30%. These primarily include the emissions from machines throughout their service life and, for example, emissions arising along the supply chain. To this end, John Deere, the parent company of the Wirtgen Group, has joined the Science Based Targets initiative (SBTi) and has had its own goals assessed and validated.
In order to achieve the greatest possible reduction in overall emissions, it is essential to focus the efforts of all players across the road construction industry. The key question we must ask ourselves is: How can we construct or rehabilitate roads with minimal or zero harmful emissions?
CECE is a pan-European organisation representing construction machine manufacturers and related industries They have identified 4 areas in which CO₂e emissions can be reduced: (Source: CECE)
A holistic approach that takes all aspects of road construction into consideration is essential in order to achieve maximum reduction of CO₂e emissions. As the pan-European organisation representing construction machine manufacturers and related industries, the CECE has already proposed a number of courses of action. Considerable savings potential can be leveraged by further improving machine efficiency, by optimised construction processes and procedures, and by means of more-efficient operating concepts. At the same time, alternative, non-fossil fuels and electric drive systems can play an important role on the road to climate neutrality.
The CECE 4-pillars approach
The Wirtgen Group has already developed numerous solutions over the years to significantly reduce fuel consumption. These include intelligently-designed drive systems and efficiency-optimised controls. One example of this is the Wirtgen ”Mill Assist”: an assistance system for cold milling machines that automatically adjusts to meet the performance and quality requirements entered by the machine operator and consistently guarantees the most favourable balance between milling performance and operating costs. This simultaneously reduces diesel fuel consumption and minimises pick wear. Another example is the Dash 5 generation of road pavers from Vögele, which feature environmentally-friendly machine technologies that also ensure lower fuel consumption.
Machines from Wirtgen, Vögele, Hamm, and Kleemann whose engines fulfil the requirements of the US EPA Tier 4f exhaust emission standard or EU Stage V can already be powered by alternative fuels. They are approved for use with alternative paraffinic fuels such as HVO (Hydrotreated Vegetable Oils – fuels on the basis of vegetable oils or animal fats) or XtL fuels (X-to-Liquid – synthetic fuels on the basis of solid, liquid, or gaseous energy resources). There are already corresponding solutions for asphalt mixing plants from Benninghoven. These can be fuelled with wood dust or BtL (Biomass-to-Liquid – liquid fuels derived from biomass).
The holistic assessment of a construction site and the methods used necessitates a consideration not only of the emissions from individual machines and/or plants, but also of all the emissions that arise or will arise in the production of the construction materials and mixes and in their transportation to and from the construction site.
To illustrate CO₂e reduction potential through the use of recycling technologies, the graph below shows the emissions from a variety of construction methods used for the rehabilitation of the surface layer and binder course of a single-lane roadway. In all of these cases, we have assumed that the construction machines and transport vehicles use B7 diesel fuel and that the asphalt mixing plant is fuelled by lignite dust. The transport distances reflect typical distances between mixing plants and construction sites.
The left column depicts emissions from conventional methods: Existing material is milled off and removed from the site before a new surface is paved with an asphalt mix produced entirely from fresh material. Calculations of emissions show that the major proportion arises in the production of the asphalt mix and in the manufacture of the materials this process requires.
In the centre column, you can see the new proportions once 80% of the asphalt mix is made of recycled material, that is, re-used milled material. Modern asphalt mixing plants are already capable of producing such material, and Retrofit solutions are available for existing plants as well. This, in itself, reduces CO₂e emissions by an impressive 27%.
Reductions are even greater if the construction materials are not heated before processing. As the column on the left shows, this is where a large proportion of CO₂e emissions arises. Tried-and-tested alternatives are already in use around the globe. The most important of these are low-temperature asphalt production and cold recycling. Cold in-situ recycling in particular consumes up to 90% fewer resources and requires up to 90% less transport movement. In the example scenario, this reduces CO₂e emissions by 43% (see right column) when building a surface layer of new material over the cold recycled layer. When completely rehabilitating the entire roadway, this method can actually reduce CO₂e emissions by up to 60% with no reduction in quality. Additional practical benefits of this method include faster project completion and longer-lasting road surfaces.
In this method for road rehabilitation, the construction materials are recycled on the spot. The asphalt does not need to be heated, so substantially less energy is required for the process.
Regardless of the measures employed, it is essential to have a transparent and verifiable system for determining and assessing emissions. This is where the tremendous opportunities offered by digitalization can play a decisive role. These days, for example, telematics systems are already able to register the fuel consumption of machines. For Wirtgen Group product brands alone, the number of machines fitted with such systems is forecast to rise to 42,000 by 2030. This will allow the documentation of such parameters under real-world operating conditions and will offer a much more realistic picture than mandatory test cycles.
Systems for the documentation of the actual work performed are now also available for the first time. These include the Wirtgen Performance Tracker (WPT) for cold milling machines and wheeled soil stabilisers/recyclers. With the aid of such digital solutions, it will be possible to document consumption figures “per work done” – i.e., on a construction site or project basis.
The WPT, Wirtgen Performance Tracker for cold milling machines records and documents how many cubic metres of asphalt have been milled. It can, among other things, also provide information about fuel consumption during a specific construction project.
Press/media kit
Click here to download a ZIP file containing the press release in the available languages in Microsoft Word format and the images in 300 dpi resolution.
Download