- Feed material
- Basalt
- Hourly output
- 145 t/h
- Feed size
- 0–400 mm
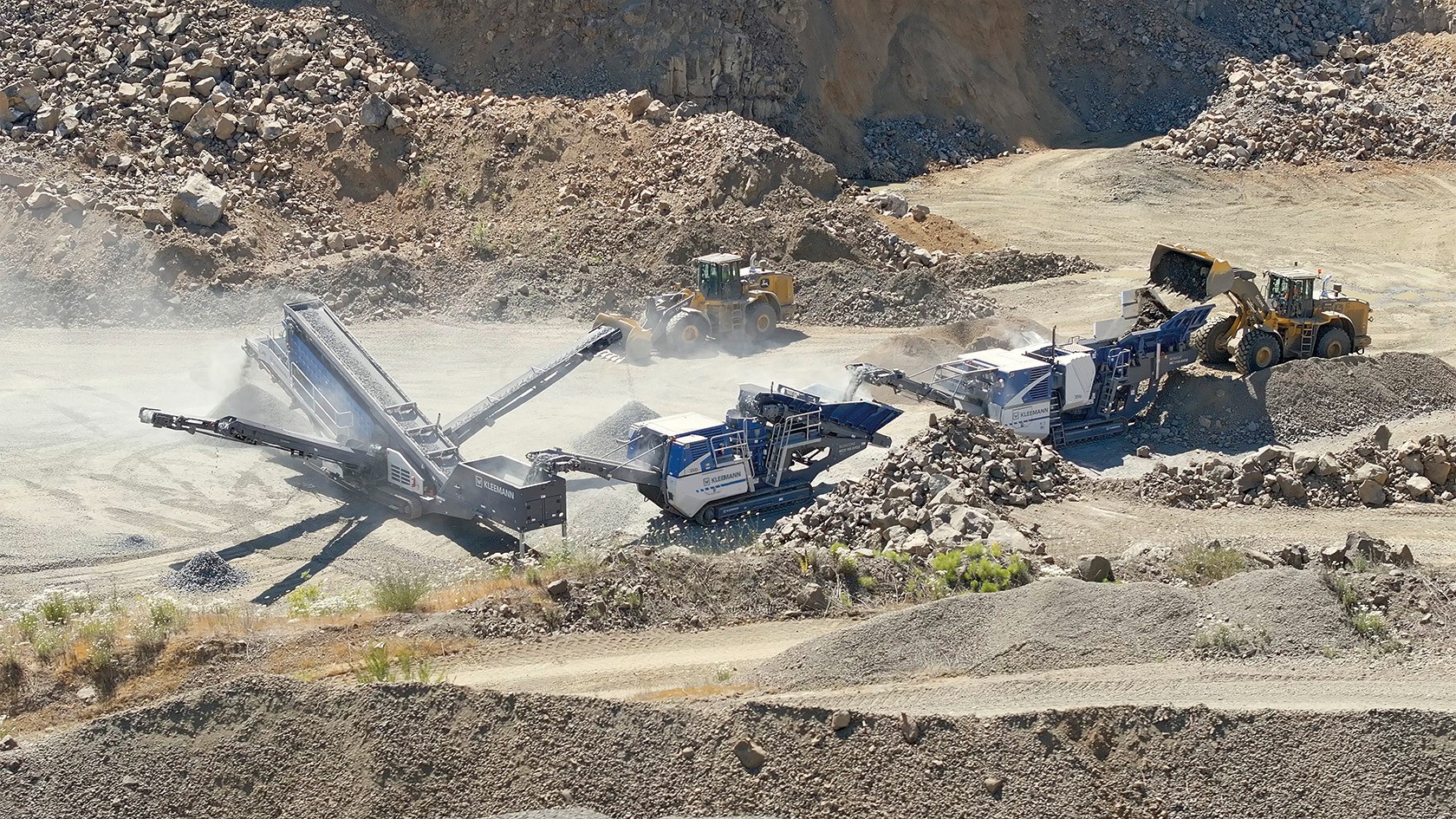
A Kleemann plant train was recently put into operation at Table Mountain Rock in Oregon (USA): The jaw crusher MOBICAT MC 110i EVO2 and the cone crusher MOBICONE MCO 90i EVO2 are combined with the MOBISCREEN MSC 953i EVO classifying screen plant. The new plant train is impressing the operators in several ways.
Table Mountain Forestry serves many areas of activity related to forestry, and forestry road building is part of the company’s application portfolio. Table Mountain Rock, a relatively new subsidiary, produces the raw material for forestry road building, among other things. The feed material is basalt in the feed size 0-400 mm, which is crushed down to small grain sizes of 0-25 mm. “With our basalt, we have a really good, dense, hard rock. And that gives us a real competitive advantage here in the coastal region,” says Kyle Humphrys, owner of Table Mountain Forestry. This application is a perfect fit for Kleemann’s linked plant train.
“Previously, it took us two weeks to move from one site to another. With the mobile Kleemann plant train, it can be done in a week. So, before the old crusher would even be up and running, we have already finished production with the new plant train. That’s huge!“, says Jake Gregg, Operations Manager at Table Mountain Forestry.
The ability to use the plant quickly and flexibly is a decisive advantage for Table Mountain Rock. But it’s not the only one. “This is a high-tech, state-of-the-art plant train. A lot less maintenance, a lot more production, and the processes are automated, which takes a lot of trouble out of the operations,” Wayne Gregg, who works directly on the machine as a user, is convinced. The intelligent linking of the entire plant via Kleemann line coupling ensures that everything works seamlessly. In the event of malfunctions or overfilling, each of the machines sends signals to the upstream and downstream machines. This automatic control and monitoring stabilises the entire process. The feed control Continuous Feed System (CFS) ensures that the crushers themselves are optimally utilised at all times.
“A lot of things can be done from a safe distance. Our people don’t have to get on the machines anymore. It makes the job a lot safer.”
Kyle Humphrys, owner of Table Mountain Forestry
Another high-tech feature is SPECTIVE. This exceptionally user-friendly operating concept developed by Kleemann can be operated intuitively. “The required settings can be entered very easily – even while the machine is running. There is virtually no downtime,” explains Operations Manager Jake Gregg. And Kyle Humphrys adds: “A lot of things can be done from a safe distance. Our people don’t have to get on the machines anymore. It makes the job a lot safer.”
The SPECTIVE operating concept allows us to change settings even with the plant running.
One of the main cost drivers in rock mining in the US is the skyrocketing price of fuel. Here, too, the company is well-positioned with the Kleemann plant train. The entire train, i.e. all three machines, run at around 60 to 75 litres per hour. “This is a really good value especially in view of the tough application. And it’s often decisive when it comes to new orders,” Kyle Humphrys continues. The machines are also easy to maintain thanks to excellent accessibility to components such as the power unit.
Overall, the low fuel and maintenance costs keep the company extremely competitive and ideally equipped to get the job done.