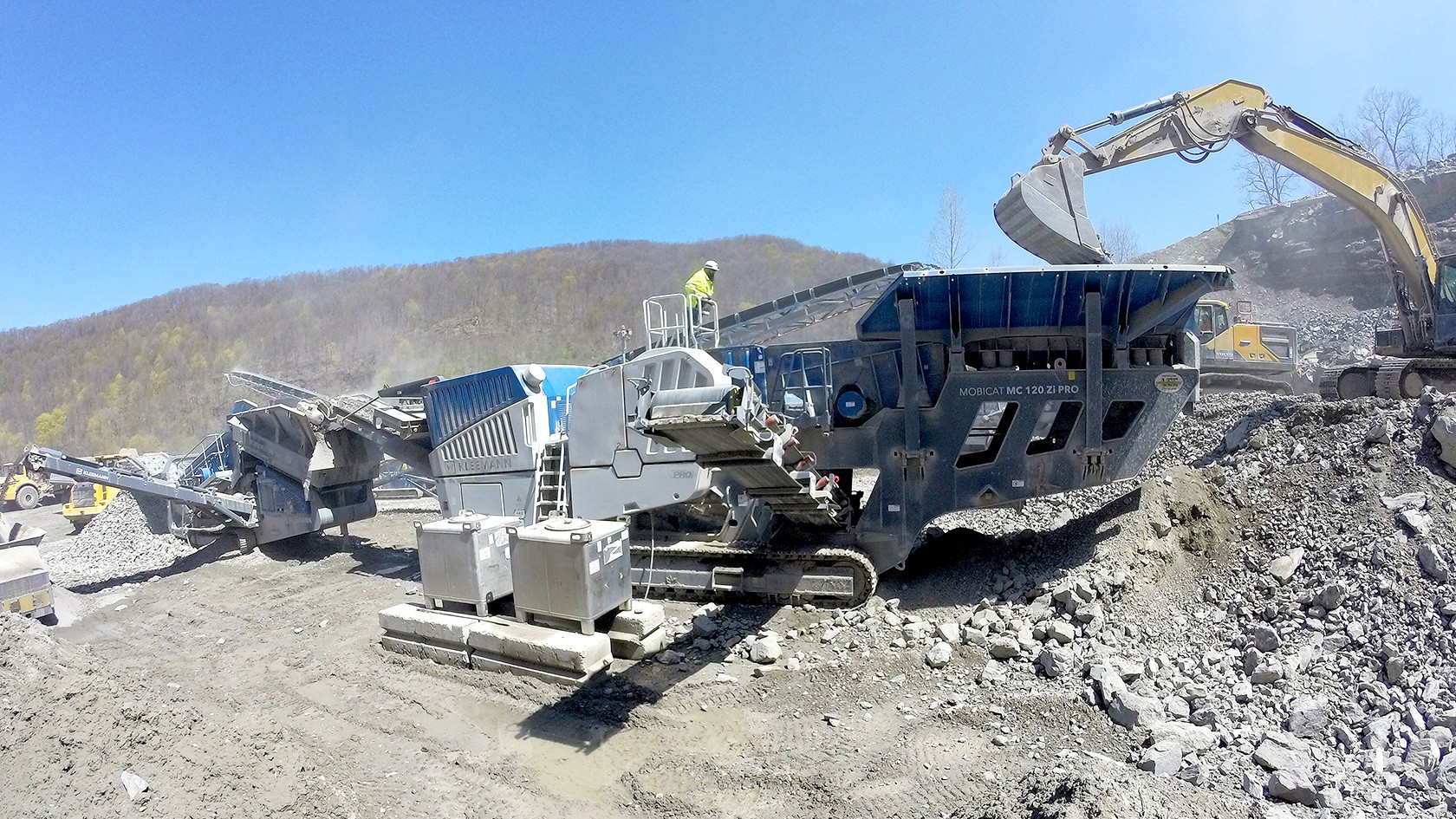
Ace Aggregates is a newly founded company that produces crushed rock in a reopened quarry in the West Virginian mountains. In around one year, the team has increased its production from 181,000 tons to approx. 545,000 tons per year – and delivered it.
The high demand is due to a first-class, hard limestone extracted by Ace Aggregates – and a booming economy in the state of Virginia. The production increase was made possible by efficient and mobile crushing and screening plants from Kleemann. The final products meet the most stringent requirements of the Department for Transport of West Virginia. Sufficient reasons for the young company to add to its Kleemann plant stock twice already.
"We acquired a disused quarry and, after a few months, started with the production and sale of crushed rock", reports Alex Wolfe, proprietor of Ace Aggregates LLC. "In the first nine months, we sold 315,000 tons of final product and blasted approx. 450,000 tons of stone. At present, we have increased our production output from 315,000 tons in nine months to over 181,000 tons per quarter." In the past, the same quarry had different owners and operators. "I don't know how high their production was, but I know that we have extracted and crushed more stone in a very short time of just over one year than they did in around 20 years", says Alex Wolfe.
"In our first full year of production, we intended to sell approximately 200,000 tons" added Wolfe. "But then demand picked up to such an extent that the operators quickly made 450,000 tons their target. "But even that was insufficient. After one and a half years in the market, we currently anticipate an output of around 545,000 tons a year. This was also accompanied by a reorganisation of the crushing processes and technology", says Justin Colebank, Operations Manager at Ace Aggregates.
Abrupt increase in production: growth of Ace Aggregates LLC in figures
At the start, the company deployed used plants from another manufacturer. However, it was not possible to reach the planned production output and it was difficult to find a service technician in the mountains of West Virginia. Furthermore, the technology did not work very efficiently and fuel consumption was very high. "It was like going to a shoot-out armed with a knife", Alex Wolfe remembers with a laugh. "We had no idea how much stone we would really sell. This is why we started with smaller, used plants. It didn't take long before we noticed that we needed a higher performance and exchanged the equipment." After a visit by Wirtgen Group at the Conexpo-Con/Agg trade fair and a discussion with Johnny Dillon, Sales Manager of the dealer Leslie Equipment Co., Wolfe short-listed crushing and screening plants from Kleemann.
"In a single year we crushed more stone than our predecessor in 20 years."
Alex Wolfe, proprietor of Ace Aggregates LLC
(in the photo with Johnny Dillon from Leslie Equipment Co., Justin Colebank, Operations Manager of the quarry of Ace Aggregates LLC, Alex Wolfe, proprietor of Ace Aggregates LLC and Thomas Jordan, Technical Sales Manager Kleemann with the Wirtgen Group in North America, from left to right)
"I always had a liking for products from Wirtgen Group, for example, I already had a look at the cold milling machines and recyclers from Wirtgen, including the WR 250i. I was impressed with the way Wirtgen Group designed their products. And the decision in favour of crushing technology from Kleemann also hit the mark. And the subject of service: I can call any time and a service technician is already on his way irrespective of the problem."
This was also very important to Alex Wolfe because it was his first time as the owner of a quarry. He therefore appreciated, in particular, the advice from Thomas Jordan, the Technical Sales Manager Kleemann at Wirtgen Group in North America, as well as Johnny Dillon. "They guided me in the right direction", says Wolfe. "I already had crushing plants on my building sites, but the processing of rock and stone was quite new to us. I didn't even know what screen sizes I needed. But they showed us everything." Since then, new Kleemann crushing and screening plants accelerate the productivity of Ace Aggregates.
After the initial experiences with the used, acquired plants, Ace Aggregates changed over – to a plant train from Kleemann. A MOBICAT jaw crusher MC 110 Zi EVO was used in the first crushing stage, and a MOBISCREEN screening plant MS 15 Z and a cone crusher MOBICONE MCO 9i EVO in the second crushing stage. At the end of the crushing process, a triple-deck classifying screen MOBISCREEN MS 953i EVO provided precise classifying of crushed aggregate.
But even this increased output was not enough. Within a few months, Ace Aggregates reacted to the high demand and, in collaboration with its partners from Wirtgen Group and Leslie Equipment Co., Jordan and Dillon, exchanged the crushing plants for two even more powerful ones. Or, more precisely, for a MOBICAT MC 120 Zi PRO in the first and a MOBIREX MR 130 Zi EVO2 in the second crushing stage.
In the meantime, the complete logistics in the quarry have been organised so that the stone can be transported by large articulated dump trucks over short distances. Some time ago, Ace Aggregates blasted a high rock face with an approximate height of 60 m. The blasted stone then accumulated on a cliff platform where it was further broken up by an excavator with a hydraulic hammer and then transported by another excavator into the 40-t skip of the truck so that it could be loaded into the jaw crusher.
Ace Aggregates LLC produces many different final products from the limestone in grain sizes of 40 mm to 300 mm as well as crushed sand. Each of these final products meets the stringent criteria of the Department for Transport of West Virginia, and many also meet the requirements of the American Association of State Highway and Transportation Officials AASHTO.
As was already the case with the first plant train from Kleemann, the two crushers also load a MOBISCREEN for coarse elements MS 15 Z or a classifying screening plant MOBISCREEN MS 953i EVO. Due to the integration of four Kleemann stackers with lengths of up to 24 m, however, the process sequence in the quarry has changed considerably. With the present arrangement, the articulated truck loaded on the cliff platform moves down a 45-degree gradient to a lower platform – and unloads the feed material near the MOBICAT MC 120 Zi, i.e. directly to the first crushing stage.
Now a bucket excavator loads the blasted stone into the generously dimensioned feeding unit of the jaw crusher. Here, an independently vibrating double-deck prescreen guarantees effective screening of fines which therefore no longer have to run through the plant. At the same time, this saves fuel, minimises wear and ensures a higher throughput.
After crushing, the jaw crusher transfers the stone to the MOBISCREEN MS 15 Z. It sorts the material into three sizes:
Kleemann stackers guarantee a high performance and optimised logistics in the quarry because they allow the creation of larger stockpiles of crushed stone.
The aggregate with a size of 40 mm to 75 mm is an intermediate product that is loaded from a wheel loader into the second crushing stage, namely into the impact crusher MR 130 Zi EVO2. The advantage compared to direct loading is that each of the two plants can operate to its full capacity.
The MR 130 Zi EVO2 is equipped with a secondary screening unit. Thanks to the use of a screen surface with a mesh size of 40 mm, smaller material reaches the downstream screening plant and large material is discharged.
The screening plant MS 953i EVO uses its three screen decks to sort the following final products:
The precisely classified final products – in this case crushed sand – are in high demand.
The operating company is more than satisfied with the low fuel consumption of the plant setup. "Compared to the used plants when we started working here, we achieve double the output with the Kleemann technology – and with the same or, in part, even lower fuel consumption", says Alex Wolfe, proprietor of Ace Aggregates.
"Now we only use half as much fuel as with our old second-hand jaw and cone crushers from a different manufacturer."
Alex Wolfe, proprietor of Ace Aggregates LLC
The Kleemann crushing and screening plants at Ace Aggregates are equipped with WITOS FleetView, the telematics solution from Wirtgen Group. The system records operating, position and maintenance data and makes a remote query of the statuses possible. This allows service technicians from Wirtgen Group in North America, or from Leslie Equipment, to react as fast as lightning.
Furthermore, users at Ace Aggregates benefit from SPECTIVE, the intuitive Kleemann operating concept that is deployed across the plants and which significantly simplifies control. "It is a very simple system", explains Thomas Jordan. "Once you know how to operate the jaw crusher, you also quickly understand how the impact crusher is set. SPECTIVE has an intuitive structure and makes operation very easy. Troubleshooting in the event of a malfunction is also very convenient."
"SPECTIVE is very easy to operate at the touch panel with its uncomplicated symbols. This also makes setting really easy", says Justin Colebank, Operations Manager at Ace Aggregates. "I like how fast it is to grasp the system. It is all self-explanatory. To start the plant, you just press a few buttons, operation itself and troubleshooting are carried out intuitively via the touch panel."
Standardised and intuitive operating concept SPECTIVE: Justin Colebank, Operations Manager at Ace Aggregates, making the plant settings.
The advantages of the crawler chassis of the Kleemann crushing and screening plants are demonstrated in the quarry in West Virginia about twice a week. Whenever blasting is pending, the plants are simply moved by remote control out of the danger area and traffic on the Mountaineer Highway is stopped. After the detonation, the machines return rapidly and undamaged to the quarry – and continue their work.
The high mobility of the Kleemann machines is only one of many reasons that explain how Ace Aggregates, without any experience in the sector, moved from an output of zero to 545,000 tons of crushed stone per year.
"The founding of Alex Wolfe's company was remarkable. Within three months he doubled or even tripled his production", says Thomas Jordan from Wirtgen Group in North America. "An amazing success!"