Reduced-temperature asphalts
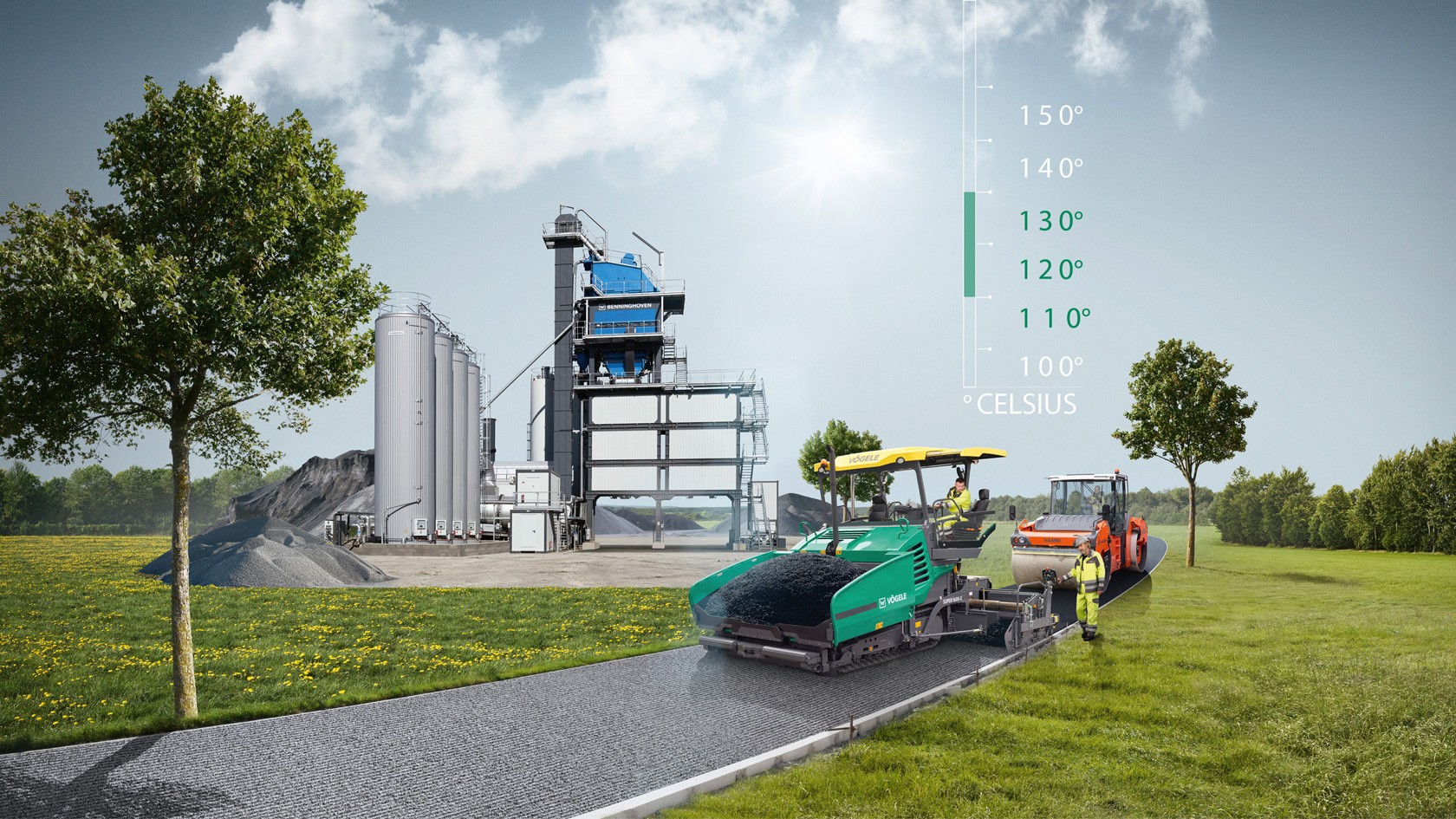
Energy-saving potential is one of the key drivers, and reduced-temperature asphalt is a road construction material that is currently becoming increasingly popular as a result. Technologies and solutions from the Wirtgen Group are the perfect response to this trend – and help ensure that the production and processing of lower-temperature mixes can be carried out virtually in the conventional manner.
Reduced-temperature asphalts – also known as low-temperature asphalt, warm asphalt, or warm mix – are mixes that have a production temperature of 110 °C to 130 °C. In contrast, conventional hot-mixed asphalts are produced at 140 °C to 180 °C – typically with 160 °C hot bitumen as the binding agent. There are numerous reasons for the growing trend toward the use of this building material in many countries and regions.
Reduced-temperature asphalt offers financial benefits, as these mixes require much less energy to produce. Lower energy consumption always means a reduction in emissions, especially CO₂ emissions. Increased environmental friendliness is an important issue, which is why reduced-temperature asphalt ranks high on the agenda of authorities worldwide. According to the German Asphalt Association, a temperature reduction of 30 °C alone saves 0.9 liters of heating oil (or a fuel equivalent) per ton of finished asphalt. At a daily production rate of 2,000 tons of mix, this corresponds to a savings of 1,800 liters of oil – or up to three-quarters of the energy required to heat a single-family home for an entire year. In addition, this corresponds to a reduction in CO₂ emissions of 6,000 kg per day. The figures that can be achieved in the real world are even higher – primarily because the reduction in temperature often reaches 50 °C or more.
When it comes to low-temperature asphalt, foamed bitumen is the binding agent of choice. Benninghoven knows its way around this material and can also integrate the technology into existing plants.
Matthias Lenarz, Team Lead Bitumen Systems, Benninghoven
Systems from the Wirtgen Group’s product brands already demonstrate their outstanding value during the production of reduced-temperature asphalts – above all, those from Benninghoven. This is because the production process is where the greatest potential to save energy and reduce emissions lies, i.e. in one of Benninghoven’s asphalt mixing plants. In this context, the specialist for the production and recycling of asphalt mixes of all kinds can draw on decades of experience – especially when it comes to the use of eco-friendly technologies. Reducing bitumen viscosity is a basic requirement for a reduction in temperature during asphalt production. This is because the binding agent bitumen actually requires a temperature of at least 140 °C to coat the mineral. Below this level, it remains too thick. As a result, Benninghoven has developed and successfully implemented various solutions to temporarily reduce its viscosity. This includes high-precision metering systems for the addition of liquid or solid additives as well as the Benninghoven foamed bitumen module.
Foamed bitumen is particularly attractive as a binding agent for the production of reduced-temperature asphalt because it only requires water as an additive, which is available at every asphalt mixing plant anyway. Mixing hot bitumen with water increases its volume many times over – this is also known as bitumen foaming. Due to the surface energy released, the binding agent covers the rock extremely well during the mixing process – even at low temperatures – and results in smooth paving properties.The technology behind the foamed bitumen module offers a key benefit for asphalt mixing plant operators. In this context, the mix weighing section is only extended by this plant option. It consists of a bitumen pump, an expansion chamber, pipework, and injection bars as well as a water metering system. Thanks to Benninghoven’s “plug & work” concept, the foamed bitumen module can also be retrofitted to existing plants at any time – simply remove the blind cover from the mixing chamber and bitumen scale and install the foamed bitumen module – that’s all there is to it. In combination with Benninghoven’s gentle and high-quality material processing, this results in reduced-temperature asphalts that can easily compete with conventional mixes.
The temperature reductions sought after in asphalt production are brought about by a temporary reduction in bitumen viscosity, which can be achieved by the addition of water or additives. On the one hand, low bitumen viscosity can be achieved withFoam bitumenor theUse of additives.
Find out moreMany contractors who have almost exclusively worked with conventional hot mixes up until now often ask themselves how reduced-temperature asphalt behaves during paving by road pavers. Vögele has been exploring this subject for a long time, researching and testing the paving of various such mixes – and providing real-world solutions.
With Vögele, the benefits gained during the paving process start even before turning on the paver. The mobile feeders in the PowerFeeder series – the MT 3000-3i Standard and the MT 3000-3i Offset – are essential when processing reduced-temperature asphalts. This is because they can unload a complete truck with 25 tons of mix in just 60 seconds. In conjunction with an additional container on the paver, it’s possible to hold up to 45 tons of material – ensuring that paving can continue without interruption. This lays the foundation for the largest possible time window for compaction, which is particularly critical when using low-temperature asphalt. An effective conveyor heating system also contributes to this, keeping the asphalt at the right temperature during transport to the paver. Vögele technology also plays a decisive role in producing unparalleled paving results.
The SUPER pavers feature a patented innovation that is particularly noteworthy in this context: the heated auger unit. “The component is located exactly at the point where the material falls onto the distribution auger and is distributed laterally. Heating it effectively prevents the material from sticking,” says Bastian Fleischer, product manager at Vögele, explaining the benefits of the exclusive and low-maintenance solution.
In addition, the components of every Vögele screed that come into contact with the material are also heated electrically. The use of Vögele’s high-compaction technology has proven to be particularly beneficial during paving. In this context, pressure bars powered by pulsed-flow hydraulics achieve a high degree of precompaction, which also extends the window of time for the rollers. In addition, Vögele has also developed and is already using specific technologies that greatly improve the processing of reduced-temperature asphalts – namely WITOS Paving Plus and RoadScan.
Vögele technology is perfect for processing reduced-temperature asphalts. The heater effectively prevents the material from sticking – and WITOS Paving Plus optimizes the processes.
Bastian Fleischer, Product Manager, Vögele
When processing reduced-temperature mixes, job site logistics play a particularly important role. This is because the greatest challenge on the job site is the window of time available for compaction – low-temperature asphalts, in particular, become increasingly resistant to compaction as their viscosity increases, so it is essential to complete the process at the highest possible material temperature. Because these asphalts are produced at a lower temperature, however, the gears during transport and on the job site need to mesh with each other perfectly in order to give the rollers as much time for compaction as possible.
WITOS Paving Plus offers valuable tools to successfully manage these complex processes and thus achieve high-quality results. WITOS Paving Plus is an integrated process optimization and documentation system solution from Vögele consisting of five complementary modules for the various individuals involved in the process – from the mixing plant operator and truck driver to the site manager.
The Materials and Transport modules are of particular importance on low-temperature asphalt job sites. WITOS Paving Materials integrates the mixing plant into the system, allowing mix to be ordered dynamically – the system sends a notification when a mix truck is due to leave for the job site. The delivery documents are also sent digitally to the site manager in advance. If a mix truck is on its way to the job site, the WITOS Paving Transport module reports its expected arrival time. Site managers receive this and other information in the WITOS Paving JobSite module. As a result, they always know how many tons of mix are currently on the road and can react quickly to the current logistics situation. This makes it easy to keep the paving process flowing – and with it, compaction.
Another Vögele solution, RoadScan, is now widely used to monitor and maintain a constant temperature range of the mix. In the process, an infrared camera measures the temperature of the entire area behind the road paver’s screed across a width of 10 m with extreme precision. The benefits are especially clear when using reduced-temperature asphalt – the system makes paving quality measurable and verifiable by measuring and documenting the temperature immediately after paving, which can be important, for example, in the event of an inspection by the client.
High-tech from Vögele supports job site logistics and documents the paving tempera-ture – with WITOS Paving Plus and RoadScan, paving teams can manage the supply of mix and contractors have documentation showing that paving was carried out within the correct window of time.
Further InformationsThe compaction of reduced-temperature asphalts also needs to meet exacting requirements. After all, the final result has to be achieved in a shorter window of time compared to hot-mixed asphalt. In order to introduce the required compaction energy into the material as quickly as possible, the tandem rollers used in this case generally operate dynamically, i.e. with active vibration or oscillation. Hamm also has another technology in its portfolio that is ideal for low-temperature asphalt job sites: the HCQ Navigator. The system increases both efficiency and quality. This is possible because the roller operators are shown a live compaction map on a panel PC in their cabin. It shows which areas have already been sufficiently compacted and which have not. In addition, environmental data such as the asphalt temperature and stiffness are also logged and displayed. All in all, this solution reduces the number of passes required.
In addition to the HCQ Navigator, Hamm’s WITOS HCQ offers the ability to remotely monitor the entire compaction process live. In this context, WITOS HCQ users have real-time access to the captured process data via the Wirtgen Group’s WITOS portal. In addition, this data can later be used for analysis and documentation.
Collectively, the plant and system technology from the Wirtgen Group makes it easy to begin using the promising construction material of reduced-temperature asphalt and ensures that the processes are extremely reliable.
"The HCQ Navigator shows which areas have already been sufficiently compacted and which have not. This means that fewer passes are necessary – a real advantage when you only have a small window of time."
Dr. Axel Mühlhausen, Product Manager Digital Solutions, HAMM
Further Informations