A whole new dimension of sustainability.
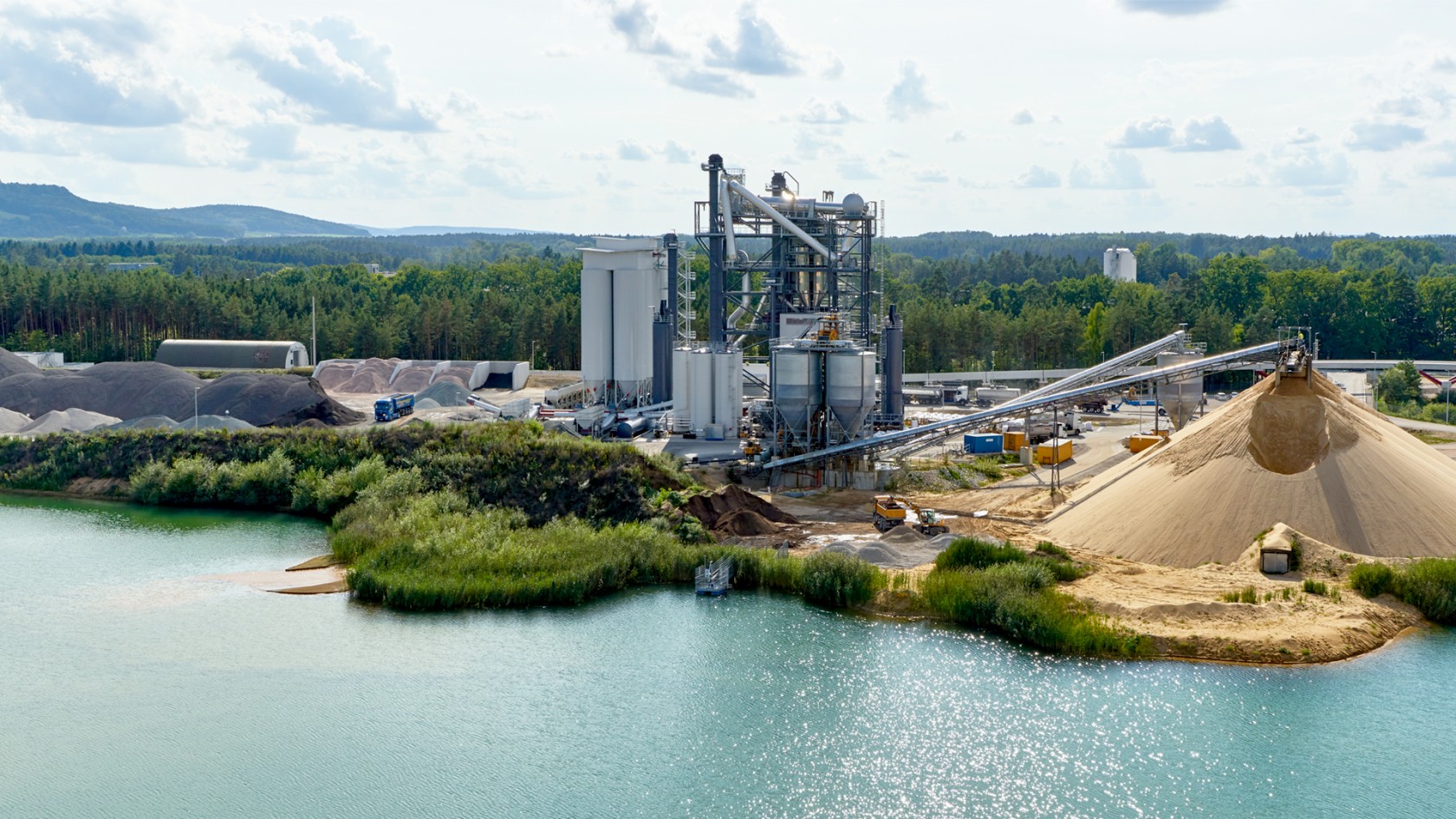
Investment in cutting-edge technology from BENNINGHOVEN: The new BA RPP 4000 asphalt mixing plant operated by the Max Bögl Group at its Sengenthal site provides the backbone for many road construction sites in the Nuremberg region. The most important innovation is a hot-gas generator with a counterflow system that supports RAP material rates of 90 + X % –with minimal emissions. The plant had already received an enthusiastic response from industry experts at bauma 2016.
Ready for asphalt production of the future: The new BA RPP 4000 operated by the Max Bögl Group is something special. The plant is installed at the Sengenthal site and supplies around 2,000 t of asphaltic mixtures to construction sites across the region every single day. Depending on the formula, the supplied mixture can contain around 1,800 t of RAP. That is because the recycling innovation from BENNINGHOVEN, which consists of a counterflow parallel drum system with a hot-gas generator, can achieve RAP material rates of 90 + X %. This unique technology also massively reduces emissions at the same time, making investment in this green and efficient technology particularly sustainable and forward-looking. In industrialized nations such as Germany, it has long been the case that many more miles of road are renovated than built from new – which means that millions of metric tons of asphalt are also removed. This task is largely handled by cold milling machines, which at their maximum performance level can load up to 3,000 t of milled material onto trucks in a single shift. This waste asphalt has long posed a challenge for road construction companies.
The recycling technologies from BENNINGHOVEN transform RAP – in the form of aggregate in a variety of grain sizes and the binder bitumen – into “black gold”. In many countries, almost every truck delivering asphaltic mixtures to a construction site carries a proportion of recycled asphalt. This is also demonstrated by the fact that – in Germany alone – out of a total of 40 million metric tons of asphalt laid each year, 12 million metric tons of recycled asphalt are now used by road pavers. RAP is also being increasingly identified as a resource around the world. In response to this trend, BENNINGHOVEN has developed and launched the counterflow parallel drum system with a hot-gas generator on the market. “The main advantage of this technology is that it combines sustainability and efficiency in a profitable way,” says Markus Bühl, Consulting and Sales from the sales and service company of the WIRTGEN GROUP in Augsburg. This was one of the main arguments that prompted Max Bögl to invest in a completely new plant rather than modernizing the existing one.
A second recycling technology – the multivariable cold feed system, which allows up to 40 % RAP to be fed cold into the production process – has also been integrated into the BA RPP 4000 plant. It allows small apshaltic mixtures from a volume of 2 t to be produced, which gives the operators of the mixing plant great flexibility. Thanks to the high-performance plant, Max Bögl is able to supply a wide range of different road construction sites in the Nuremberg area with asphaltic mixtures from Sengenthal with immediate effect – using its own fleet of temperature-controlled trucks.
Hot feed system: counterflow parallel drum system with a hot-gas generator for RAP material rates of 90 + X %
This cutting-edge technology achieves the highest RAP material rates in asphalt recycling worldwide. The recycling material is heated to the optimum asphalt processing temperature of 160°C in a parallel drum – in counterflow, as is also the case with aggregate obtained from quarries. Unlike in conventional asphalt production, the burner heats the RAP indirectly – using hot gases – to ensure that the bitumen contained in the asphalt does not burn while keeping emission levels within a normal range at the same time.