Benninghoven | Future fuels
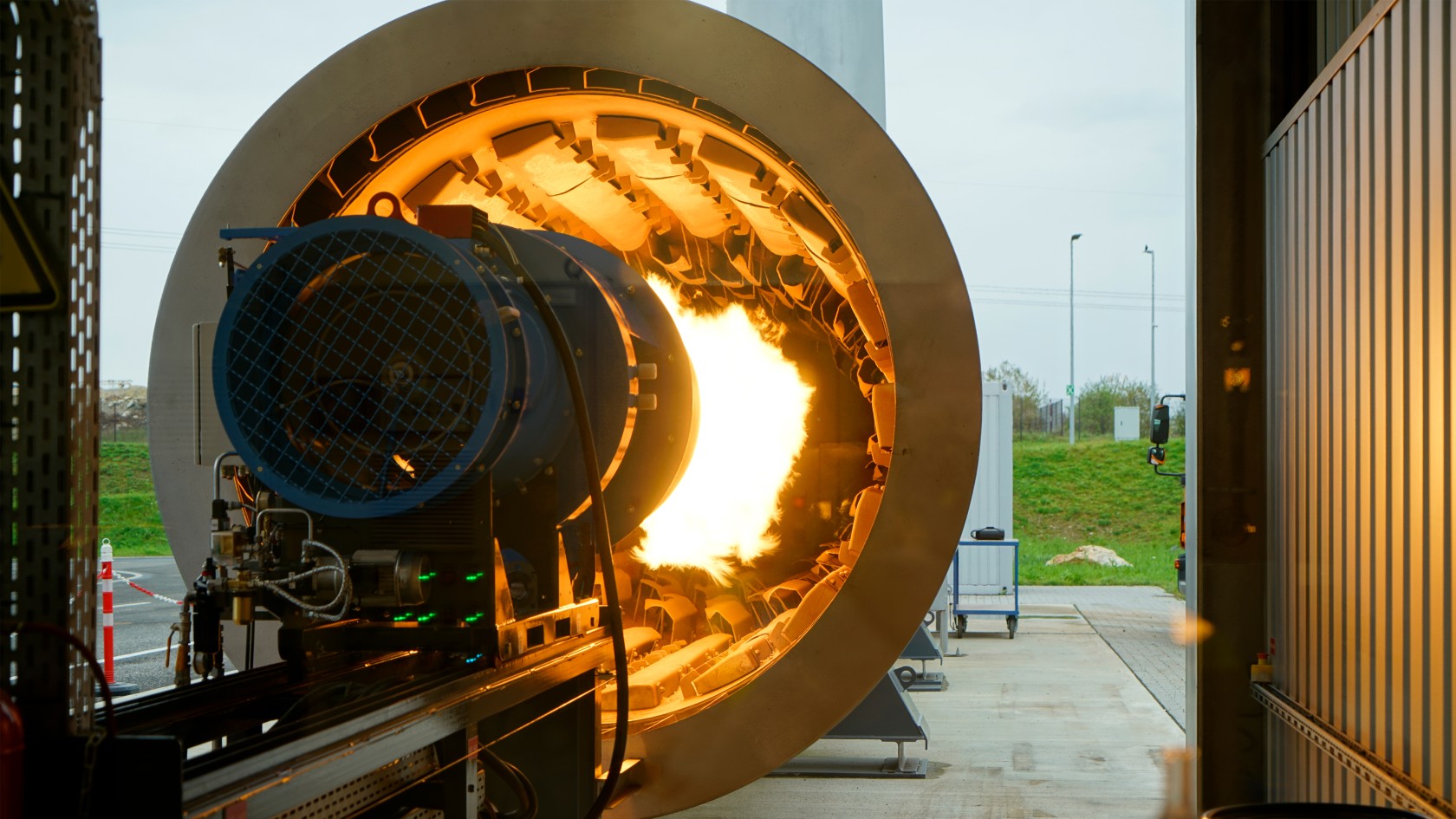
Benninghoven burners enable the safe use of renewable – and therefore sustainable – energy sources
Many markets are now preparing to exit from coal, while systems running on oil are also increasingly subject to tighter regulations and restrictions. With technologies from Benninghoven, operators can modernize their plants and safeguard the continued operation of their business. One example of these innovations is the EVO JET multi-fuel burner, which can use renewable fuels such as biomass-to-liquid (BtL) and wood dust. Both have a net-zero carbon footprint.
Making the switch from fossil to carbon-neutral
All over the world, climate action and tougher regulations from state and local governments are also challenging the asphalt industry to reduce their output of greenhouse gases like CO₂. For owners of mixing plants, reducing emissions also works to ensure the continued operation of their business. A more sustainable and cleaner approach to mixing asphalt can already be achieved by converting from oil or coal dust to gas: Burning natural gas or liquid gas will emit only half as much CO₂.
The figures for renewable fuels such as wood dust and liquefied biomass (biomass-to-liquid) are even better since these fuels are carbon-neutral. These future fuels are also more attractive in terms of availability: apart from their finite nature, the sourcing of fossil fuels has also become increasingly difficult. All of which makes it even more important for operators to identify the right technologies for alternative fuels and get their plants ready for the future.
Wood dust burners have a net-zero carbon footprint
Wood is a renewable resource whose production can be managed in a sustainable way and is therefore carbon-neutral when used as a fuel. The EVO JET wood dust burner from Benninghoven introduces wood dust as a fuel for firing asphalt mixing plants and again expands the company’s portfolio of burner technologies developed in-house. For operators, the wood dust burner offers a sustainable option for modernizing their existing mixing plants.
Benninghoven’s development engineers have worked out the ideal particle size for the wood dust, which is typically harvested from wood residues and waste. Identifying the optimum grading curve for the fuel is important for the burner’s flame geometry – and therefore for the effectiveness of heating either virgin mineral or recycled asphalt (RAP). Many of Benninghoven’s customers are already enjoying the benefits of their new EVO JET wood dust burner.
Making the switch to renewable fuels: Benninghoven’s EVO JET burners can also be operated on biomass-to-liquid or wood dust.
BtL burner introduces biomass as a sustainable alternative fuel
Another significant development in the energy market is the use of liquefied biomass, known as biomass-to-liquid (BtL). BtL can be made from plant waste like straw, wood, or energy crops like maize and oilseed rape. Benninghoven now also offers an innovative solution for the use of biomass as a fuel:
the EVO JET BtL burner. Like wood dust, biomass-to-liquid is also neutral in terms of carbon accounting. As with any EVO JET model, a Benninghoven BtL burner can also be operated with other fuels such as oil, coal dust, and gas. The new Benninghoven burners therefore offer plant operators a future-proof investment option: the chance to continue fossil fuel use in the short term but to be ready to switch to renewable fuels when necessary.
Benninghoven develops net-zero technologies
Benninghoven has pioneered the development of solutions that will be capable of meeting the medium- and long-term challenges now facing the asphalt industry. “One question that arose in this context was the role of hydrogen as a future fuel, since it produces no carbon emissions. However, we have to look at both availability and direct energy savings when it comes to burner fuels. Over the short term, using our gas, wood dust, and BtL burner solutions will achieve major reductions to emissions of carbon dioxide and other greenhouse gases,” explains Steven Mac Nelly, Head of Design & Development at Benninghoven.
Benninghoven also follows a clearly defined process for new developments and product improvements, which naturally applies to burner technology, as one of the company’s core competencies. Here, the development team makes use of advanced infrastructure that includes the latest simulation software as well as burner test benches.
As an asphalt mixing plant specialist, the development of sustainable fuels is a key part of Benninghoven’s efforts to provide solutions for sustainable, clean, and efficient asphalt production. These solutions also include the innovative Benninghoven hot-gas generator and REVOC system, which help to achieve high rates of recycling with low emissions.
“We’re thinking ahead and developing tomorrow’s solutions today. Apart from allowing the use of future fuels like wood dust and BtL, we’re also focusing on direct energy savings,” comments Steven Mac Nelly, Head of Design & Development at Benninghoven.
Public Relations
Reinhard-Wirtgen-Straße 2
53578 Windhagen
Germany