Road rehabilitation with the SUPER 1800-3i SprayJet
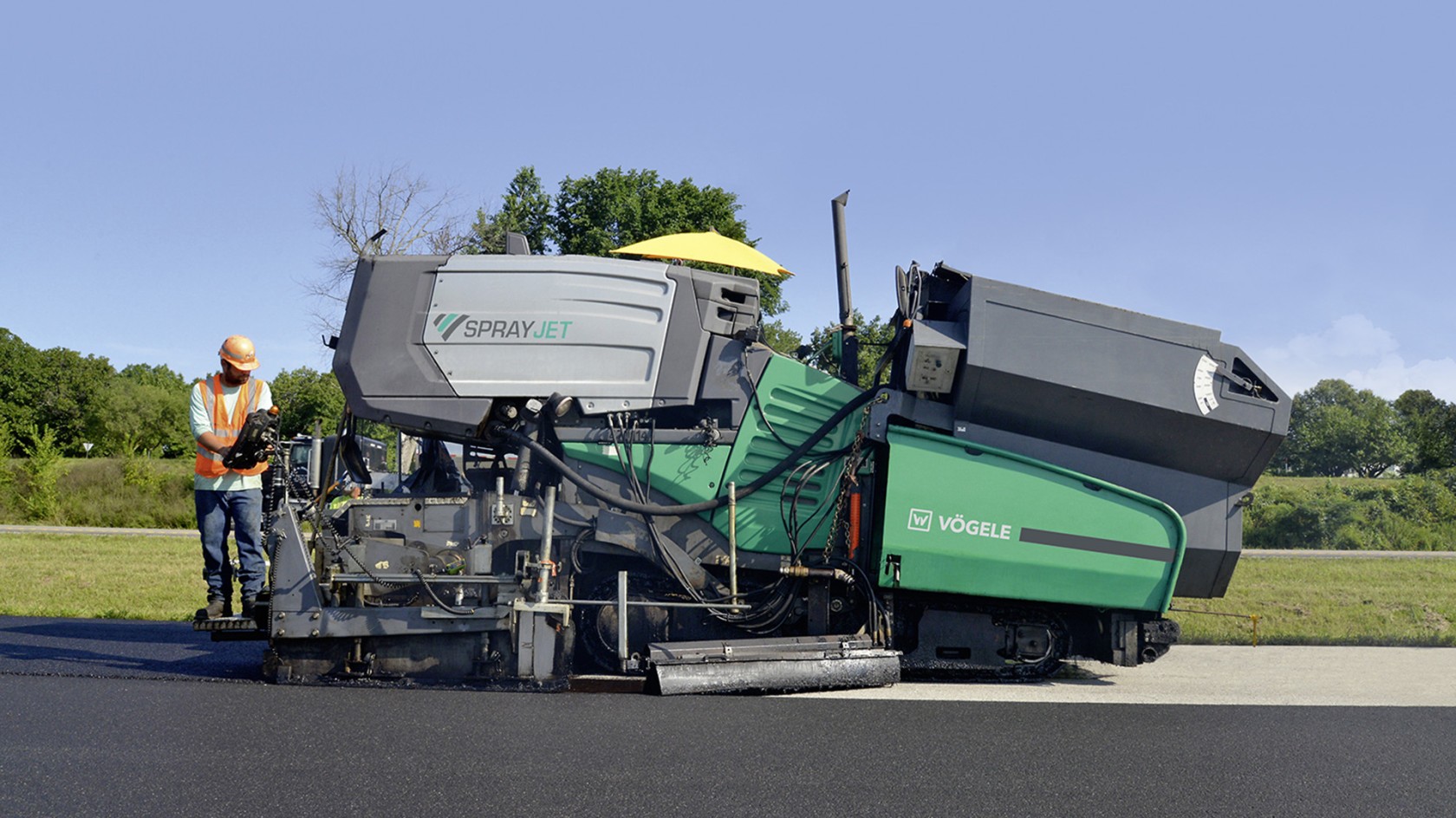
Contractors and government road agencies in North America have been using the VÖGELE SUPER 1800-3i SprayJet paver – and its predecessor, the SUPER 1800 SF – to place ultrathin bonded overlays like NovaChip for years. But increasingly, VÖGELE SprayJet technology is being used to place standard hot mix asphalt overlays as well as ultrathin bonded overlays. The ultrathin bonded overlay is a durable pavement preservation surface treatment generally no more than 3/4-in. deep. Utilizing polymer-modified emulsion from the onboard tank, a computer-controlled spray system built into the SUPER 1800-3i SprayJet places a bond coat, also called a “tack coat”, over a width of maximum 19 ft. 8 in.
Dallas | Texas
On top of this tack coat, the paver immediately places a polymer-modified, open-graded surface mix – fed to it by truck or material transfer vehicle – that cures very rapidly as it’s compacted by a roller in mostly static mode. The resulting ultrathin lift optimizes the use of high quality aggregates, while maintaining overhead clearances and curb reveal. And the one-pass construction process moves quickly, allowing efficient construction and return of traffic, while the open-graded mix mitigates tire noise and back spray, thus preventing hydroplaning and improving visibility in wet weather.
In a classic application for the VÖGELE SUPER 1800-3i SprayJet paver, in heavy traffic on Dallas North Tollway, crews of Austin Bridge & Road used its new SUPER 1800-3i SprayJet paver with an integral tack coat spray system to place a 3/4-in. polymer-modified ultrathin bonded overlay.
Such a thin overlay was placed on the Dallas North Tollway in summer 2018. There, Austin Bridge & Road used its new SUPER 1800-3i SprayJet paver to place 50 lane miles of ultrathin bonded overlay nonstop over multiple 48-hour shifts. The spray paver resulted in a fast-moving, clean placement of tack coat and polymer-modified thin overlay. This open-graded mix was placed 3/4-in. deep, utilizing 3/8-in. size aggregate with minimal fines. “Placement of tack coat by the paver results in superior bonding of the overlay to the pavement, with tack coat staying in place and not being tracked off the road,” said Mike Kuhn, General Superintendent for Austin Bridge & Road (AB&R). “There’s also less end-of-job cleanup work.”
Austin Bridge & Road’s crews also approve of the new paver. “Our crews like it,” Kuhn said. “I asked them, why do you like it? They take their glasses off, look at their uniforms and say, ‘No spots’! We no longer have the issue of workers covered with specks of emulsion. It also means that passing automobiles don’t get tack coat on them.” And that makes a big difference to the operator. “The biggest part for us is how clean it is to operate, compared to other processes,” Kuhn said. “The end-of-day cleanup takes 30 minutes thanks to the integrated clean mode, compared to competitive machines where it takes over an hour. There also is no need to use plastic to clean out the spray bar. All of this cuts costs and time for us.”
On the Dallas North Tollway, Austin adhered to a tight schedule in which it started paving on a Friday night and continued for 48 hours straight until Sunday evening. To keep the job moving, it used an auxiliary distributor truck to supplement the onboard emulsion tank on the spray paver. “With the distributor truck hooked up, we were traveling at up to 60 ft. or more per minute,” Kuhn said. “When the distributor got low we would top off the onboard emulsion tank and we would slow to 30 ft. per minute to give the truck time to refill and get back. After the refill process, we were able to get back up to 60 ft. per minute.” During the ultrathin placement, Austin Bridge & Road worked with lane closures from Friday, 10 p.m. to Monday, 5 a.m. “Generally we try to be completed with the paving by 6 p.m. Sundays to allow time for cleanup and striping,” Kuhn said. To keep the work moving day-andnight, all weekend, Austin kept an average of 10 trucks lined up in front of the SUPER 1800-3i SprayJet. “On that job, we had a 45-minute turnaround to refill and return,” Kuhn said. “We did 41,000 sq. yd. in nine and a half hours the first night! I remember ten years ago, if you got 30,000 sq. yd., you were celebrating. And now we expect to do that every day with this paver.”
The VÖGELE SUPER 1800-3i SprayJet has five spray bars with a total of 24 high-quality spray nozzles. Spaced 250 mm apart with a 120° spray cone, these ensure the seamless application of emulsion. Depending on the type of emulsion and nozzle size, the rate of spread can be varied between 0.3 and 1.6 kg/m2. All the paver operator has to do is set the required quantity before spraying starts. This produces a uniform film of emulsion which covers the entire surface without overlaps. The nozzles of the VÖGELE SUPER 1800-3i SprayJet operate in pulsed mode rather than continuously. This, combined with the low spraying pressure of just 43.5 lbs psi, means that misting is almost completely prevented.
Mansfield | Missouri
As an alternative to spray paving, the VÖGELE SUPER 1800-3i SprayJet also can be easily adapted to conventional hot mix asphalt (HMA) paving following removal of the emulsion spray module. But now state departments of transportation are going beyond ultrathin bonded overlays as they consider the benefits of the placement of HMA mats using the built-in spray system of the spray pavers. “In the three states in which we do business, it’s a requirement for some jobs that a spray paver be used to apply the bond coat emulsion and the mix, whether for an ultrathin bonded overlay, or a conventional Superpave mix,” said Andy Ernst, Vice President for Construction Operations, Pace Construction, St. Louis. “A competitor could not have bid on this portion of the job with only a conventional paver and tack distributor truck, unless he chose to place a chip seal with asphalt overlay, a method we decided not to offer in our bid.” Spray paver-placed conventional overlays are specified at the discretion of the state, according to the job at hand. “I don’t see distributor tack and paving ever going away,” Ernst said. “Instead, spray paving for conventional HMA is just one more tool in the owner’s toolbox – another way to achieve superior pavements. It does a very good job and I see a need for both types of applications.”
On U.S. 60 in southwest Missouri, Pace uses its SUPER 1800-3i SprayJet with integral spray system not to place 3/4-in. ultrathin bonded overlay, but a conventional 2-in. Superpave mix. Ernst expects to see more spray paver-applied conventional HMA pavements in the future. “This year we are using this method to place two pavements in Indiana,” he said. “They’ve been doing ultrathin bonded overlays, but this year is the first time they’ve placed conventional HMA with a spray paver.” A tack coat adheres one layer of asphalt to another layer of pavement, whether bituminous or portland cement concrete. Research shows that layers of pavement perform better when thoroughly bonded to each other, just as fragile, thin veneers of wood form a robust sheet of plywood when they are glued to each other.
Andy Ernst, Vice President for Construction Operations, Pace Construction
While it typically uses its SUPER 1800-3i SprayJet to place ultrathin bonded overlays, Pace Construction of St. Louis, was using its paver to swiftly place a 2 in.-deep conventional Superpave HMA lift, compacted to 1 3/4 in., on the dual-lane U.S. 60 near Mansfield in southwest Missouri. Two breakdown rollers and a finish roller were being used, with a target density of 94%. For U.S. 60, Missouri, DOT provided an option for standard paving with the spray paver. That’s because owning agencies like elimination of the tack coat distributor truck for conventional paving, as is possible when HMA is placed with a spray paver. This option is clean, without haul trucks driving through the emulsion, tracking it all over temporary striping, the pavement and the lift that was placed the day before. Spray paving eliminates all that as the tack coat is placed by the paver immediately ahead of the lift of asphalt.
With its VÖGELE SUPER 1800-3i SprayJet, Pace would place up to 12,000 t of Superpave mix 2 in. deep on U.S. 60 in southwest Missouri.
“I’ve been working with the spray paver all summer, and this is the first full-depth conventional HMA job we’ve done,” said Bob Needels, Project Manager for Pace. “The others have all been 5/8 in. ultrathin bonded overlays. U.S. 60 is the first Superpave I’ve ever seen it lay, and we’re getting really good results out of it. It’s a very clean process, with no tracked tack. We’re getting a good reaction out of the truck drivers, who don’t like tack slung all over their trucks any more than we do on our equipment. Using the SUPER 1800-3i SprayJet benefits everybody.” Pace’s Needels said it’s actually better not having the distributor truck in the paving train at all. “It’s safer, because it rules out delivery trucks sliding on the slick tack off into the ditch,” he said. “And if a car happens to get into the closed lane, and they slam on their brakes, there is no tack to slide them out of control.”
One paver manufacturer offers an aftermarket spray system that must be attached to the machine, but this poses significant disadvantages, Ernst said. “The dedicated spray functions of the VÖGELE paver work great for us, because we can get those jobs with spray specs year after year and keep it operational all season,” he said. “That’s why we choose not to make use of the option of removing the SprayJet module for conventional paving.” Pace looked at a competing make of spray paver, and even at the paver for which an aftermarket spray system had been devised, but chose to go with VÖGELE. “That maker was introducing its aftermarket system and considering it was new technology, we just didn’t feel comfortable with that,” Ernst said. “They had a different manufacturer making the spray unit to fit the paver, and with it all being so new, we chose not to go down that road,” Ernst said. “And the only other purchase option was a model which could only be fed by a material transfer vehicle, while the SUPER 1800-3i SprayJet can be serviced directly by trucks if the insert is removed from the hopper,” he added. “That was a feature that was very appealing to us, because we will place the ultrathin bonded overlay in subdivisions without much room for an MTV.”