Reduced-temperature asphalt
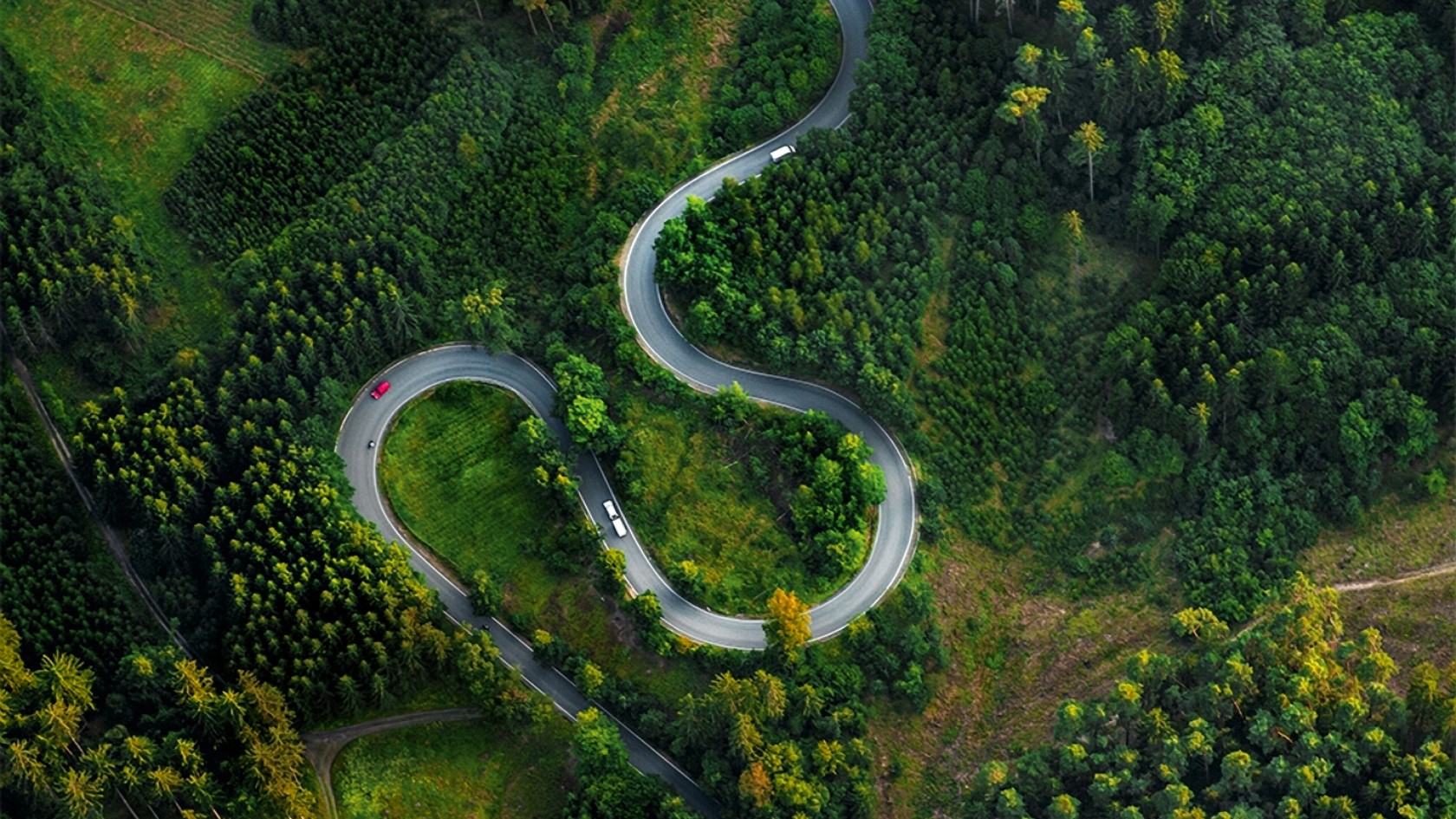
The term “reduced-temperature asphalt” is used for an asphalt that can be manufactured and processed at a lower temperature without negatively affecting its properties.
The main difference to conventional hot asphalt is the processing and installation temperature. In figures, that means a temperature reduction of 20–40 °C. Some of the accompanying effects in production and use include an improved total energy balance, for example, as well as a reduction in emissions during manufacturing and lower figures for workplace exposure levels when installing the asphalt.
* Deutscher Asphaltverband e.V., Asphalt Guideline, Reduced-Temperature Asphalts
Reduced-temperature asphalt
The temperature reductions sought after in asphalt production are brought about by a temporary reduction in bitumen viscosity, which can be achieved by the addition of water or additives.
Bitumen (the binder) cannot actually wet/envelope the mineral component until about 140 °C – its viscosity is simply too high at lower temperatures. The fluidity or viscosity also depends on the specific bitumen used and can vary widely between different types of bitumen. Since viscosity is temperature- and type-dependent, hard bitumen has a higher viscosity at the same temperature than soft bitumen. A standard temperature range is between 140 °C and 180 °C, and typically around 150–160 °C.
The reason for achieving a binder viscosity that’s low enough is to ensure good wetting and enveloping of aggregates in the mixer. The smoothness of the asphalt mixture also plays an important role when installing the road surface and ensuring the asphalt can be compacted.
On the one hand, low bitumen viscosity can be achieved withFoam bitumenor theUse of additives.
By mixing hot bitumen with water in the foam bitumen module, the bitumen is foamed up to multiple times its original volume. This temporarily reduces its viscosity. In addition, the wettability of the stone materials is also improved, due to the larger surface area.
All you need for the technical implementation is to expand the weighing/mixing section with the FOAM BITUMEN MODULE: this is flange-mounted onto the mixer cabinet and the bitumen weigh hopper.
Straightforward connection using PLUG & WORK guarantees rapid installation and commissioning.
BENNINGHOVEN’s technical solution for adding smaller quantities of solid additives is its Powder/granulate dosing system. Based on materials and quantities needed, additives are dosed into the mixer with an air-flow based system. Another option is the Multivariable feed system – a patented solution that features precise dosing (exact weighing system) and which enables the dosing of larger volumes of additives into the mixer. Material is fed in here using an elevator or inclined conveyor.
For up to two liquid additives, the Adhesive system can be used to add these to the process. The system is equipped with two feed pumps that dose the liquid additives into the bitumen weigh hopper and/or into the mixer. The system is characterized by its excellent chemical and thermal stability.
This is another area where BENNINGHOVEN is your trusted partner. From our FOAM BITUMEN MODULE to dosing systems for feeding a wide variety of additives to your process, we have the answer to your individual requirements. Thanks to Plug & Work, a retrofit can be completed quickly and easily for any kind of plant.
Working more efficiently with sustainable and economical technologies is the challenge of today and tomorrow. Benninghoven offers a variety of innovative solutions for increasing sustainability in asphalt production.
Find out moreAsphalt production, recycling systems, combustion technology, control systems, and bitumen technologies – thanks to BENNINGHOVEN’s technologies, each of our customers can find the right solution for their specific site that fully complies with requirements and conditions.
Go to technologies