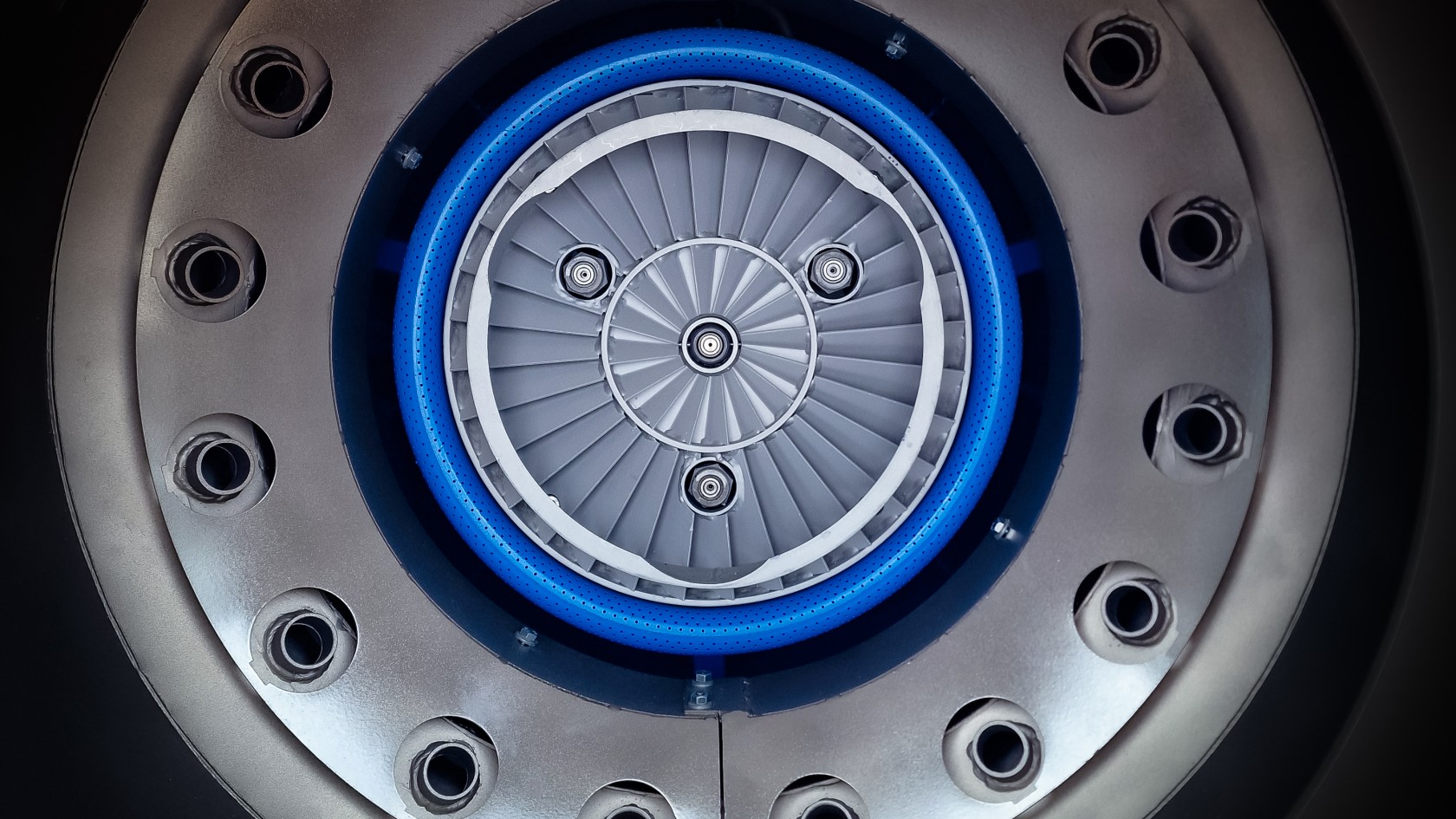
Benninghoven burners enable reliable use of renewable and therefore sustainable energy sources
Many markets are now preparing to exit from coal, while systems running on oil are also increasingly subject to tighter regulations and restrictions. With technologies from Benninghoven, operators can modernize their plants and safeguard the continued operation of their business. A contribution here is made by EVO JET multi-fuel burners, which can use renewable fuels such as biomass to liquid (BtL) and wood dust. Both have a net-zero carbon footprint.
100% green hydrogen system for road construction
With the first burner anywhere in the world that can be run up to 100% on green hydrogen, BENNINGHOVEN offers a forward-looking solution for greater sustainability in roadbuilding.
All from a single source – From the hydrogen source itself, the scope of delivery from Benninghoven covers the feed systems plus pressure regulation section, multi-fuel burner, hydrogen control section, burner control and plant components adapted to run on hydrogen.
The burner also ships with a new control system, while the carefully coordinated hardware and software solution keeps the asphalt production process cost-effective.
Burner technologies from Benninghoven can be used to equip both new plants as well as existing asphalt mixing plants. Retrofit solutions can also be deployed in plants from other manufacturers. This gives any plant operator the chance to start using the latest technologies whenever they want to – a key aspect for ensuring cost-effective, sustainable asphalt production and long-term job security.
Download
All over the world, climate action and tougher regulations from state and local governments are also challenging the asphalt industry to reduce their output of greenhouse gases like CO₂. For owners of asphalt mixing plants, reducing emissions also works to ensure the continued operation of their business. A more sustainable and cleaner approach to mixing asphalt can already be achieved by converting from oil or coal dust to gas: While switching to natural gas or liquid gas can halve carbon emissions,
the figures for renewable fuels like wood dust and liquefied biomass (biomass to liquid) are even better, since these fuels are carbon-neutral. These future fuels are also more attractive in terms of availability: apart from their finite nature, the sourcing of fossil fuels has also become increasingly difficult. All of which makes it even more important for operators to identify the right technologies for alternative fuels and get their plants ready for the future.
“We’re thinking ahead and developing tomorrow’s solutions today. Apart from allowing the use of future fuels like wood dust and BtL, we’re also focusing on direct energy savings.”
Steven Mac Nelly, Head of Design & Development at Benninghoven
Energy from biomass
The principle of producing BtL fuels is based on liquefying biomass.
In the case of wood as a starting material, thermo-chemical conversion processes in a reactor use high temperature and high pressure to turn the cellulose-rich wood into pyrolysis oil.
Other steps in the process include purification, synthesis, and the refining of this pyrolysis oil into BtL fuels.
Another significant development in the energy market is the use of liquefied biomass, known as biomass to liquid (BtL). BtL can be made from plant waste like straw, wood, or energy crops like maize and oilseed rape. Benninghoven now also offers an innovative solution for the use of biomass as a fuel
: the EVO JET BtL burner. Like wood dust, biomass to liquid is also neutral in terms of carbon accounting. As with any EVO JET model, a Benninghoven BtL burner can also be operated with other fuels such as oil, coal dust, and gas. The new Benninghoven burners therefore offer plant operators a future-proof investment option: the chance to continue fossil fuel use in the short term but to be ready to switch to renewable fuels when necessary.
For wood or wood waste as a starting product, the challenge lies in the processing of the natural material, which can vary greatly in its chemical composition. These variations then affect the final BtL product. Smaller fluctuations can be compensated for by adjusting the preheating temperature. Larger fluctuations or fuel changes, however, require adjustments on site.
For new fuels, customers therefore send their heating medium to Wittlich in a stainless steel container so the correct basic parameters for the burner can be determined at the BENNINGHOVEN factory. The fuel is tested extensively here and the optimum burner settings are identified.
Still burning in the future
Wood is a renewable resource whose production can be managed in a sustainable way and is therefore carbon-neutral when used as a fuel. With the EVO JET wood dust burner, Benninghoven has made it possible to use wood dust in asphalt mixing plants – adding another product to the portfolio of burner technologies developed in-house. For operators, the wood dust burner offers a sustainable option for modernizing their existing mixing plants.
The design engineers at Benninghoven have worked out the ideal particle size for the wood dust, which is typically harvested from wood residues and waste. Identifying the optimum grading curve for the fuel is important for the burner’s flame geometry – and therefore for the effectiveness of heating either virgin mineral or recycled asphalt (RAP). Several Benninghoven customers are already successfully using the EVO JET wood dust burner.
The features offered by the solid fuel burner give it the advantage of being able to use both coal dust and wood dust as fuels.
When a new burner is purchased, it can be adjusted to using coal dust or the “future fuel” of wood dust.
With bottlenecks in the coal dust supply already making their presence felt, however, carbon-neutral wood dust fuel is fast becoming the more attractive option.
A full set of peripherals includes the burner and the dosing unit. The dosing unit inlet is formed by the interface to the customer systems. The wood mill and wood silo are provided by the customer.
Brenner
The wood dust is fed into the burner with precision dosing by means of the feed fan and the dosing unit. In the burner head, a separate auxiliary flame then ignites the material. The control range for wood dust with an auxiliary flame is 1:6, with the calorific value of wood dust being approx. 18 MJ/kg depending on the type of wood.
A secondary fuel such as heating oil EL or liquid/natural gas is used for the auxiliary flame.
The wood dust dosing system with storage tank has a capacity of 2.5 m³ and is installed at the wood dust silo discharge. In the tank, two agitators prevent the wood dust from clumping together. A speed-controlled dosing screw releases the fuel in accordance with the required burner output and transports the wood dust into a blow-through rotary valve, which forms the interface to the conveying pipe. From here, the wood dust is blown into the head of the burner with a feeder fan and pipe.
Starting material on the asphalt mixing plant
> Wood pellets
> Wood chips
> Wood dust
Within Germany, the operating company must ensure that the overall plant (e.g. silo plus dosing system) is routinely inspected according to the BetrSichV industrial safety regulations. Outside of Germany, inspection obligations must be fulfilled according to applicable national laws and regulations.
> Explosion protection (ATEX) specifically for coal dust and wood dust
Liquid gas burner and natural gas burner
BENNINGHOVEN gas burners are capable of burning liquid gas while it is still in its liquid phase, without first having to transform the gas into a gaseous state. This means that no additional peripheral such as vaporizer is needed nor the corresponding input of energy.
Liquid gas burners and natural gas burners have the same mechanical structure, and differ only in terms of their peripheral equipment, i.e. how the fuel is introduced into the burners.
> In the burner head, the fuel is gasified while being mixed with the oxygen before then being ignited.
> The burner head is made of a highly heat-resistant material
> The special geometry of the head also determines the shape of the flame
Liquid gas, termed “associated gas”, is produced during the extraction of crude oil or natural gas. Previously, this associated gas was often simply released into the atmosphere or flared off. With gas flaring now increasingly prohibited around the world, this has had an additional positive impact on the increasing availability of liquid gas.
Oil burner for extra-light heating oil (heating oil EL)
Heating oil made from crude oil is classified as one of two types: extra-light heating oil (fuel oil EL) and heavy fuel oil (fuel oil S). Quality requirements for heating oil are set out in the DIN 51603 standard. Extra-light heating oil can be burned in kilns, central heating systems and industrial furnaces without pre-heating. However, heavy fuel oil must be pre-heated before transport and combustion. Systems operated using these fossil fuels are now increasingly subject to regulations and restrictions, however.
> BENNINGHOVEN EVO JET burner, installed on the dryer drum
> For optimum drying and heating of the virgin mineral or recycled material, with extra-light heating oil (EL) used as fuel.
> Compressed air is used to create a combustible fuel/air mixture within the nozzle.
> This allows optimum atomization of the oil particles across the largest possible surface area.
> The fuel/air mixture is then injected/atomized into the burner head.
> Compressed air 7 bar, oil pressure 12 bar.
> This has the advantage of a short, easily controlled flame and a high output control range of 1:8.
> Calorific value of extra-light heating oil 42,700 kJ/kg.
> Oil return nozzle as alternative
Coal dust burner (lignite or thermal coal) and coal dust dosing system
Relentlessly rising energy costs and the need for careful management of limited resources require innovative technologies plus continuous improvement. The EVO JET burner has been developed by BENNINGHOVEN’s research team to meet real-world needs.
BENNINGHOVEN’s established and well-known approach to usability also played a key role in the development of this burner. The burner features a modular, highly accessible design.
The burner is mounted on a chassis to ensure it can be easily moved into place for maintenance work. A frequency converter system ensures that both the burner fan and oil pump are perfectly coordinated with one another, and can work throughout all control ranges. As a result, only the specific level of consumption requested is used for drying, whatever the output setting. Redesigned from scratch, the new silencer keeps noise to a minimum while simultaneously improving the energy conversion efficiency of combustion. This is achieved by the new air inlet layout. The improved energy conversion efficiency results from trapping the heat radiated by the front wall of the drum and re-routing the preheated air to the burner. This, in turn, means less energy is required to preheat the air, which helps to lower the costs of fuel. Burners in the EVO-JET series feature mature designs for all fuel types and have been comprehensively field-tested. This energy-saving program is rounded off by BENNINGHOVEN installing only electric motors compliant with the new IE 2 (or IE 3) standard – soon to become mandatory.
> Coal dust is a solid particulate fuel that is manufactured from lignite or thermal coal. This dust is either a waste product collected while mining coal from the seam or is produced as a commercial product in milling plants.
> Coal dust is a fossil fuel and also viewed as a low-cost fuel.
> BENNINGHOVEN EVO JET burner HGG, installed on the dryer drum
> Coal dust is fed into the burner with precision dosing using the supply fan and coal dust dosing system.
> In the burner head, a separate auxiliary flame then ignites the material.
> This flame switches off once burner output is 20% of nominal burner output
> The solid material flame continues to burn independently from this point or is activated again automatically if output drops below this value again
> Fuel for the pilot flame can also function as an independent fuel
> Control range 1:5 coal dust (alone) and 1:8 coal dust (with auxiliary flame)
> Calorific value of coal dust 20,900 kJ/m³
> Burner control, output control, coupled control, and switchover between fuels are effected with a type-approved control system
The BENNINGHOVEN EVO JET burner, designed as an oil burner in standard burner models, can be expanded to utilize up to three fuels. This turns the burner into a combination burner, which means that other types of fuel such as oil, natural gas, liquid gas, heavy oil, BtL fuels (liquefied biomass), and coal dust are all available as fuels. The lignite dust is fed into the feed line with the aid of the coal dust dosing system (flange-mounted onto the outlet valve of the coal dust silo) and blown into the head of the burner by a conveyor blower.
This well-designed coal dust dosing system offers operators a number of key benefits:
> Functionality
> Fuel consumption
> Safety
Working more efficiently with sustainable and economical technologies is the challenge of today and tomorrow. Benninghoven offers a variety of innovative solutions for increasing sustainability in asphalt production.
Find out moreAsphalt production, recycling systems, combustion technology, control systems, and bitumen technologies – thanks to BENNINGHOVEN’s technologies, each of our customers can find the right solution for their specific site that fully complies with requirements and conditions.
Go to technologies