Concrete Paving Technology
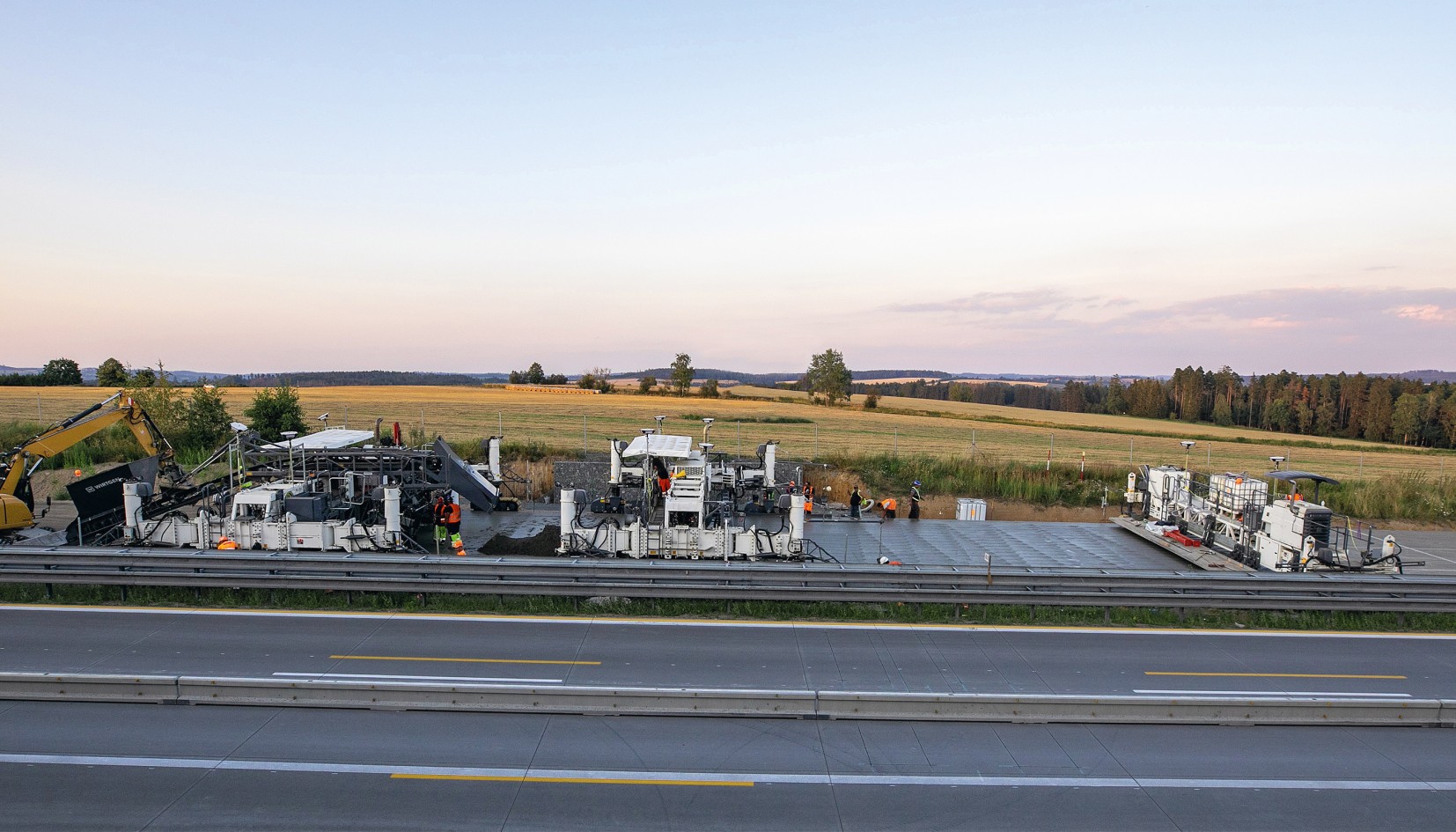
For extremely hard-wearing highways or runways and the production of monolithic concrete profiles, we offer sophisticated processes that make construction easier for you. Leverage our wide range of machines for maximum precision in concrete paving.
Discover the operating principle and technical components of concrete paving. Become familiar with the inset and offset methods and learn more about our standard and special applications.
In offset applications, a concrete mixer transfers the concrete to the receiving hopper. The material is transported into the slipform via a swivel-mounted conveyor belt or a swivel-mounted auger conveyor. Depending on the machine model, the conveyor belt is available in various lengths and in a folding version. Different versions of the auger conveyor are also available. Whether conveyor belt or auger – all of the settings such as conveyor speed, inclination angle, or position can be adjusted at the touch of a button. An additional transverse auger conveyor offers many benefits. For example, the concrete mixer can travel in front of the slipform paver and not need to be off to the side, thereby eliminating the need to close another lane. Despite the fact that a larger quantity of concrete is required as a buffer, the transverse auger conveyor is still an ideal solution – like in tight bends where the concrete mixer is unable to permanently supply the machine with concrete, for example.
In inset application, the concrete is either deposited right in front of the slipform paver or is fed in front of the machine from the side via a belt conveyor or side feeder. In the next step, the concrete is distributed evenly across the full paving width by a spreading auger or spreading plow. Built-in electrical or hydraulic vibrators ensure homogeneous compaction of the concrete. The inset mold forms the concrete surface to the specified thickness and width while the slipform paver travels forward. In addition, a dowel bar inserter can be added which inserts the dowel bars into the concrete as specified parallel to the paver’s direction of travel. Central tie bars or side tie bars can be inserted perpendicular to the road surface. The oscillating beam scrapes the surface across the roadway. The “grinding movement” produces a small concrete roll in front of the beam which enhances the high quality of the concrete surface. Afterwards, a super smoother can smooth the concrete surface.
Flexibility for Concrete Paving
The innovative system for extending the working width enables fast and convenient on-site reconfiguration of the paving mold. The result is shorter reconfiguration times and maximum machine utilization rates while maintaining the usual high quality.
The WPS 62(i) placer speader is normally used in combination with a slipform paver and a texture curing machine. While trucks and semitrailers successively dump concrete into the conveyor belt unit’s large receiving hopper, the conveyor belt guides the conveyed material to the center of the road. The WPS 62(i) placer speader uses a spreading auger to spread the laid concrete and paves it uncompacted with a narrower width and greater thickness than the following slipform paver. Finally, the paver paves the pre-poured concrete in the required width and thickness together with the pre-laid reinforcement. To complete the process, the texture curing machine produces a defined surface structure and sprays evaporation protection onto the fresh concrete road surface.