- Length of reference section:
- 500 m
- Paving width:
- 3.6 m
- Total BSM layer thickness:
- 26 cm
- Thickness of paved surface layer:
- 4 cm
- Performance data KMA 240i
- 1,250 t of BSM in 5 hours
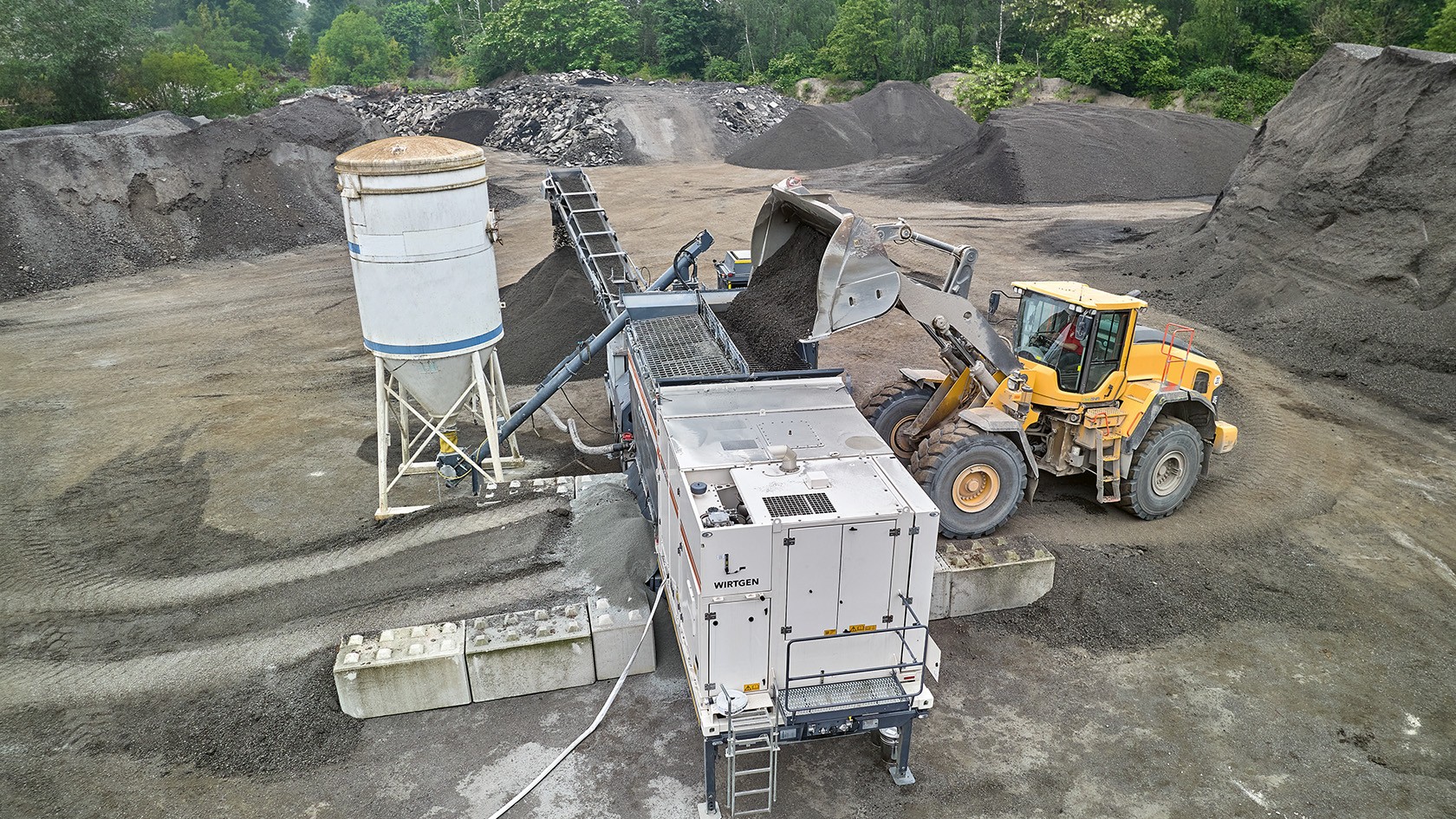
An extremely ambitious reference project
Cologne | Germany: The slogan ‘Work On Progress’ is prominently displayed everywhere on STRABAG construction sites. With this campaign, STRABAG communicates its goal of climate neutrality along the entire value chain by 2040. Innovative projects with this goal in mind are being promoted in all segments of the company.
A complete rehabilitation of a 2.5 km section in both directions was carried out on the A 555, Germany’s oldest autobahn. The overall construction time was estimated to be more than 18 months. At least two lanes were to be kept open to traffic to avoid serious traffic congestion in the region. The hard shoulder was to be reconstructed as a heavy vehicle lane with the highest load class of BK100 With conventional paving methods, this would have involved: milling, removal and disposal of all asphalt layers. Stabilisation of the road bed. Reconstruction of the asphalt base layer, asphalt binder course and asphalt surface course with sufficient load bearing capacity.
In conventional asphalt paving, the most significant sources of CO₂ emissions are, on the one hand, the production of the new asphalt layers and, on the other hand, the trucks used for transporting material to and from the site. This is where the cold recycling method from Wirtgen offers savings potential. In contrast to the conventional construction method, bitumen-stabilised material (BSM) produced in a mobile cold mixing plant from Wirtgen was used here for paving the new base layer of the autobahn. ‘What Wirtgen is offering us here with its cold in-plant recycling method is an exceptionally advanced process,’ says Stephan Ehlers, Technical Manager, STRABAG AG (Düren Region).
STRABAG AG used a 500 m section of the hard shoulder as a reference project. All material sampling, mix analyses and compaction tests were carried out by the in-house TPA testing lab. Due to the good international testimonials, STRABAG AG wanted to determine the permanence and load-bearing capacity of BSM when paved as a base layer with a load class of BK100.
The Wirtgen cold mixing plant KMA 240i produced the mix for the BSM base layer from reclaimed milled asphalt with the addition of foamed bitumen and cement. The most significant reduction of CO₂ emissions achieved here was a result of the cold processing of the mix. Alone the bitumen was delivered at a temperature of 180°C and then processed together with water and air to produce foamed bitumen. All this eliminated the need for energy-intensive heating of the aggregate fractions or the granulated asphalt.
Thanks to its high mobility and a relatively small footprint, it was possible to set up the KMA 240i at a close and logistically favourable distance from the construction site. This enabled the reduction of a large proportion of the emissions resulting from material transport.
The advantages and benefits of cold recycling at a glance
Up to:
Learn more about cold in-plant recyclingUsing BSM for the base layer on major roads and highways is nothing new around the world and is meeting with increasingly interest and popularity in Germany. Suitability testing of the cold recycling mix for the base layer was carried out by STRABAG AG (Düren Region) with the assistance of Wirtgen in its own construction materials testing lab. When appropriately formulated, the mix is suitable for all traffic loads. The volumes of the binding agent and aggregates to be added was determined in preliminary trials. Reclaimed asphalt pavement with 25% crushed sand for the filling of fines, plus 1% cement, 2% foamed bitumen and water yielded positive synergies for the sustainable mix.
‘We can make process flows considerably more effective and faster with bitumen-stabilised material. In view of our expressed commitment to achieving climate neutrality by 2040, we have a vested interest in the further development of what we have learned from this project.’
Stephan Ehlers, Technical Group Manager STRABAG
The KMA 240i enables continuous production of 240 t of cold mix per hour. BSM mix can be stockpiled and thus enables more flexible site logistics. This also means that mix can be produced at any time and temporarily stockpiled until needed. The mix remains pavable and, in contrast to conventional mixes, does not need to be laid down almost immediately after production.
The BSM base layer was paved over the pre-prepared road bed in two separate layers to achieve the specified degree of compaction. To ensure uninterrupted paving, a Vögele MT 3000-3i mobile feeder successively transferred more mix to the hopper of the Vögele paver following on behind. The Vögele Super 1900-3i paver took over the true to grade and slope paving of the new base layer to a working width of 3.6 m. The first layer of cold mix paved had a thickness of 16 cm and the second layer, paved the next day, a thickness of 10 cm. Following pre-compaction with the AB 500 screed, each of the cold mix layers was ideally compacted by an HD+ 140 tandem roller and an HP 280i pneumatic-tyre roller from Hamm. According to Stephan Ehlers, ‘the compaction values determined by TPA were more than satisfactory.’ On the construction site, the cold recycling mix fulfilled all the requirements determined by preliminary testing.
As the final step in the process, the BSM mix was paved over with a new asphalt surface layer (SMA 11 S) with a thickness of 4 cm.
BSM mix is firmly established as a field proven paving material in many countries around the world and is used for all load classes. As cold recycling mix can actually extend the service life of roads, it can be considered to be a particularly sustainable material. In a comparison with conventional construction methods, the advantages and benefits of its use are more than obvious.
For STRABAG AG, the success of this project also ties in with its corporate philosophy and smooths its path on the way to climate neutrality. ‘The advantages and benefits in comparison with conventional construction methods are clearly identifiable and should be taken into consideration in future projects. The exception should become the rule when it comes to establishing advanced construction methods’, concludes Stephan Ehlers.
Press/media kit
Click here to download a ZIP file containing the press release in the available languages in Microsoft Word format and the images in 300 dpi resolution.
Download