In comparison, conventional asphalt paving would have involved milling off the entire road surface in several stages and then widening and repaving the roadway from the ground up. In-place cold recycling eliminated all these separate steps. Foamed bitumen and cement were added to the existing asphalt material and processed in-place to produce an as-new BSM base layer. The old road surface was milled off by the W 380 CRi to a depth of 15 centimetres. Around 300 t of material per hour were transferred to the Vögele SUPER 2100-3i paver next in line, which laid the new pavement profile with a width of 5.5 m and a depth of 12 cm, all in a single pass. The cold recycling train worked at a speed of 4 m/min along the 3 km section of the Sinding Hedevej. As soon as the Hamm rollers had taken care of the final compaction, the road was able to be temporarily reopened for local road users.
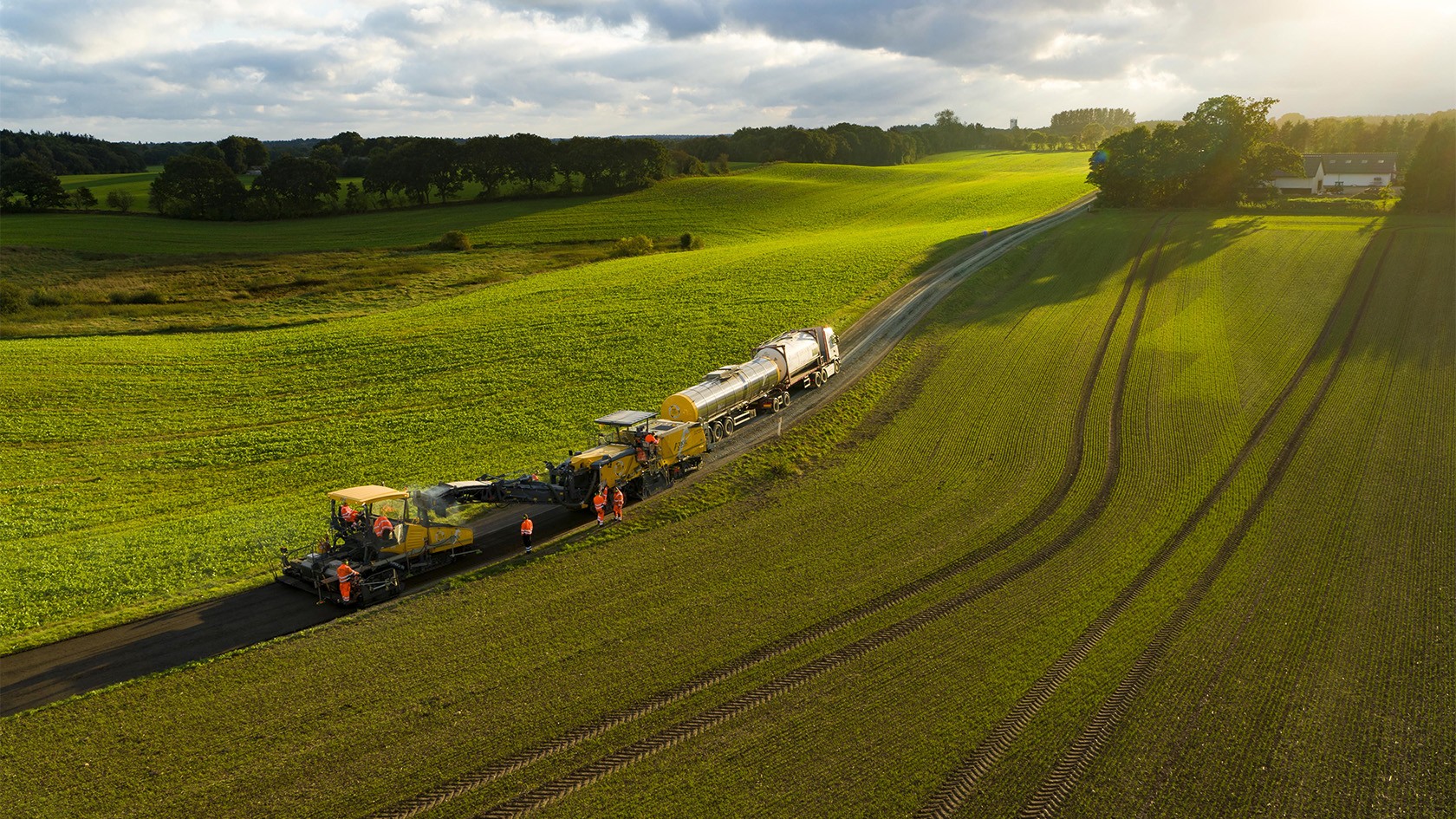