- Feed material
- Lime sand brick mixture
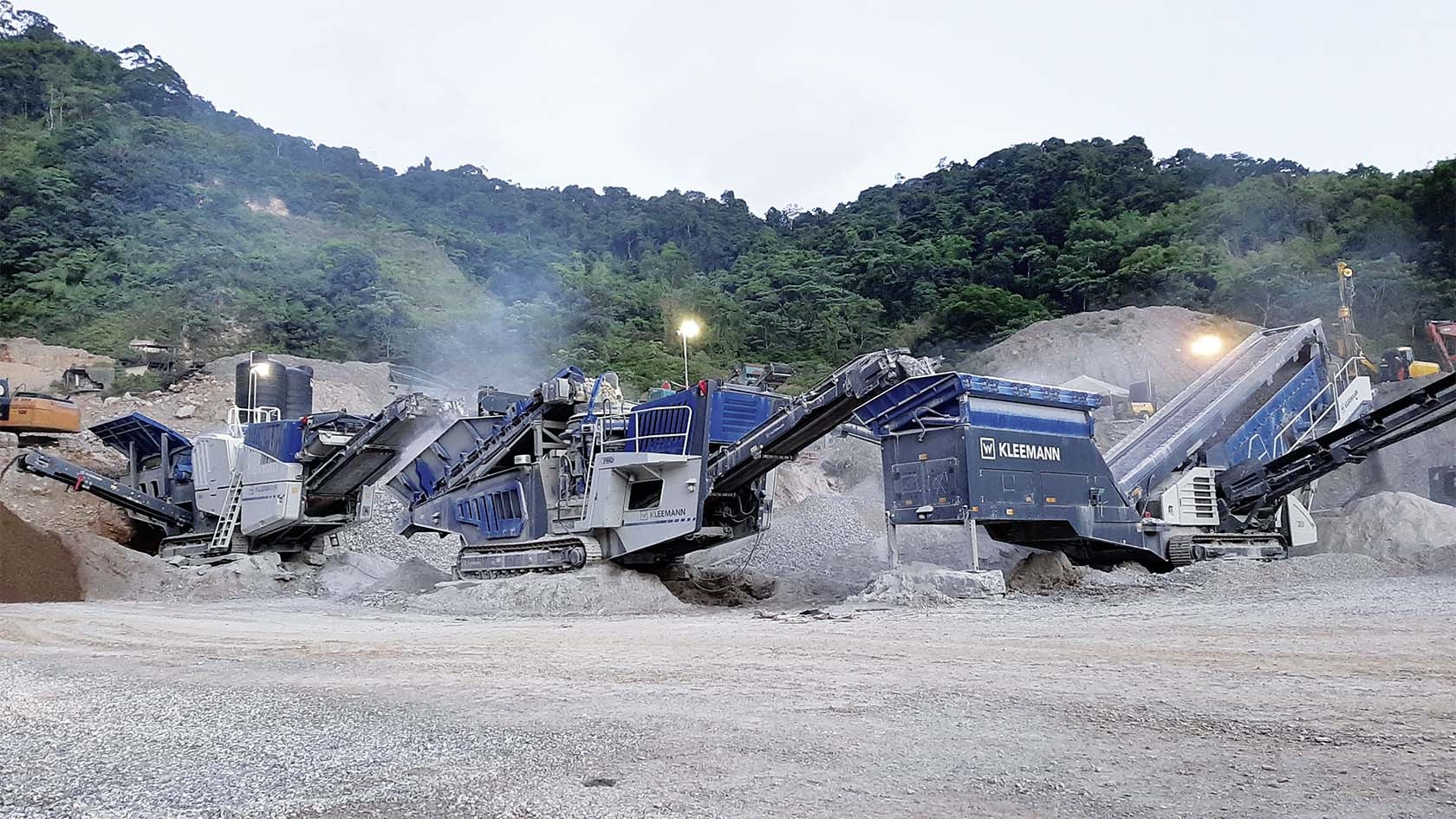
Coupled plant train impresses in limestone
A PRO plant train from Kleemann has been in operation for Jusamco Ltd since October 2020 on the island nation of Trinidad & Tobago in the south Caribbean. The core of the plant comprises two PRO plants: the mobile jaw crusher MOBICAT MC 120 Z PRO and the mobile cone crusher MOBICONE MCO 11 PRO. The mobile screening plant MOBISCREEN MS 953 EVO rounds off the process. The plant train impresses with its high productivity and economy and produces final product for the production of asphalt.
Apart from numerous infrastructure projects of its own on the island of Trinidad – the largest island in the nation - Jusamco placed a strong focus on the export of aggregates to Guyana. In Guyana itself, work is currently under way on a large number of major infrastructure projects related to road and harbour construction, which have massively increased the demand for prepared stone material. Around 75% of the limestone mixture processed by Jusamco is exported to the neighbouring country Guyana.
The plant train of Jusamco in Trinidad: the core comprises the jaw crusher MOBICAT MC 120 Z PRO and the cone crusher MOBICONE MCO 11 PRO. The screening plant MOBISCREEN MS 953 EVO rounds off the complete process.
When selecting the plant technology, the decision fell on a PRO plant train from Kleemann. The factors that impressed the most were the high output, the very high quality of the final product and simple line linking of the individual machines to form a plant train. "The simple linking of the machines and the automatic processes of the individual plants tuned to one another made our operation a lot easier", says Kyle Parsons, project manager in charge at Jusamco. Added to this is the certainty "that we can expect excellent technical support and parts supply from our contact persons at Kleemann and Resansil, our local dealer. We already have machines from Wirtgen Group in our fleet and we were always completely satisfied with the local service."
"The simple linking of the machines and the automatic processes of the individual plants tuned to one another made our operation a lot easier".
Kyle Parsons, project manager in charge at Jusamco
The plant train consists of three machines whose technical processes are coupled to one another. This means that automatic control stabilises the complete process. Each machine basically operates independently but forwards signals to the upstream and downstream machines in the event of malfunctions or overfilling. The feed control Continuous Feed System (CFS) also guarantees optimum utilisation of the crusher. Ultimately, all components are loaded evenly.
The automated tuning relieves the burden on the operator and harmonises the process. The connection of all machines also guarantees safety: if an emergency-stop button is pressed anywhere on the plant train, all machines are safely stopped. This concept prevents damage or overload situations. All of this combined results in a high availability and output with low wear. The high output can also be quantified: compared to the plants that were previously used in the quarry, output has been doubled.
"In our eyes, the automatic control is a real positive factor. Such a plant train would normally require one operator per plant - plus the excavator driver. Thanks to the line coupling, we were able to divide the work between two operators: one who operated the complete plant train and an operator in the excavator. The two operators that were saved were able to deal with other tasks in the quarry, such as logistics or material provision," reports Kyle Parsons, "more effectiveness is hardly possible".
"More effectiveness is hardly possible."
Kyle Parsons, project manager in charge at Jusamco
After delivery of the new plants in September 2020, the project had to face the special challenge posed by the Covid-19 pandemic: the plant train had to be put into operation online without local supervision. Most countries in South America, as elsewhere, were in lockdown and travel was not possible. How well plant start-up functioned in spite of these adverse conditions was shown after a year: there were no significant problems and the machines and crushing tools revealed hardly any wear. On the one hand, the low wear resulted because the material was not so abrasive but, above all, due to a very finely tuned process and thus optimum material flow. "Of course we were worried at the start as to whether start-up and instructions on machine operation would work via video conference. Ultimately, we had no choice because the machines were there and we had to produce", says Parsons. But thanks to the commitment of all people involved at Kleemann and Resansil "start-up worked really well. Operation with SPECTIVE of course played a big role. Simple and intuitive - that really says it all."
The structure of the SPECTIVE operating system allows everybody to find their way intuitively. The visual presentation and simple user guidance make errors almost impossible. "Thanks to the simple operation, we were able to instruct several operators in SPECTIVE right from the start and now have total flexibility in plant operation."
After the first few weeks of operation, it quickly became clear: "The crushing and screening plants are very easy to access", reports Parsons. Jusamco attaches great importance to care of the plants. Regular maintenance is self-evident. "We can reach all areas and without significant disassembly work."
"The crushing and screening plants are very easy to access"
Kyle Parsons, project manager in charge at Jusamco
The simple screen surface change with the screening plant MOBISCREEN MS 953 EVO also impressed Jusamco. After all, apart from the aggregates for the production of asphalt mixtures of 0-50 mm are also partly prepared. This requires a conversion of the screen. Following consultation with Kleemann experts, the time required for this conversion was reduced from approx. 5-6 hours to 3 hours: only the screen surface in the upper deck has to be replaced completely; in the middle and lower deck, only the last sections are removed. Not only the work time and thus the downtime were reduced, but wear on the screening plant was also further optimised.
"We are very satisfied with our contact partners at Kleemann and Resansil. Above all, we appreciate the readiness to find practical solutions. We have already experienced this excellent co-operation with the other brands from Wirtgen Group.“
Press/media kit
Click here to download a ZIP file containing the press release in the available languages in Microsoft Word format and the images in 300 dpi resolution.
DownloadDetails and further information can be found on our product pages.