Plant train consisting of the jaw crushers MOBICAT MC 120i PRO and MC 110i EVO2, the cone crusher MOBICONE MCO 90i EVO2 and the screening machine MOBISCREEN MSC 953i EVO in the limited space of the quarry.
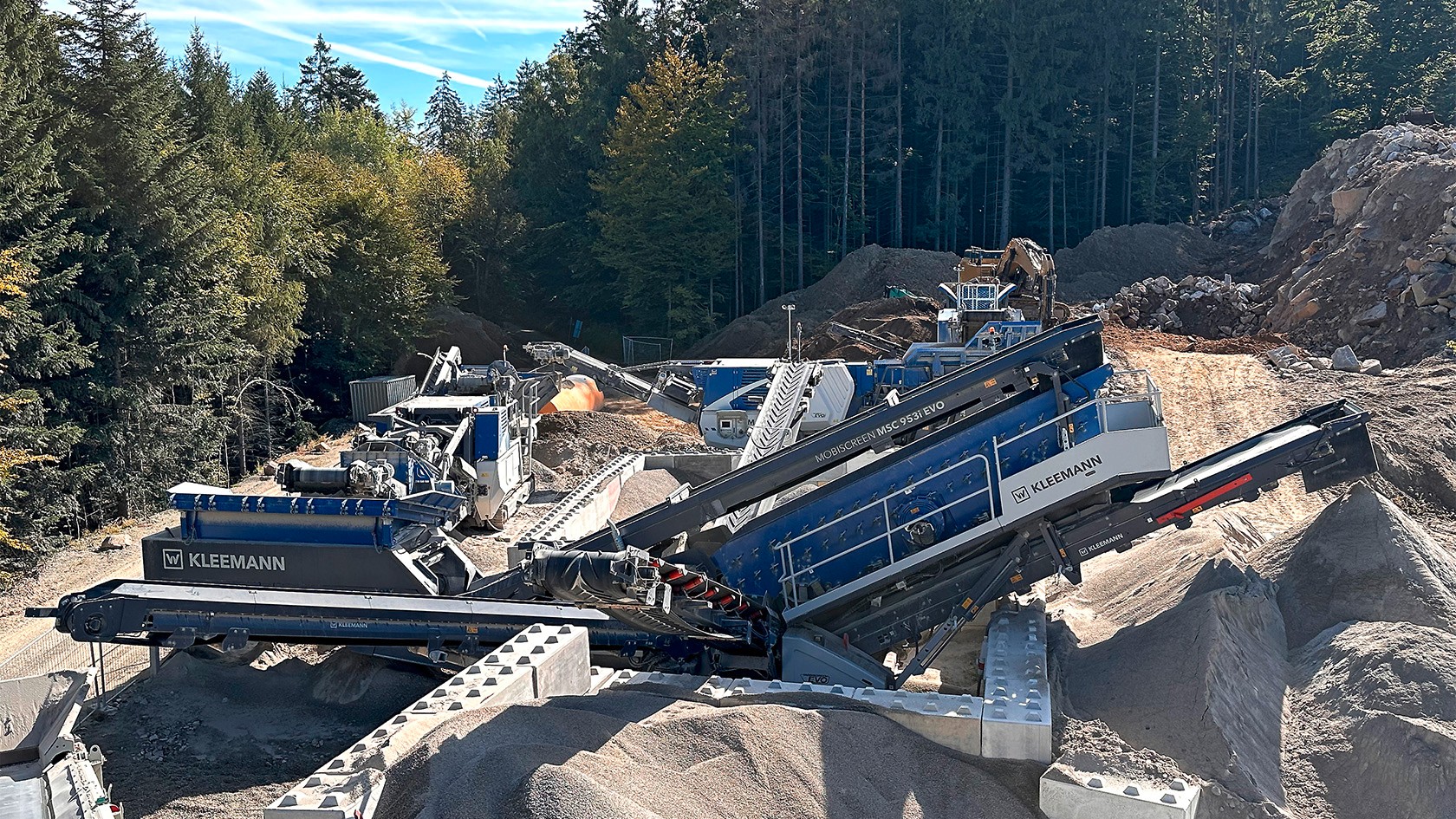
A perfectly tuned plant combination now utilises large volumes of excavated material in the Bavarian Forest
In a quarry in the Bavarian Forest, the paving specialist Godelmann crushes granite into fine grit. The material on site is extremely hard and abrasive. After a series of tests, the end result was achieved with a slightly unusual compilation: Two jaw crushers, one cone crusher plus a screening plant.
Godelmann, with its head office in Fensterbach, Bavaria, is one of the big players in the production of paving stones. The subject of sustainability is central to the company throughout the entire production process, which was underscored in 2023 with the presentation of the German Sustainability Award. It is self-evident that the company has placed a special focus on transparent and sustainable supply chains, starting with their own regional production of raw material.
Plant train consisting of the jaw crushers MOBICAT MC 120i PRO and MC 110i EVO2, the cone crusher MOBICONE MCO 90i EVO2 and the screening machine MOBISCREEN MSC 953i EVO in the limited space of the quarry.
When an opportunity arose in the Bavarian Forest to process excavated material that had accumulated in a granite plant quarry belonging to the Bavarian Forest Administration, Bernd Godelmann and company management together with the Technical Manager Josef Regler grasped the opportunity. Up to now, a stonemason from the region has been removing freestone to produce large granite products such as worktops or gravestones. This extraction produced huge amounts of residual material that could no longer be used for his purposes – extremely hard and extremely abrasive. “Up to now, no company was really prepared to process this material” explains Andreas Wagner, Kleemann expert from Wirtgen Germany, “plus the fact that quarry location is not at all ideal.” The site is in the middle of a forest. Access for large machines is a challenge and the space on the site is very restricted.
Kleemann expert from Wirtgen Germany Andreas Wagner (left) and the Technical Manager at Godelmann Josef Regler (right) before the Kleemann plant train.
“The present-day result was reached after numerous tests. The Kleemann technicians worked intensively on the whole process and together we honed and optimised it. And now we have a solution that is perhaps unconventional, but which functions perfectly.”
Josef Regler, Technical Manager at Godelmann
Godelmann recognised the opportunity with this quarry to further expand the regional raw material supply. The idea of utilising the previously unused excavated material also fitted into the sustainability strategy of the company. And the flexible, mobile Kleemann machines could be the solution to this extraordinary task!
After contact was made with the Kleemann process technicians, an elaborate test series was started. Today, a Kleemann plant train is set up in the quarry that crushes the hard material into the desired 0-16 grit – the invested effort achieved the desired result. “Kleemann Process Technology really carried out fantastic work here”, says Josef Regler. “The present-day result was reached after numerous tests. The Kleemann technicians worked intensively on the whole process and together we honed and optimised it. And now we have a solution that is perhaps unconventional, but which functions perfectly.”