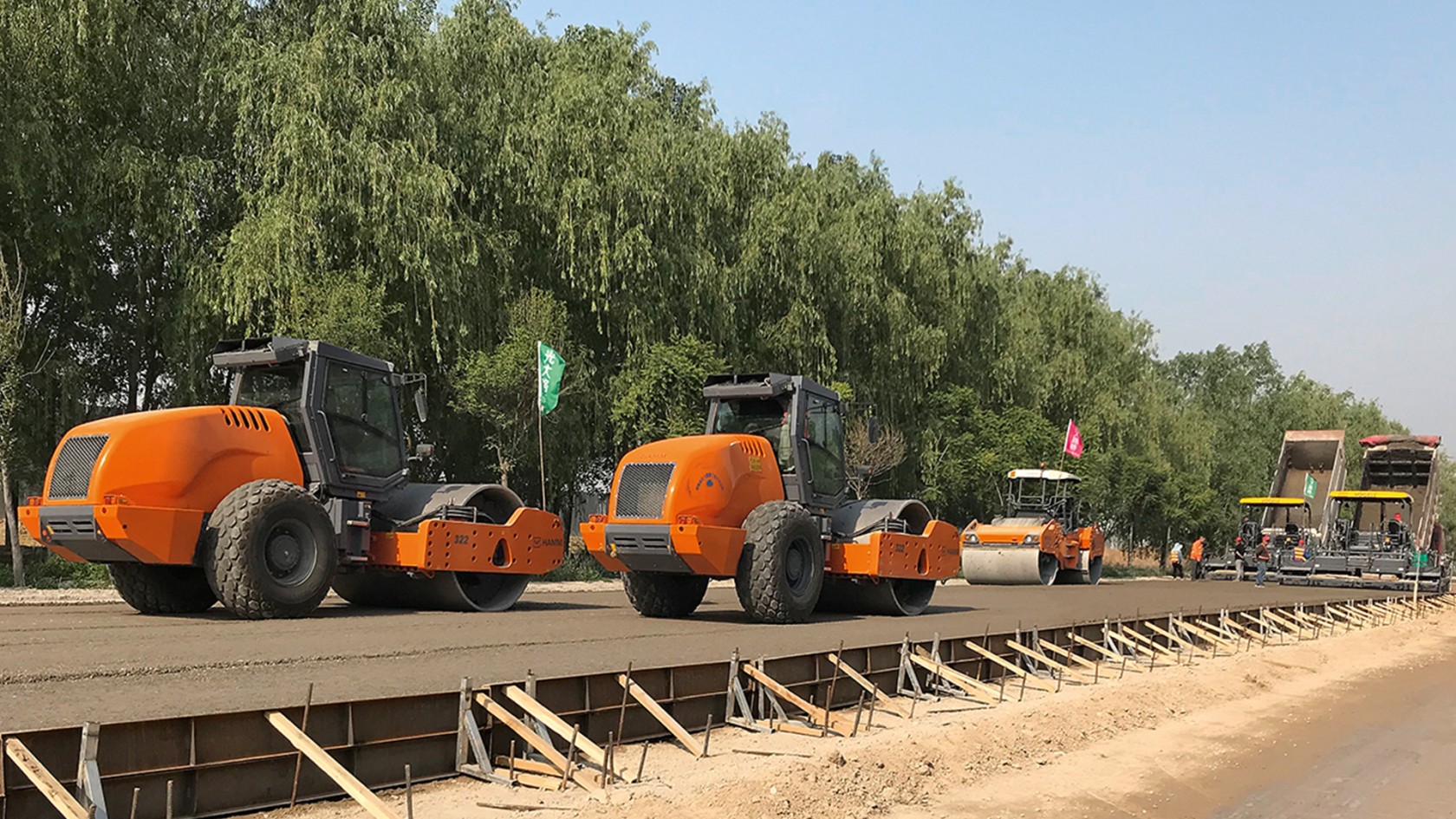
In Henan province, close to the Yellow River, two HAMM 322 compactors proved their outstanding performance by successfully building a cement treated base course (CTB) up to 50 cm thick. This type of compactor is manufactured in the WIRTGEN GROUP’s China-based factory in Langfang and has been tailored to meet the needs of Chinese customers.
The S101 Mazhuangqiao section, located in Qingfeng county in the Puyang municipality of Henan province, was severely damaged by heavy traffic. This resulted in bumps, ruts, cracks etc. having a negative impact on driving comfort and safety. The local government decided to upgrade a part of this provincial road to the G342 national road. The total length of the section in question is 2.5 km. Eventually, it will be a road with four lanes in both directions. For the rehabilitation process, the damaged top layer and the 36 cm-thick CTB layer were milled off first. The next step was to pave a new CTB course which was 50 cm thick before compaction and 36 cm thick afterwards. It was subsequently covered with a new wearing course. CTB courses with a total final thickness of 36 cm are usually built in two layers, each 15-20 cm thick. The main reason for this procedure is the ease with which compaction quality can be controlled. But there was an additional challenge on this project: time. The time frame was limited, so the contractor decided to pave the 50 cm-thick CTB course in one pass, taking advantage of higher working efficiency and lower costs.
High performance for efficiency and quality
Compared to the traditional paving method, the construction of such a thick layer has several advantages: the integrity of the pavement is improved, the pavement construction process is simplified and construction time is saved. Whilst the procedure of paving such a thick CTB is simple, its quality control becomes a challenge. Other factors affecting quality, such as the evenness of the ground, aggregate grading and water content, the performance of the pavers and compaction performance become key factors when completing such a project. The contractor, Henan Guangda Road & Bridge Engineering Co., decided to use a WIRTGEN GROUP fleet composed of two VÖGELE SUPER 1880 L multifunctional pavers equipped with an SB 300 HDT screed specially designed for paving cold materials in thick layers. A HAMM HD 138 tandem roller and two HAMM 322 soil compactors were used for compaction. The two SUPER 1880 L pavers paved the CTB course side by side with a total paving width of 9.5 m and a paving thickness of 50 cm. After the HAMM rollers had completed their work, the CTB course was successfully compacted to a thickness of 36 cm.
Compaction speed of 3 km/h at high amplitude
In Puyang, a high compaction efficiency was essential, which was why the contractor defined a specific roller plan to achieve the ideal compaction degree. The first machine – the HAMM HD 138 tandem roller – was responsible for preliminary compaction. The roller applied static pressure in the forward direction, and compacted in vibration mode at high amplitude during reverse travel, only once back and forth. Then two HAMM 322 compactors followed for second ary compaction, completing three passes in vibration mode at high amplitude plus three passes at low amplitude with a compaction speed of 3 km/h.
Hydraulic drive makes the difference
A closer look at compaction performance shows that the hydraulic drive of the HAMM compactors is key to the big difference when compared to mechanical or semi-mechanical single-drum vibratory compactors. These machines are not able to meet the requirements when compacting CTB with a thickness of 50 cm. The 22 t fully hydraulically-driven HAMM 322 compactor is able to do this as it features a different weight distribution. The front section, i.e. the drum part, can reach a weight of about 15 t. Mechanical or semi-hydraulic compactors cannot distribute that much weight to the front section, because they need the weight in the rear part of the machine for traction. In the 22 t class, the drum can only be applied with a maximum of 50% of total machine operation weight, namely 11 t. This means that the HAMM hydraulic compactor has a much higher static load. Combined with its powerful vibrator, it performs far better and more efficiently than models of the same (or even higher) weight classes with mechanical or semi-hydraulic drive.
Even surface
Another advantage of the 322 compactor is the evenness of the surface. As its hydraulic drive starts and stops the compactor smoothly, effects such as undulations, for example, are avoided. These are often caused by mechanically or semi-hydraulically driven compactors starting and stopping. The resulting evenness and bearing capacity of the CTB course, achieved thanks to very efficient compaction by the HAMM 322, was an excellent foundation for the subsequent asphalt paving. Results of analysis of the drilling core samples from the test section were good, showing that the required compaction quality was delivered. All in all, the VÖGELE pavers, HAMM rollers and HAMM compactors worked together very efficiently, enabling Henan Guangda Road & Bridge Engineering Co. to complete construction of the 50 cm-thick CTB course of this section successfully in not much more than a week. As bearing capacity met project requirements, the customer was once again convinced by the outstanding performance of VÖGELE pavers and HAMM compactors.
VÖGELE SUPER 1880 L with 1,000 t/h laydown rate
Paving a 50 cm-thick base course requires extremely powerful and durable pavers. The VÖGELE SUPER 1880 L is well-known as a powerful multifunctional paver for cement-treated base courses and asphalt. Its long extended hopper with a maximum capacity of 15 t permits fast unloading of trucks while its powerful conveyor system delivers a high through-put rate and continuous material flow. These features enabled the two SUPER 1880 L to do a very good job when paving the 50 cm-thick CTB course in Qingfeng county.