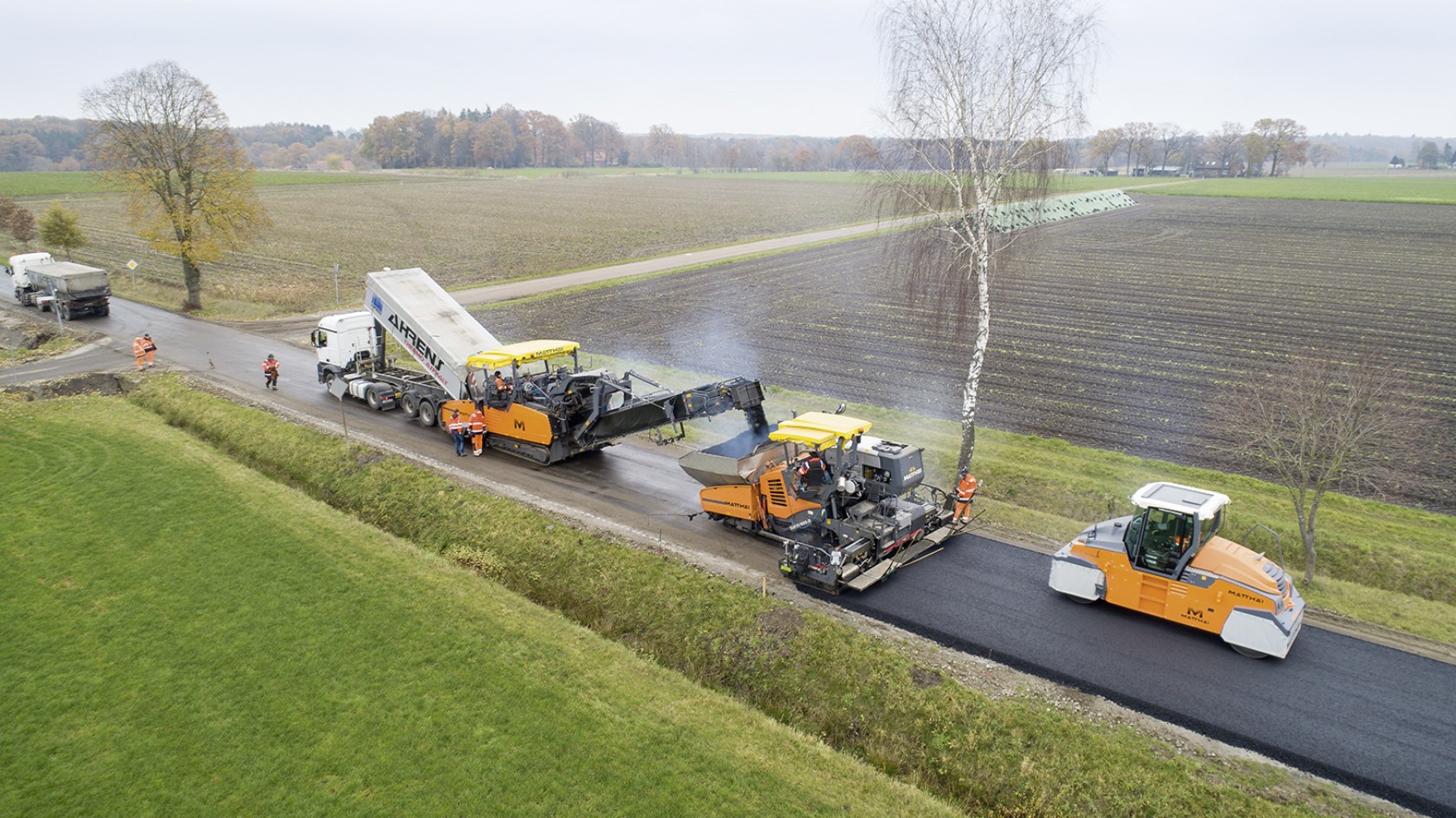
The joystick for operating the conveyor allows it to be pivoted accurately to either side and handles very conveniently. Users are enthusiastic.
Mr Delventhal, how has the new material feeder been doing on your job sites so far?
Really well. We use the material feeder for various projects - building major roads, trial sections or for smaller-scale projects, for example. Regardless of whether the job site is large or small, it makes processes more efficient, prevents demixing and thus increases the quality of the asphalt courses. As the construction manager, these are key factors for me.
So what does your paving crew have to say about the new machine?
The operators especially appreciate the user-friendly nature of the new Dash 3 generation, the ErgoPlus 3 concept. The clear operating console, intuitive operation and automatic functions save time and prevent errors, allowing my colleagues to concentrate on transferring the mix. An especially practical feature is the automatic conveyor with its proportionally-controlled primary and secondary belts or the laser distance control which controls the speed of the material feeder automatically to suit the speed of the paver. The entire operating concept just satisfies users’ requirements really well: the joystick for operating the conveyor allows it to be pivoted accurately to either side and handles conveniently. These kinds of details matter in the routine working day.
And what do machine technology and performance look like?
We have found these, too, to be convincing so far. The material feeder, for example, drives very well straight ahead and has a low-noise drive - important points for my paving team. With an output of up to 1,200 t/h, the material feeder is also a true workhorse.
Ring road K121 in Schneeheide (near Walsrode in Lower Saxony) was severely deformed and cracked. The carriageway was also too narrow for oncoming traffic, so the objective was to rehabilitate and widen the road.
Contractor Matthäi first paved the 10 cm-thick base layer 5.6 m to 6 m wide for 2.1 km using a SUPER 1800-3i SprayJet, then paved the 4 cm-thick surface course.
Supported by the VÖGELE MT 3000-3i Offset material feeder, paving went very quickly and without any paving interruptions.