Crushing technology
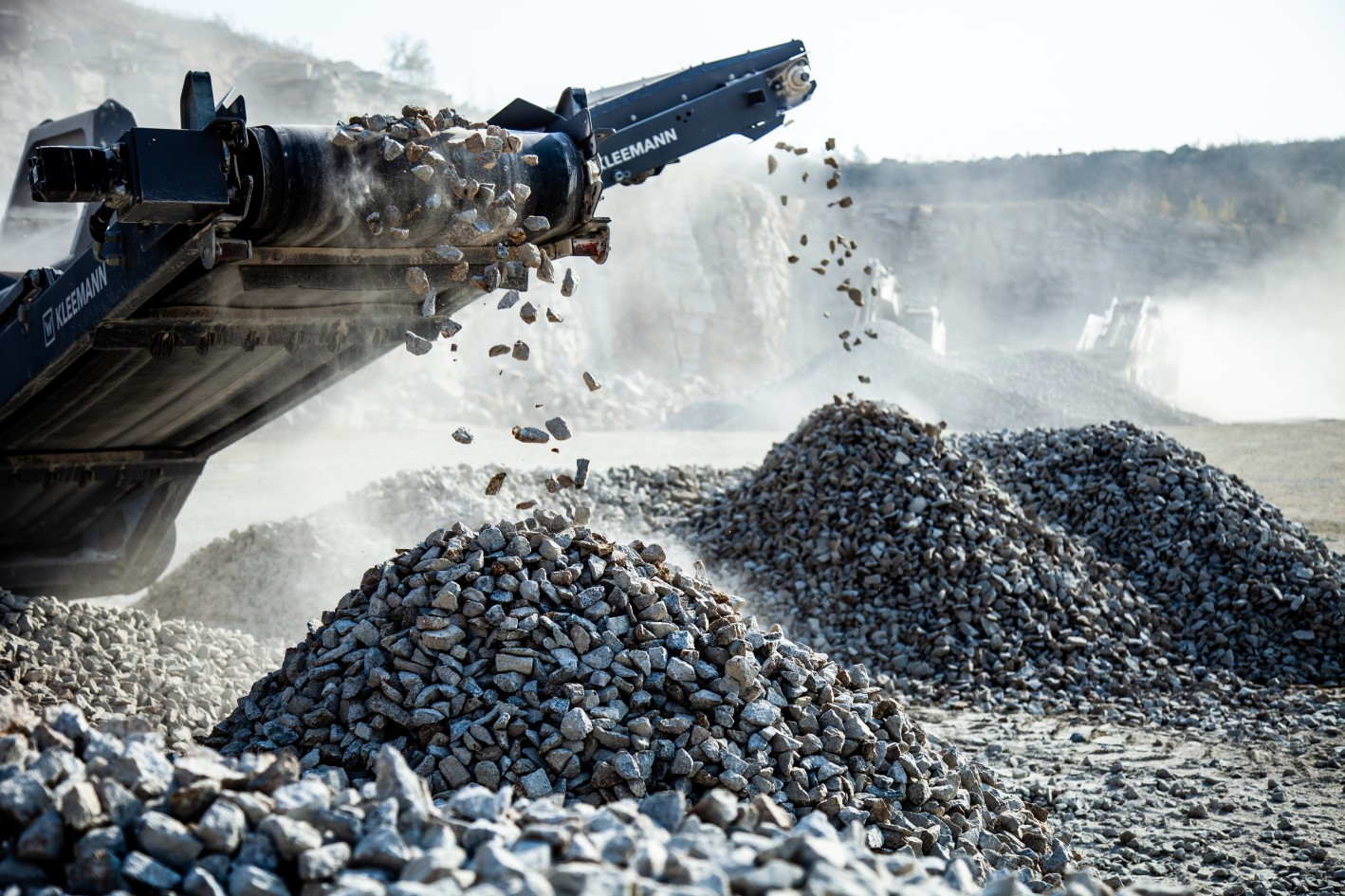
Feed material, required final product and cost-effectiveness influence the selection of the crushing technology.
The quarrying of natural stone types is associated with the use of machines that crush material with high compressive strengths systematically and effectively. Jaw crushers are ideally suited for tough applications in quarries and are mainly used as primary crushers.
Jaw crushers operate according to the principle of pressure crushing. The crushed material is crushed in the wedge-shaped pit between the fixed crusher jaw and the crusher jaw articulated on an eccentric shaft. The material is crushed by the elliptic course of movement and falls down due to gravity. This occurs until the material is smaller than the set crushing gap.
The crushing energy acts on the feed material with strong forces and a low speed. The name jaw crusher is derived from the crusher jaws necessary for crushing and the "chewing" motion.
Jaw crushers are used for coarse and primary crushing of brittle, medium-hard and hard stone. They are used most frequently as primary crushers.
Jaw crushers are not usually capable of producing a final product that meets the standards. In some recycling applications, small jaw crushers can be used to produce crushed base layers for secondary road and path construction.
Cone crushers are the choice for use in medium-hard to hard and abrasive natural stone as well as for raw material preparation in mining applications. The cone crushers deliver cubic final grain sizes in the 2nd and 3rd crushing stage that meet the standards.
The cone crushers are available in different sizes, versions and for various applications.
Cone crushers crush the feed material in a circulating opening and closing crushing gap between bowl liner and crusher cone. Opening and closing also takes place simultaneously on the opposites sides of the crushing chamber.
Cone crushers are available in different designs. With the cone crushers used by KLEEMANN, the crusher shaft is press-fitted into the main frame. The crusher cone carrier is mounted on an eccentric power supply unit. The rotation of the power supply unit opens the gap in a circulating movement between crusher cone and bowl liner. Raising and lowering of the bowl liner changes the grain size to be produced.
Cone and gyratory crushers are mainly used when impact crushing is no longer possible due to the high compressive strength of the crushed material, or the wear costs due to the abrasiveness of the stone are not economically justified.
Due to their design, cone and gyratory crushers are limited with regard to the feed size and the achievable reduction ratios.
On mobile plants, cone crushers are used predominantly in the secondary and tertiary crushing stage.
Gyratory crushers differ from cone crushers with regard to their design.
In contrast to the cone crusher, which has a fixed shaft on which the power supply unit and the head rotate, the gyratory crusher has a main shaft that can be moved hydraulically in vertical direction on which the head is permanently shrink-fitted. The shaft is supported axially at the bottom end on a thrust bearing, which, in turn, is mounted on the adjusting piston. The crushing gap adjustment is made by raising and lowering the adjusting piston and thus also the main shaft. At the upper end, the horizontal crushing forces are introduced to the upper section of the crusher via the head bearing, which is integrated in a transverse member, the so-called "spider".
Due to the design, the height of a gyratory crusher is generally considerably greater than that of a comparable cone crusher.
THE POWERFUL ALL-ROUNDER
Whether in a quarry or on a construction site, impact crushers crush stone so efficiently that the grain shape, grain size distribution and cleanness comply with the strict standards for concrete and asphalt aggregates. The impact crushing plants not only achieve a first-class product quality but also a remarkable throughput.
In contrast to pressure crushing, the impact crusher operates according to the impact crushing principle. In this process, the crushed material is picked up by a fast moving rotor, greatly accelerated and smashed against a fixed impact plate ("impact toggles"). From there, it falls back within range of the rotor. The crushed material is broken again and again until it can pass through the gap between the rotor and impact toggle.
The actual crushing process takes place when the stone contacts the rotor ledges and the impact toggles. Crushing also takes place as a result of contact between the stones themselves.
Impact crushers are used as primary and secondary crushers. As primary crushers, impact crushers are used in limestone mainly where a high content of fines, good cubicity and angularity and a high output are required.
In modern recycling of concrete, asphalt and rubble, thanks to their high output and excellent final product quality they are indispensable. In contrast to pressure crushing, they are able to extract all reinforcing steel from the concrete and thus achieve a largely iron-free final product.
As secondary crushers, they are often used behind jaw crushers to create final products that meet the standards.
Impact mills are usually used when the final product to be created is to have a grain size of only up to approx. 10 millimetres. Impact mills are often used for recrushing in the third and fourth crushing stage because the feed sizes have to be correspondingly small.