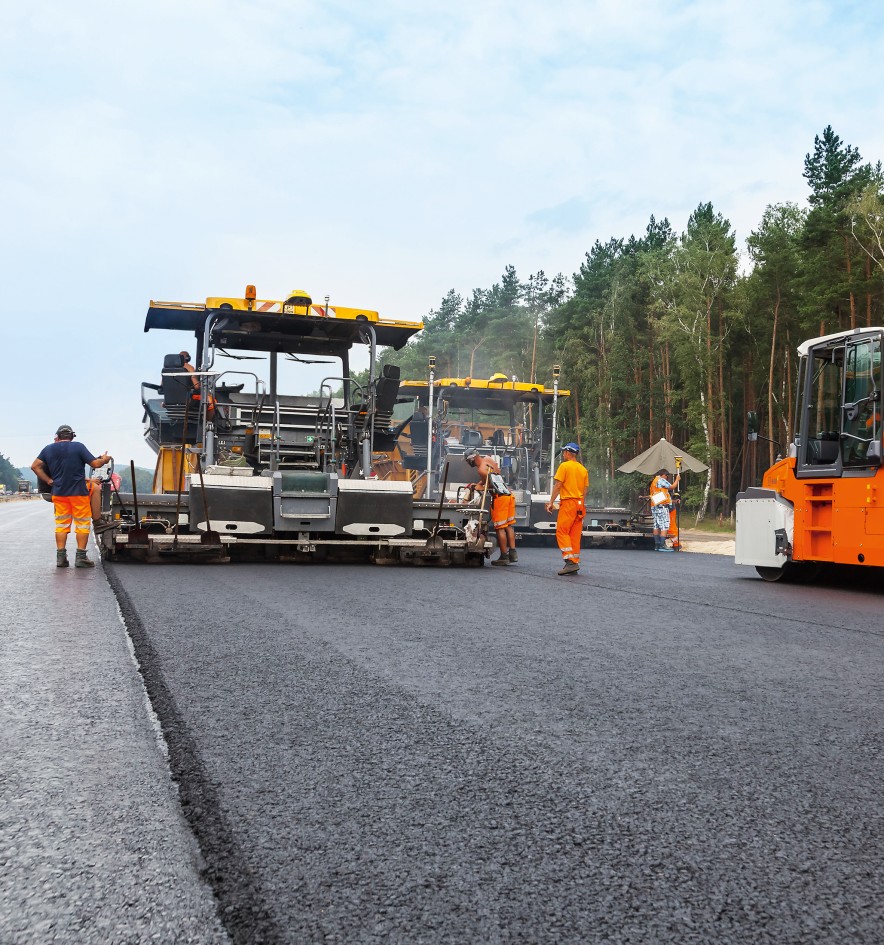
Expansion of the Berlin ring road: when widening the trans-European motorway, the team frequently had to move between many small job site sections. AutoSet Plus, the automatic functions of the SUPER pavers, provided invaluable support for the paving team.
Germany | Berlin
A construction project with many small sections: during the widening of the A10 motorway ring road around Berlin, the paving team from Johann Bunte Bauunternehmung GmbH & Co. KG frequently had to move their machines on the job site. This was a challenge since different machine settings were required after virtually every move. Entering these each time would take time and would also be a potential source of errors. And this is why this motorway job site impressively highlighted the benefits of the AutoSet Plus Paving Programs: the automatic functions for SUPER pavers ensure paving quality at the press of a button.
Motorway job site in greater Berlin: during the project near Potsdam, the AutoSet Plus Paving Programs function helped the paving team to ensure that they were always working with the correct machine settings.
AutoSet PlusThis is AutoSet Plus
The innovation for the SUPER pavers of the “Dash 3” generation allows procedures to be automated and make the paving process more efficient – and all at the press of a button on the paver operator’s ErgoPlus 3 console. It is important to distinguish between two basic functions:
1. The Repositioning function
Automatic repositioning accelerates the resumption of work after the paver has been moved on the job site or when there is a change of work shifts, for instance. Paving-related paver settings are stored for later retrieval.
2. The Paving Programs
When paving programs are created, all the settings and paving parameters of relevance for a particular job site are saved. This ensures that the data will be available for comparable projects in the future and can be called up at the press of a button.
Extending over 196km, the A10 motorway – also known as the Berlin ring road – is the longest motorway orbiting a European metropolis. A large proportion of the goods and passenger traffic to and from Poland and other eastern European countries uses it to bypass Berlin. Many commuters use the road, too. One of the most heavily used sections lies between the Potsdam and Nuthetal junctions southwest of the German capital. The volume of traffic on this 9km stretch is tipped to rise from 90,000 to 126,000 vehicles a day by 2025, around a quarter of them heavy goods lorries. In response to this, the A10 is being widened to eight lanes over this stretch. Traffic will continue running on six lanes alongside the job site until the project is complete. The sequence is as follows: first, the three existing westbound lanes will have to be removed entirely. Four new lanes are then to be built from scratch, with the eastbound carriageway is next in line. The project will increase carriageway width to 18.5 m.
Time was in short supply when implementing this project near to Berlin. Indeed, so little time was available that, to ensure adherence to the schedule, the carriageways had to be widened with interruptions, because the bridges and underpasses had to be extended or likewise built from scratch simultaneously with the construction of the road. That meant that the paving team of the contractor Johann Bunte Bauunternehmung GmbH & Co. KG frequently had to move between strips, as well as between the different sections, while also paving a variety of mixes – sometimes within the same work shift.
AutoSet Plus – which was a great support to the Bunte team on the Berlin motorway job site, helping them meet the specified quality parameters – is the ideal choice for construction projects like this. AutoSet Plus is easily and intuitively operated from the paver operator’s ErgoPlus 3 console. The Paving Programs function enables AutoSet Plus to automate the work processes – not only saving time, but also improving the paving quality. The function was used on the A 10 motorway because it allows all settings and paving parameters to be saved and then retrieved once the paver has been moved. As a result, the processes on this job site, with its numerous separate sections, were significantly more efficient and convenience for the team was increased.
Short sections, identical paving scheme: paving was carried out in three strips which were laid down one after another as follows:
Strip 1: the first strip of the base courses was laid by the SUPER 2100-3i – true to line and level thanks to Navitronic Plus from VÖGELE.
Strips 2 and 3: after repositioning, the SUPER 2100-3i also laid the outer strip with Navitronic Plus, working in a team with the SUPER 1900-3i – in a “hot to hot” process.
The SUPER 1900-3i used multi-cell sonic sensors from VÖGELE for grade and slope control, as the precisely paved strips on the right and left could be used as a reference.
Strip 1: SUPER 2100-3i with Navitronic Plus
Strip 2: SUPER 2100-3i with Navitronic Plus (“hot to hot”)
Strip 3: SUPER 1900-3i scanning on the left and right with multi-cell sonic sensors (“hot to hot”)
Other innovative technology from VÖGELE was also used, in addition to AutoSet Plus. To ensure the pavement was true to line and level exactly as specified in the planning data, the SUPER 2100-3i was equipped with Navitronic Plus from VÖGELE. The 3D control system assumes grade and slope control – automatic control of grade and crossfall – while also controlling screed position. Navitronic Plus additionally controls the steering of the VÖGELE tracked pavers. VÖGELE is the only company that can offer this advantage to its customers. To provide a virtual reference, an mmGPS system from TopCon (3D zone laser and GPS) was used on the Berlin ring road. This ensured maximum precision to line and level – likewise automatically. The paving result was documented with innovative technology, too. Both SUPER pavers were equipped with equipped with VÖGELE’s RoadScan temperature measurement system.
Technology that thinks for itself: Navitronic Plus, VÖGELE’s 3D machine control system, takes care of the steering, while controlling grade and slope as well as screed position.
“We’ve delivered first-class work on the A10. We were greatly helped not only by AutoSet Plus, but by other cutting-edge technology from VÖGELE, too – especially RoadScan and Navitronic Plus.”
Jürgen Schimang, Asphalt Coordinator Johann Bunte Bauunternehmung GmbH & Co. KG
However, of all the technologies employed, AutoSet Plus was the most important on the job site: after all, the section is being widened to 18.5m in each direction, which is why the bridges along the route also need to be replaced. As a result, the job site is split into many different sections of relatively short length, over which the entire asphalt package has to be laid. The asphalt package consists of a mortar base on which the asphalt layers, comprising a base, binder and surface course, are placed. For noise abatement purposes, they are mainly made of porous asphalt.
“Normally we have to reset all the paving parameters every time we reposition the paver,” explains Henry Moser, Paving Foreman at Johann Bunte Bauunternehmung GmbH & Co. KG. “The same applies to every new layer if a different mix is to be paved at a different thickness and pave speed.” In a construction project such as the widening of the A10, the settings for the VÖGELE SUPER 1900-3i and SUPER 2100-3i paver would have to be re-entered repeatedly several times a day. “And when there’s time pressure as well, it goes without saying that mistakes can arise,” Moser adds. “That’s why we were glad of the assistance AutoSet Plus provided on the job site.”
On the A 10, each mix for the various asphalt layers had to be paved with identical parameters. To ensure that they were, the two paver operators saved the settings after each layer as a paving program whenever this layer was laid for the first time. This was quick and easy to do, because most of the settings can be taken over automatically by AutoSet Plus.
After completing one of the sections, Bunte transported the 2 VÖGELE Highway Class pavers to the next one – and the operators were able to continue working with identical settings at the press of a button. “That enables us to ensure that every asphalt layer is laid and precompacted in the same way on each section,” adds Jürgen Schimang, Asphalt Coordinator at Bunte. “So AutoSet Plus gives a high degree of security: to the paving team, because there is one less potential cause of errors; to us, because we have more process reliability; and to the client, because they can be sure that every metre of every layer is paved identically.”
Automatic setting at the press of a button: when the first base course strip had been laid, the Bunte workers saved all the machine settings using AutoSet Plus. To do that, the paving team saved just six parameters manually in the “AC22T-10cm-06m” paving program, because AutoSet Plus automatically took over all the rest of the data from the machine settings. A name for the paving program can be freely selected. It is composed of "AC" for the type of mix used (Asphaltic Concrete), 22 for the maximum grain size in millimetres and "T" for base course (which is Tragschicht in German). The “10cm” addition denotes the layer thickness and “6m” the pave width. The wide array of parameters stored highlights just how much time can be saved using AutoSet Plus Paving Programs. At the start of a work shift or another construction project, the paver operator or paving foreman can select the program from the memory and activate it by pressing a button. The Bunte paving team also created suitable paving programs for the binder and surface courses – allowing them to increase their productivity further.
André Felchner, Head of Applications Technology VÖGELE