Paving and Compacting Low-Temperature Asphalt
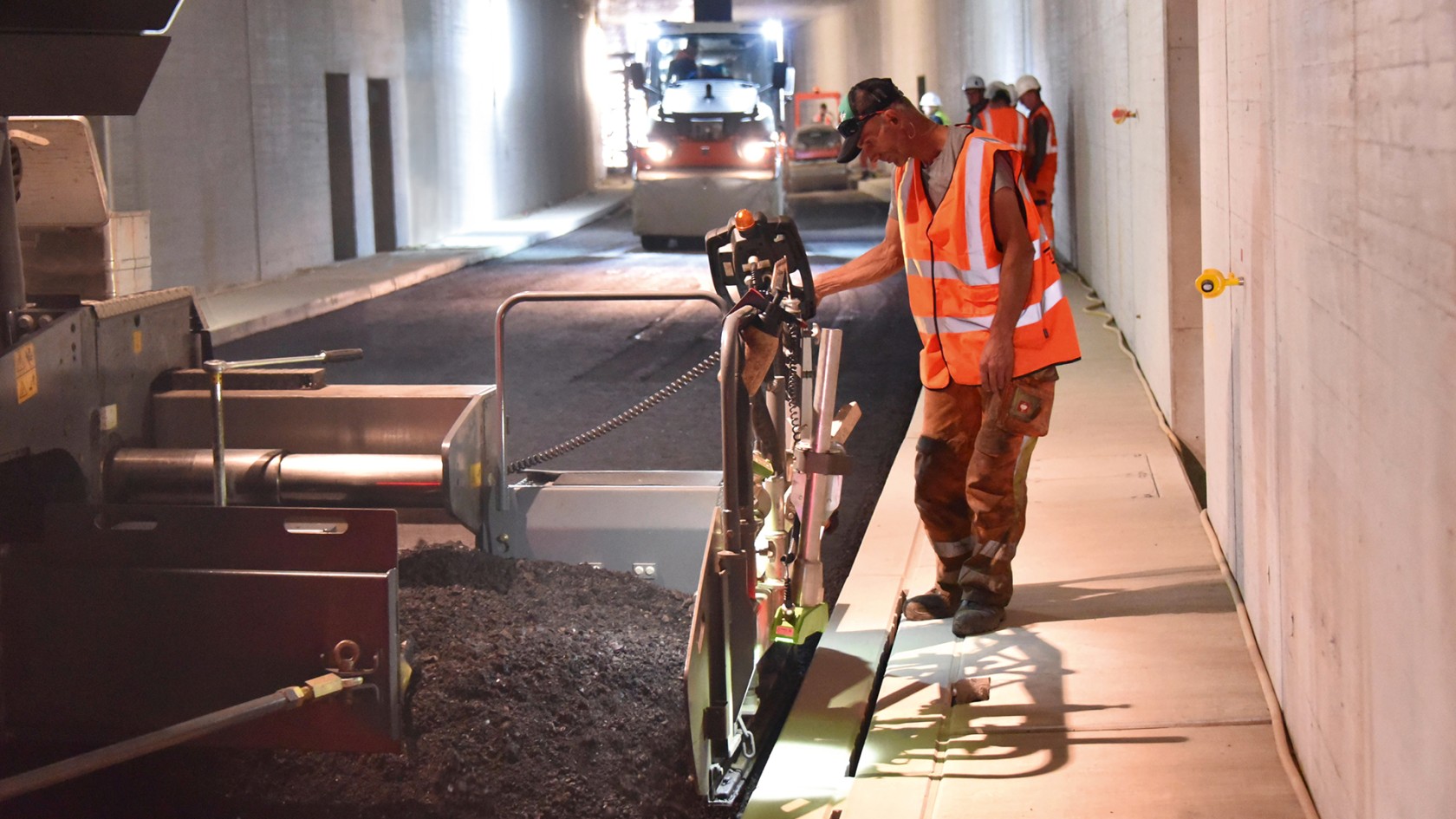
Strict conditions were applied to paving in the road tunnel under Karlsruhe’s Kriegsstrasse road: in order to reduce emissions, the contractor was to use machines with diesel particulate filters and reduced-temperature asphalts. Using VÖGELE pavers and HAMM rollers, the “Kriegsstrasse Tunnel” consortium of Schleith and Züblin was able to meet the requirements and simultaneously pave the mix efficiently and in high quality.
The process of completely reorganizing the centre of Karlsruhe around the Kriegsstrasse has been going on since 2019: what used to be a wide road for through traffic is to become a generous space for pedestrians plus a landscaped tram track and an avenue of trees with cycle paths. At the same time, an underground train line is being built and through traffic is being diverted into a road tunnel 1.6 km long. The client KASIG (Karlsruher Schieneninfrastruktur-Gesellschaft mbH) gave a high priority to protecting the paving team for the paving of the two tunnel bores (5.3 m and 6.8 m wide respectively). As a result, only rollers and pavers with diesel particulate filters were allowed to work in the tunnel. The use of low-temperature asphalts was also specified: as their paving temperature is approximately 30 °C below that of hot asphalts, they significantly reduce the pollution arising from vapours, emissions and high temperatures to which the paving team is exposed. Experts furthermore assume that reduced-temperature asphalts have a particularly high resistance to deformation. This is of particular benefit on such a heavily-used route as the Karlsruhe road tunnel.
Short window of opportunity for paving and compaction
A number of challenges is involved in processing this mix, however: on the Karlsruhe project, special waxes ensured that it was possible to compact the mix, even at low temperatures. However, this kind of asphalt hardens the instant a critical temperature is undershot, so the mix had to be paved and compacted as quickly and smoothly as possible. The contractor, Martin Paschmann Asphaltbau GmbH, used two VÖGELE pavers of the SUPER 1800-3i type and three HAMM rollers: a DV+ 90i VT-S-type Combination Roller, a DV+ 70i VV-S Tandem Roller and an HD 14i VO Compact Roller.
Efficient, powerful pavers required
In order to allow the rollers as much compaction time as possible, it was important for all the equipment on the job site to work together smoothly: in addition to steady transport of mix, continuous, efficient paving was also key. The SUPER 1800-3i machines played to their strengths here - with their powerful, gentle material handling and distribution, they achieve high laydown rates and can consequently pave even reduced-temperature asphalts in high quality. The so-called heated centre auger bearing box, already patented by VÖGELE, makes the primary contribution here; it is located where the mix drops onto the auger for distribution across the width of the machine. As on VÖGELE pavers, this surface is heated evenly, no material sticks to it - not even reduced-temperature asphalts. Electric screed heating furthermore ensures that the other components in contact with the mix, such as the screed plates and the compacting systems, are also constantly heated. This guarantees an even surface structure and incidentally reduces soiling of machine components.
A high degree of pre-compaction and automatic functions save time
In addition to clean, accurate paving, pre-compaction is another key factor. The AB 500 and AB 600 Extending Screeds were used in the Karlsruhe road tunnel, both equipped with tamper and vibrators as compacting systems. This allowed the pavers to achieve a high degree of pre-compaction and thus reduced the number of roller passes subsequently required. The ErgoPlus 3 operating concept also increased the efficiency and quality of paving: as the higher viscosity of the reduced-temperature asphalt compared to that of hot mix also had an impact on specification of roller dimension, the automatic functions of AutoSet Plus, among others, were especially helpful. Using the “Save paving programs” function enabled the paver operator to save the paving parameters once they had been used successfully and then call them back up at the touch of a button the next day or for the next section of the project.
A challenge in final compaction
In addition to the challenges faced during paving, this project also demonstrated that “compared to paving hot, it is harder for the fleet of rollers to achieve final compaction because the window available for achieving final compaction is much smaller with reduced-temperature asphalts,” reports Sebastian Boldt, foreman at Schleith GmbH. The smaller window means that the roller needed to work particularly close to the paver and in short, regular runs. “This allows the rollers to generate a great deal of compacting power in the short amount of time available. However, it is also possible to compact reduced-temperature asphalt homogeneously across the whole carriageway in dynamic form, i.e. using vibrators or oscillation,” says Dr. Axel Mühlhausen, application expert at HAMM. If the fleet of rollers is to consist of tandem rollers and combination rollers, thermal aprons are helpful to prevent the tyres cooling down quickly. The tunnel bores were paved with asphalt in two construction sections. “On the first really short section, we adapted the paving process and rolling patterns to suit the ease of compaction of the mix,” reports engineer Christian Riede. As senior construction manager at general contractor Schleith, he co-ordinated all the asphalt work. “Although it was possible to process the reduced-temperature asphaltic concrete used for a relatively long period, it would then suddenly become hard. This instant rise in stiffness makes compaction work more difficult and is a key difference from conventional hot asphalt. This once again proves that use of the correct time window is a key factor in the success of high-quality compaction.”
Ideal application for combination rollers
The client had specified medium-weight rollers for the first pass to compact the combined base and binder courses made of asphaltic concrete. A DV+ 90i VT-S-type Combination Roller from HAMM weighing approximately 9 t was accordingly used. It first used its pneumatic tyres to compact the mix, which is initially susceptible to pushing. This working motion of the tyres first generates a dense structure. The drum then ensures the necessary evenness. If the roller then approaches the paver at an angle, this effectively avoids corrugation. When compacting mixes susceptible to pushing in binder, base or surface courses, the pneumatic tyres knead and work the mix without pushing it or tearing it up. To do this, the pneumatic-tyred roller requires good traction. On HAMM rollers, traction control guarantees this in every situation. The smart design of wheel suspension with level compensation in the DV+ furthermore ensures that weight is evenly distributed on the roadbase.
Tandem rollers in the team
Final compaction was completed by a team involving an HD 14i VO Tandem Roller (4.5 t) and a centre-pivot steered DV+ 70i-VV-S Tandem Roller - the reduced time window meaning that compacting power needed to be applied quickly. When paving a free asphalt surface course, the edge areas in particular need to be compressed and compacted quickly - as soon as the asphalt has sufficient resistance to deformation. This was not necessary in the tunnel, as the course was being paved between slot gutters which was already complete.
Positive summing-up
Once the last section of tunnel had been paved, the teams from Martin Paschmann Asphaltbau GmbH and Schleith GmbH took stock. “Paving reduced-temperature asphalt is still new to a lot of people, so there is a lack of experience-based values - especially with regard to material characteristics during compaction, which was why we continuously checked density using an isotope probe. Both the measurements and the laboratory examinations carried out subsequently confirmed that we produced a high-quality, homogeneously compacted carriageway using VÖGELE pavers and HAMM rollers,” says Christian Riede.
Public Relations
Reinhard-Wirtgen-Straße 2
53578 Windhagen
Germany
Tandem roller with vibration and oscillation drum
Weight | 4,785 kg |
Drum width | 1,380 mm |
Exhaust emissions category | EU Stage V / EPA Tier 4 |
Extending screed
Compacting systems | TV, TP1, TP2, TP2 Plus |
Pave width | 2.55 m - 8.50 m |
Basic width | 2,55 m |
Extending screed
Compacting systems | TV, TP1, TP2, TP2 Plus |
Pave width | 3.00 m - 9.50 m |
Basic width | 3 m |