W 210 Fi large milling machine from WIRTGEN
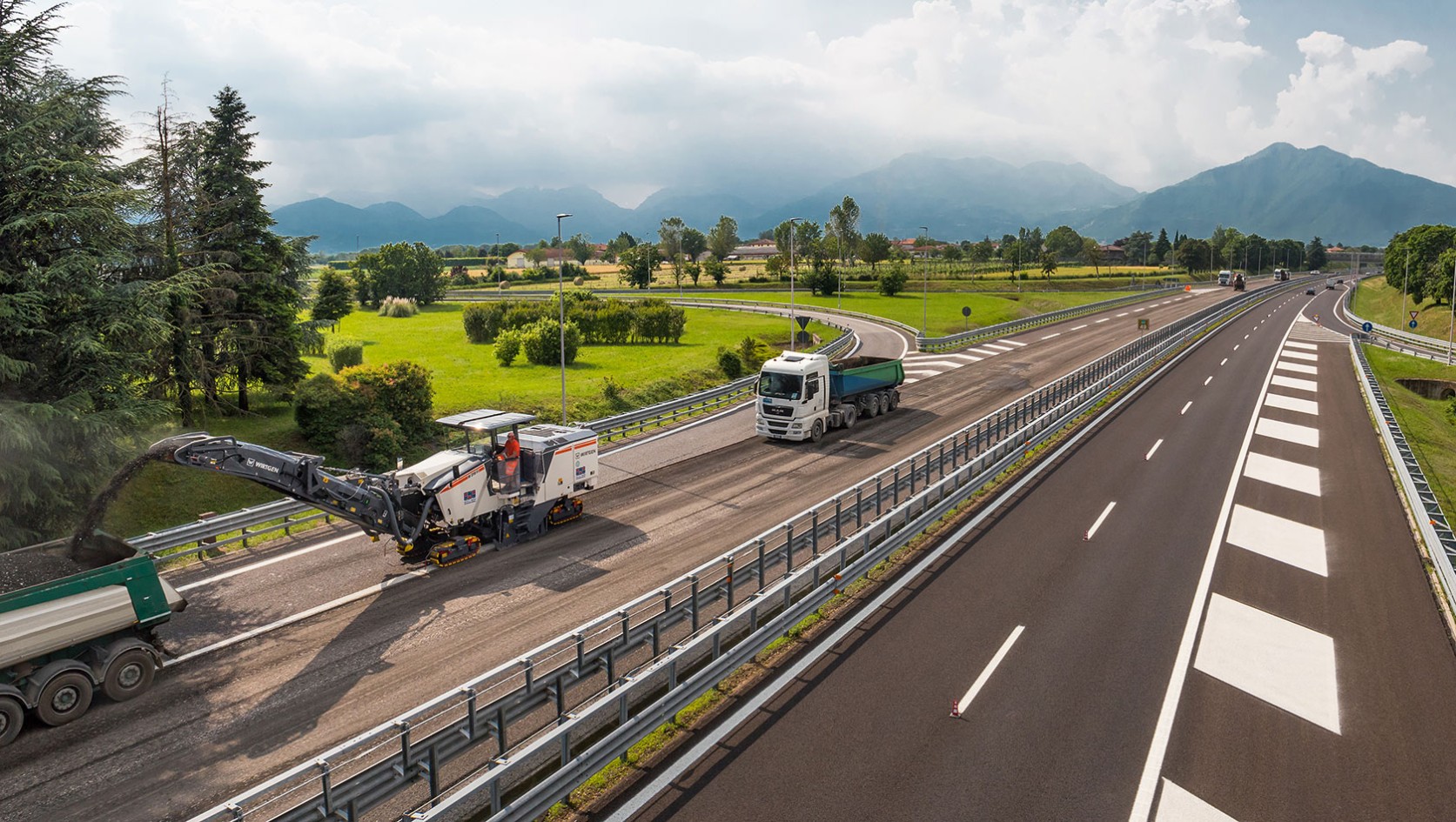
High quality at low cost and a reliable assistant to hand – for milling machine operators, WIRTGEN’s new large milling machines are the ultimate in road rehabilitation.
The professional machine with the strongest milling performance demonstrates its full potential on the A 31 motorway in northern Italy.
A total of three W 210 Fi machines demonstrated the added value of their technological innovations during rehabilitation of the A31 motorway, which connects the A4 Milan-Venice motorway with the Alps. The task on a 1.4km section in the province of Vicenza was to mill the pavement off to a depth of 22cm near the Thiene exit. The lower base course was then stabilized with cement by a WIRTGEN WR 250 recycler and soil stabilizer over an area of roughly 15,000m² and subsequently compacted by HAMM rollers. VÖGELE pavers then laid the asphalt.
To separate the milled material according to the types of mix, the large milling machines first removed the surface course to a depth of 4cm, and then milled the 18cm-thick asphalt binder course and asphalt base course in a second pass. This allowed systematic reintroduction of the separate layers into the material cycle.
The cold milling machines drove in staggered formation to continuously “feed” a rapid succession of 45 dump trucks with milled material. The new generation of machines impressed even such experienced milling machine operators as Valentino Pivotto, who works for milling service provider Crestani, “And not just because it was the first job following training on the machine.” It was the first time in many years that the operator had driven a WIRTGEN milling machine again.
The W 210 Fi represents an enormous leap forward in terms of control, performance and productivity. Not to mention the DUAL SHIFT feature, which makes this machine a real benchmark in its field.
Valentino Pivotto, Milling Machine Operator Crestani
Thanks to the new two-speed powershift transmission, which is automatically controlled by Mill Assist, a much larger range of milling drum speeds is now also available. The diesel engine also features a modern engine rating with a high torque starting at 1,300rpm. This lowers diesel consumption and noise emissions.
The intelligent control of the two-speed powershift transmission combined with the diesel engine extends the range of milling drum speeds, both upwards and downwards. This supports significant reductions in fuel consumption and cutting tool wear in the low milling drum speed range.
A high-quality milling pattern can be achieved in the upper milling drum speed range, even when working with a high area output. This makes the W 210 Fi professional machine ideal for particularly demanding milling jobs.
The WIRTGEN Performance Tracker (WPT) now makes it possible for the first time to precisely determine the milling work actually performed and “eliminate all uncertainties about the project parameters”. The machine’s performance and consumption data are also extremely valuable to Martin. “I can send all this data directly from the machine, which means we immediately receive a comparison of costs and productivity. This makes jobsite cost analysis much easier.”
At the same time, efficiency analyses are also a valuable decision-making basis for future orders. The machine operator then knows which milling machine is the most efficient solution for the respective job.
It is definitely different from other cold milling machines. Especially when it comes to fuel consumption, which has really been reduced without performance losses. Another interesting feature is the WPT system, which provides a wealth of data.
Gabriele Martin, milling machine operator at Ecovie
Wirtgen has developed a solution that, for the first time, makes it possible to accurately and reliably document actual milling work completed – the new PERFORMANCE TRACKER (WPT).
The three milling service providers had opted to primarily use three W 210 Fi machines for the rehabilitation of the A31 motorway. “This machine allows the operator to concentrate more effectively on the work, thanks to the excellent visibility and the new control and data acquisition systems,” says Massimo Valerio, pointing out the control panel of the new large milling machines.
Thanks to the newly designed operating concept, the Girardini operator not only has a clear overview of all the most important data on the milling process and the milling machine condition on a central seven-inch control panel; the operating convenience is also enhanced by control panels for levelling or for controlling the discharge conveyor. “At the end of the day, the operator’s platform really makes all the difference,” says Valerio, who is relieved of many tasks by the new Mill Assist control system.
To operate the machine at the optimum operating point, he and his colleagues previously had to set a large number of machine parameters, such as the diesel engine and milling drum speed, the milling speed or the quantity of water required to cool the cutting tools, relying only on their intuition and experience. This was a highly challenging task considering the complexity involved.
Varying conditions, such as different degrees of pavement material hardness, also required frequent manual adjustments.
This is where Mill Assist comes in. It continuously processes more than 60 signals to simulate many different setting variations and combinations in real time using complex algorithms and formulas.
In automatic mode, Mill Assist always strikes the optimum balance between milling performance and operating costs. This not only improves machine performance, but also reduces diesel, water and cutting tool consumption as well as CO2 emissions.
Massimo Valerio was also immediately struck by the “lower noise emissions and vibrations when milling 10, 15 or even 18cm, as we are doing here” – Milling 4.0 on the A31.
Simply more efficient: even optimization options are communicated to the operators, for example whenever milling in two passes would be more economical than in one.
In addition to automatic operation, the milling machine operator also has the option of selecting one of three work strategies depending on the requirements: