WIRTGEN SP 15i offset slipform paver
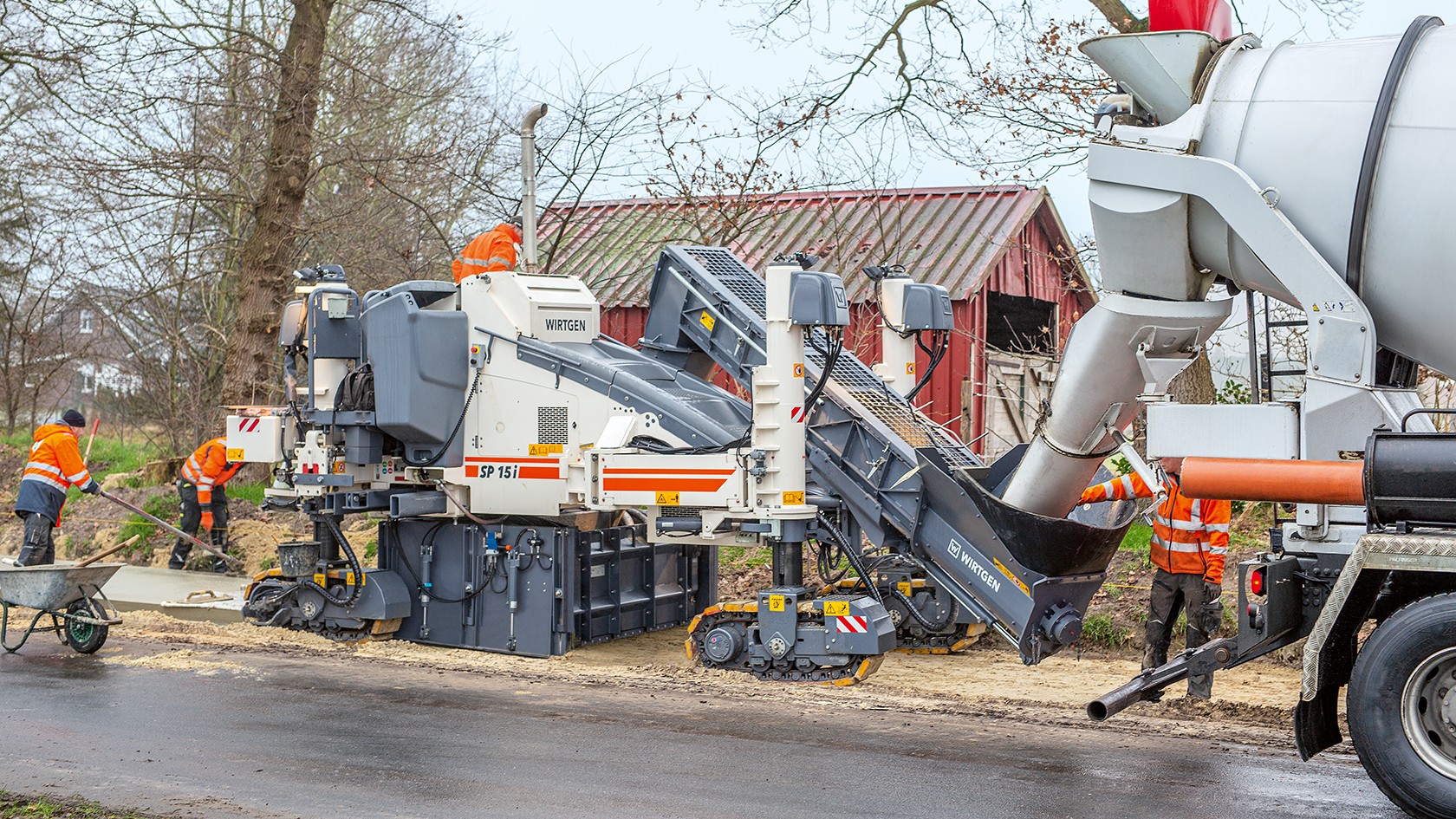
Because the SP 15i is an all-rounder when it comes to paving monolithic profiles up to 1.3 m high, it is one of the most popular slipform pavers in its class worldwide. In addition to the construction of kerb and gutter profiles, concrete safety barriers, drainage structures or channels, the smallest machine in WIRTGEN’s range of slipform pavers is also suitable for the production of narrow paths. In this case, the SP 15i can – under certain conditions and depending on the configuration – now also pave areas up to 2.2 metres wide instead of the previous maximum of 1.8 metres thanks to a new offset mould.
During a project in Esterwegen, near Papenburg, Germany, the small paver offered a first taste of the extended range of applications it can now cover by paving a 750-metre-long and 2-metre-wide cycle path along a rural road. Since the adjacent trees left little space to work, outstanding manoeuvrability was required in addition to compact machine dimensions. This is one area in which the SP 15i stands out thanks to its intelligent steering and control system, among other features. Especially in bends, the tried-and-tested Ackermann steering ensures the machine can be handled with precision. The computer-assisted steering system varied the speed of the individual track units so that the SP 15i followed the specified references with pinpoint accuracy. In addition, the system adjusts the steering angle of each track unit fully automatically, depending on the paving radius and the machine geometry. This means that the machine can, in principle, be used to pave curved profiles with minimum radii of only 500 mm. In addition, the slipform paver can be easily manoeuvred with the help of additional steering modes – Crab and Coordinated. The SP 15i used in Papenburg was equipped with two steering and height sensors each that scanned the previously tensioned stringline on the left-hand working side, thus ensuring the process of levelling the 12-centimetre-high cycle path was extremely precise.
During construction, traffic on the quiet rural road kept flowing on one lane. At the same time, the construction site was easily accessible at all times for the truck mixers to discharge the concrete into the receiving hopper of the paver’s 4.6-metre-long auger conveyor. The 2-metre-wide mould was fed via the auger. As the auger conveyor is capable of holding large quantities of concrete, paving was able to continue even between loads from the truck mixers.
Thanks to the ability to continuously pour concrete and the machine’s steady high advance rate of 1.3 m/min on average, we were able to complete the project in just three days.
Franck Alberts, foreman at Böhling Bauunternehmen GmbH