Surface Miner
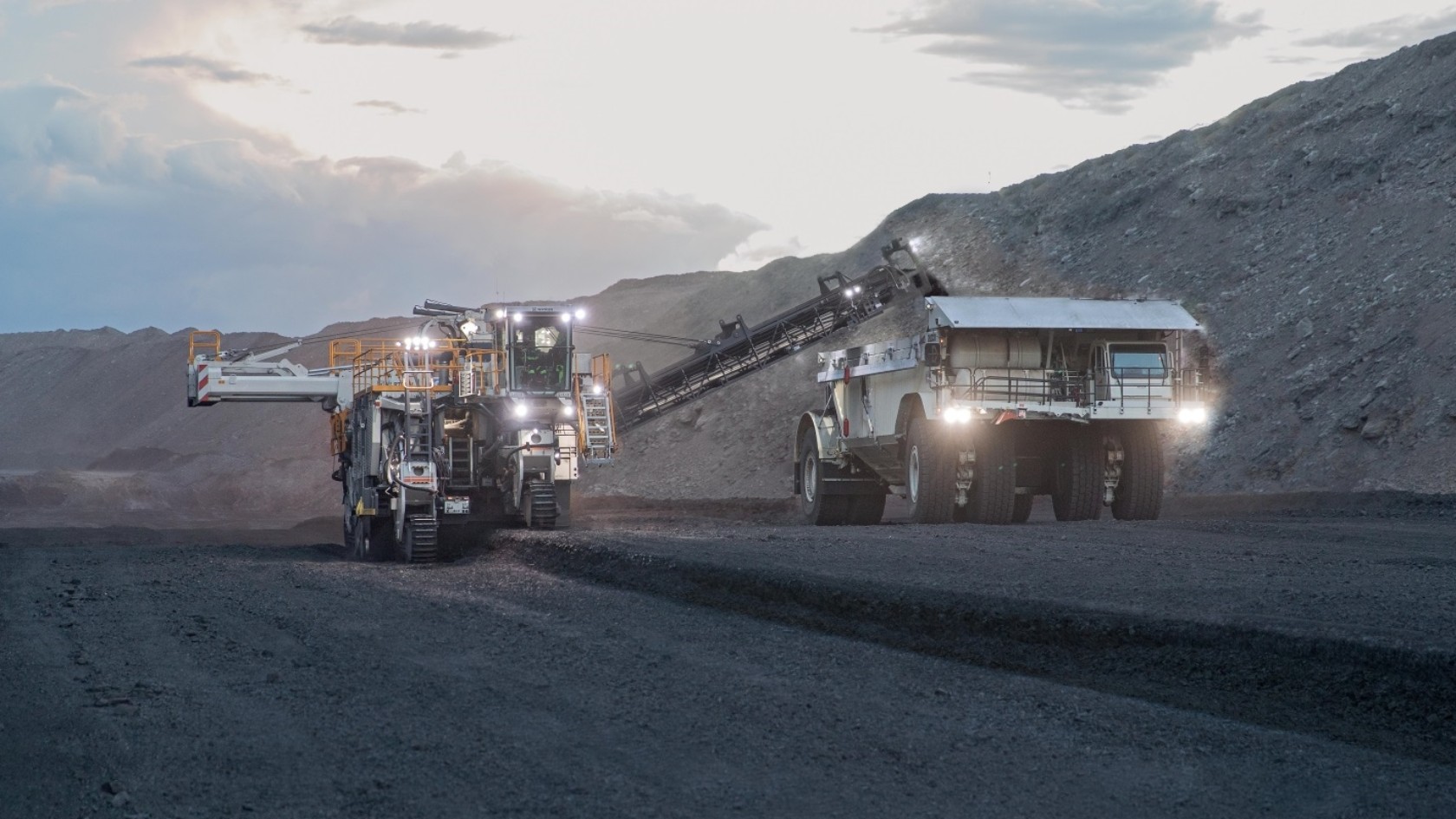
Computer-assisted automatic functions not only optimise work processes and thus machine productivity, but also the machine operator’s performance. Our numerous intelligent information and diagnostic systems additionally support the operator and make their job easier – resulting in faster and more efficient operations. A few examples of assistance systems for surface miners are presented below.
WIRTGEN surface miners can be operated effectively by a single machine operator. The cutting operation and cutting depth control are performed in a largely automated process. The operator can fully focus on steering the track units, controlling the miner’s advance speed and discharging the mining material.
Mining Assist combines both payload and quality control in a single system. In addition, the intelligent assistance system is supplemented by an additional sensor on each side of the machine immediately behind the scraper. These determine the condition of the sub-base to be removed in advance. As a result, the machine operator can adjust the working depth on the relevant side of the machine well in advance in order to obtain only high-quality material.
The WIRTGEN Payload Control system shows the machine operator the quantity loaded onto the current truck in real time. For this purpose, a sensor system on the discharge conveyor measures the mass throughput of the milled material and transmits the information to the operator’s control panel.
With WIRTGEN Quality Control, a sensor system on the discharge conveyor of the surface miner also measures the ash content of the mined coal in order to classify the material in question and determine its quality. The BTU value determined is then analysed by the system and displayed to the machine operator on the control panel. After each truck has been loaded, the average that has been calculated indicates the stockpile which the payload should be transported to. This makes it possible to sort the coal according to quality.