Automatic level and cross slope control
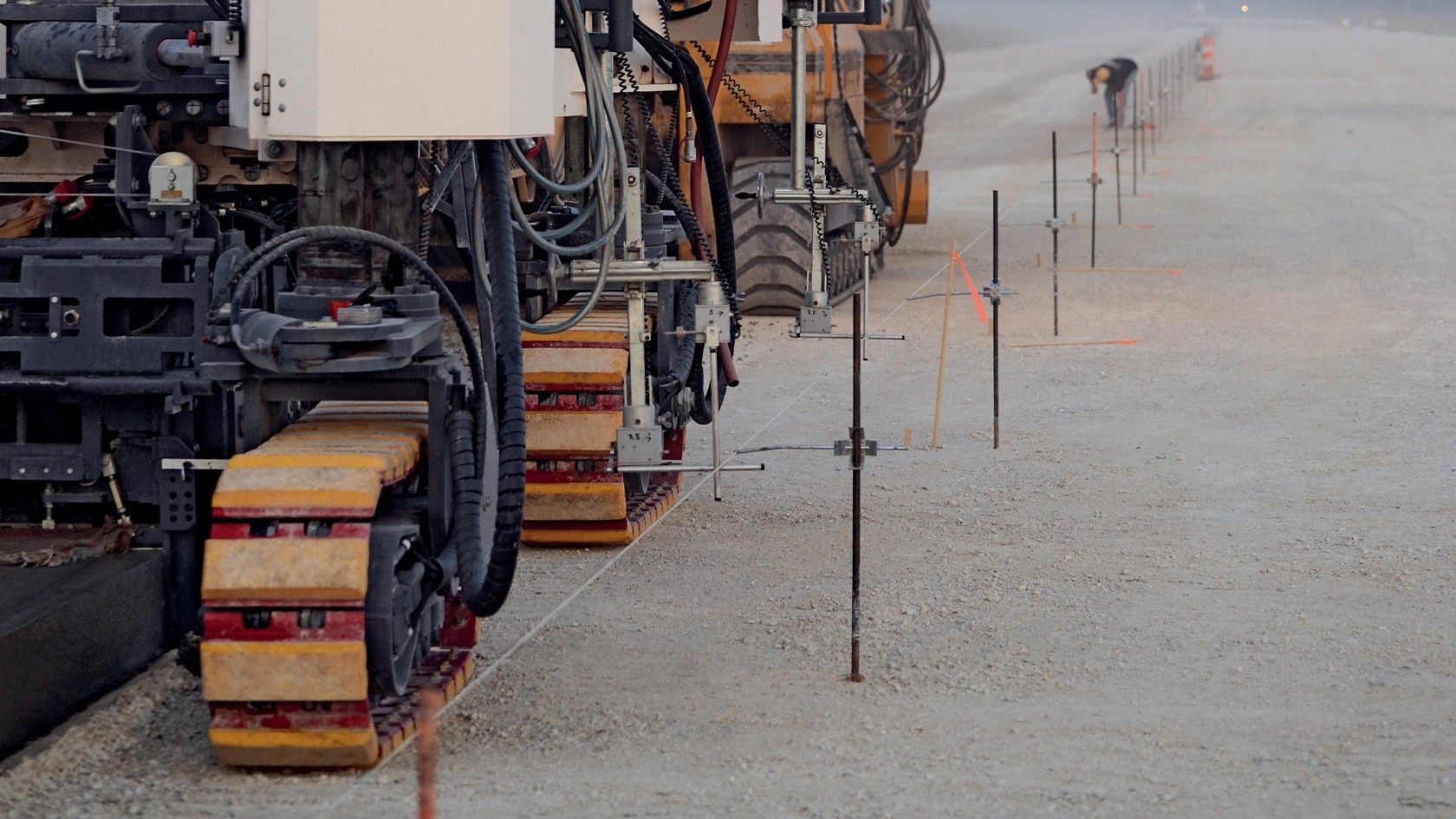
The levelling control system governs the paving thickness of concrete profiles in accordance with a specified reference. Slipform pavers typically use mechanical systems scanning a stringline to effect horizontalposition and level control.
Stringless 3D control systems have also proven their worth in recent years, however, and are sometimes even a requirement today in tender specifications. 3D control offers many advantages over stringline control – the ideal paving line, for instance, need not be transferred to the actual construction site by means of a wire but is available as a computer model. This digital terrain model is used to define the set positions of the machine which are then monitored using optical measuring systems such as a motorized total station and prism. A wide variety of concrete profiles can thus be produced to precision in a simple and efficient process.
A stringline is carefully installed and tensioned along the entire length of the concrete profile or slab to be produced prior to commencing the paving operation. It will provide the specified paving level. Two separate sensors carried by the slipform paver normally guide off the stringline for level control – one sensor for the front tracks, a second one for the rear tracks. While the slipform paver keeps moving forward, both sensors scan the stringline and continuously send pertinent level details to the paver’s control system. These level details are not absolute values, however, but merely the deviations from the set value that is provided by the stringline.
The control system receives the measured results, and in case of any deviation actuates the relevant hydraulic cylinders to compensate by adjusting the level of the machine including the mould. This matching process takes place around 40 times per second. The side of the paver carrying the mould is immediately raised or lowered by the resulting difference between the actual and set values. The opposite side of the machine is balanced in level by means of a second control loop with integrated slope sensor.
With stringless systems, the computer of the 3D control system feeds the paver’s control system with the specified parameters of level and horizontal position of the concrete profile to be built. The 3D system uses a special interface to communicate with the controller of the slipform paver.
Two prisms are typically installed on the slipform paver which have direct visual contact to a total station each, reflecting their optical beam. The total station keeps determining the prism’s current 3D position. The measured results are transmitted by radio to the system computer on the paver. Two multi-axial slope sensors integrated in the machine additionally determine the paver’s longitudinal and cross slope.
The system computer uses these parameters to calculate the machine’s actual position and direction of travel. The position data are continuously compared with the design data of the concrete profile stored in the system computer as a digital model. Any deviations are immediately forwarded by the system computer to the paver’s machine control system. The paver’s control system then initiates the required corrections in level, slope and steering angle of the track units. This procedure enables the production of concrete profiles that meet the specified requirements with great accuracy.
Perfect paving results are guaranteed thanks to the electronic slope control developed by WIRTGEN on the basis of the “Rapid Slope” cross slope sensor. Optimized control technology enables the innovative slope control system to achieve as yet unmatched dynamics and precision. Significantly shorter machine response times are refl ected in the precision and quality of the completed concrete product. The WIRTGEN cross slope system can be relied on to quickly level out any vibrations or ground irregularities.