Control and overload systems
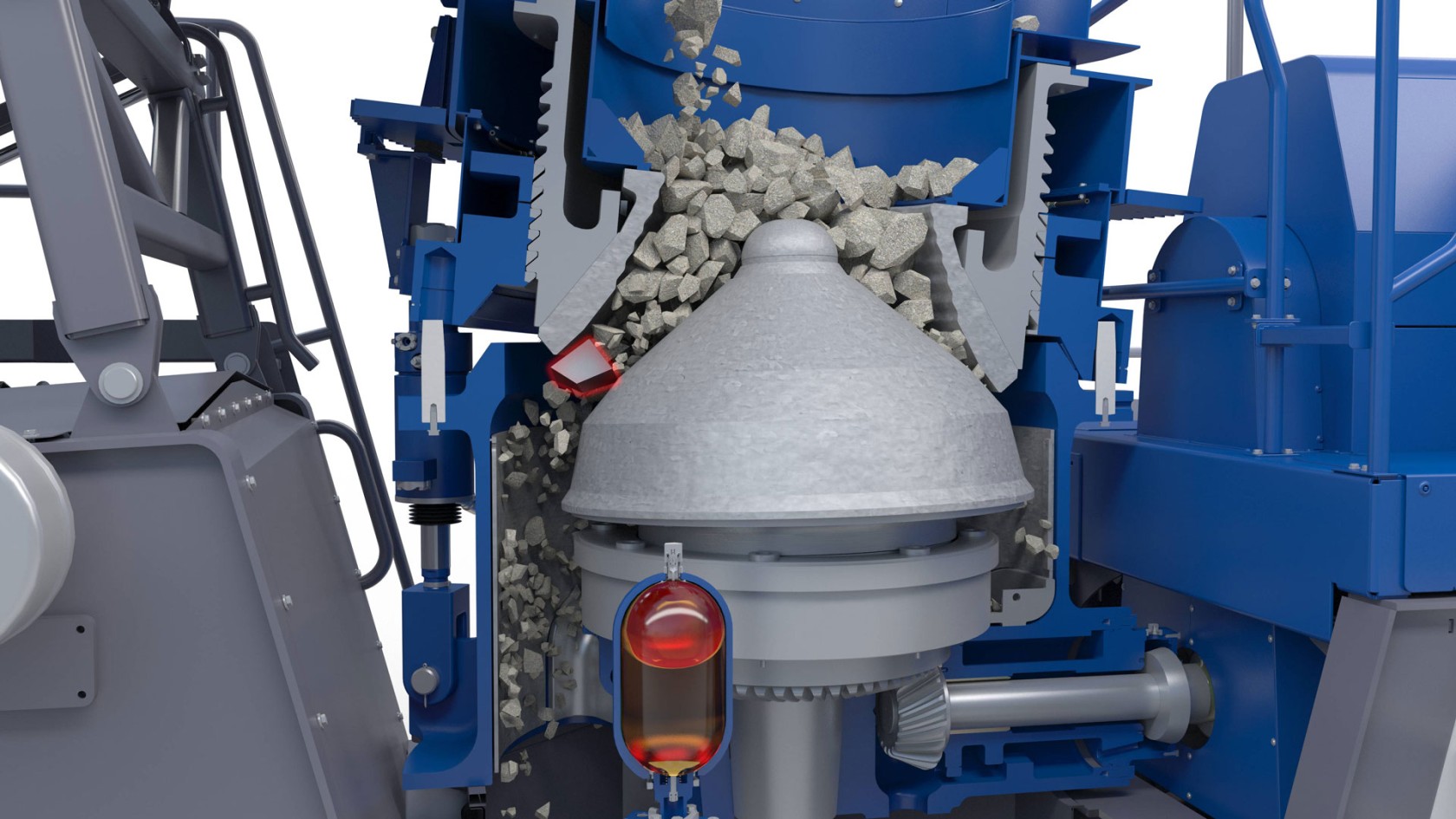
Control and overload systems for crushing plants control the process for you
Continuous crusher utilisation is indispensable for a first-class final product and a correspondingly high production output of crushing plants. Control and overload systems help to keep the fill level constant and avoid production downtimes in overload situations.
Depending on the feed material, overload and underload situations frequently occur in the crushing process. Overload often results in standstills with occasional resultant crusher damage. To prevent this, the plant is often not utilised to the full extent. This results in decreasing production output and product quality.
Particularly in untypical applications, the good prescreening it achieves is indispensable. The additional time and effort required for a prescreen with magnet and the personnel who sort out wood and other uncrushable objects are reflected in the production costs accordingly.
Modern crushing plants support the user here with automated control and overload system and thus guarantee plant performance and machine availability.
On KLEEMANN crushers, the Continuous Feed System (CFS) regulates different plant parameters such as crusher feed and thus always guarantees an optimum feeding system.
That means: When crusher utilisation reaches a critical level, the conveying speed of the feeding unit is reduced. Conversely, when the speed is increased again the crusher feed returns to the normal level. Of decisive importance is that the CFS works steplessly and adjusts to the ideal process automatically.
The combination of overload and other control systems that differ according to the plant type guarantees high process reliability and thus high availability of the plant. Overall result: increased production output.
CFS control system keeps on learning continuously
The CFS is an intelligent system that is continuously self-taught. It reacts to an uneven material flow caused, for example, by delayed feeding or mixed feed material. The system adapts the feed speed automatically and thus ensures constant utilisation.
Even in case of uneven feed material, for example, with varying content of fines or feed grain that is too coarse, the necessary adaptation measures are detected by the system and, for example, the conveying speed of the feeding unit is adapted. This is important because, for example, fines have a strong influence on the crushing process and thus the crusher load.
Principle of the Continuous Feed System using the example of a MOBICAT jaw crushing plant: The automatic control system adjust the material feed depending on the crusher level and allows users to place the focus on material loading.
Load reduction guarantees plant availability
If crushers are operated beyond their permissible load range, this can result in serious damage. The Load Reduction System LRS, which works closely together with the CFS, has the task of preventing this. The "load monitor" in the software detects the overload and intervenes to control it: the loaded volume is reduced, the filling level of the crushing chamber is adjusted and the forces acting on the housing and rocker are thus reduced. If, on the other hand, an underload is detected, the crusher level is increased again in steps to guarantee an optimum plant performance.
In difficult applications with a high share of foreign material such as metal (e.g. in recycling), frequent overloading of the crusher is possible. For the MOBICAT MC 110(i) EVO2, the effect multi-stage overload system is a special highlight. It effectively prevents blockages and material bridging that can lead to unwanted downtimes. If uncrushable material enters the crushing process, the CSS opens 2x faster over the entire adjustment range than with the predecessor plant or, as an option, even up to 20x faster. After this procedure, the crushing gap is repositioned automatically to the previously set crushing gap. This increases the availability and thus the overall output.
Intelligent impact toggle yields
The mobile impact crushers MOBIREX MR EVO2 are used as all-rounders in soft to medium-hard natural stone and in recycling. The reasons that can lead to an overload are correspondingly diverse. Uncrushable foreign bodies such as excavator teeth made of tempered steel are particularly feared on work sites.
Thanks to the effective overload system, in case of uncrushable elements the lower impact toggle opens and then moves back automatically to the preset value. As a final safety element, a bursting disc is installed to protect the crusher.
Expert knowledge
Opening of the crushing gap on jaw and impact crushing plants prevents initialisation of the protection level. As a final mechanical safety element on the KLEEMANN MOBICAT and MOBIREX series, a pressure plate with a predetermined breaking point is installed which, when broken (similar to a safety fuse in the electric circuit), leads to machine standstill.
Tramp Release for optimum self-protection
Used in the second or third crushing stage, MOBICONE cone crushers are designed for precise recrushing of stone. To guarantee optimum performance, output, product quality and wear must be balanced up.
If uncrushable material such as metal enters the crusher and a short-term overload situation occurs, the overload system Tramp Release reacts. It lifts the bowl of the crushing unit, which increases the size of the gap and the foreign body can pass the crushing chamber without causing damage.
Ringbounce Detection regulates in case of a high content of fines
A further overload scenario with cone crusher is so-called Ringbounce. In this case, an excessive share of fine material or materials bound by moisture clog the crusher. When operating cone crushing plants, this is the "natural enemy" of a continuous crushing process. Forces are created that mean that the bowl can no longer be held firmly on the main frame and starts to vibrate. This needs to be prevented.
On the KLEEMANN cone crushers, the overload detection system Ringbounce Detection takes over this task. Here, the hydraulic pressure and other parameters of the crusher are monitored continuously. If necessary, the system reacts and thus prevents latent overloads that could cause serious damage. Depending on the application, you can use the control system to define whether the Ringbounce Detection is to be tuned more to output ("Mixture Mode") or to product quality ("Precise Mode").
Low content of fines = no overload reaction
High content of fines = overload reaction probable
Expert knowledge
In the cone crusher, crushed material slides down from the top, while new material slides in from above. When the gap closes, the slipped material is crushed and reduced in size. However, this also reduces the available volume in the crushing chamber. If the material does not have enough cavities, for example because fines fill the spaces between larger stones, an overload situation can occur as the cone tool runs on block when the gap closes.