MOBISCREEN MSS 502(i) EVO
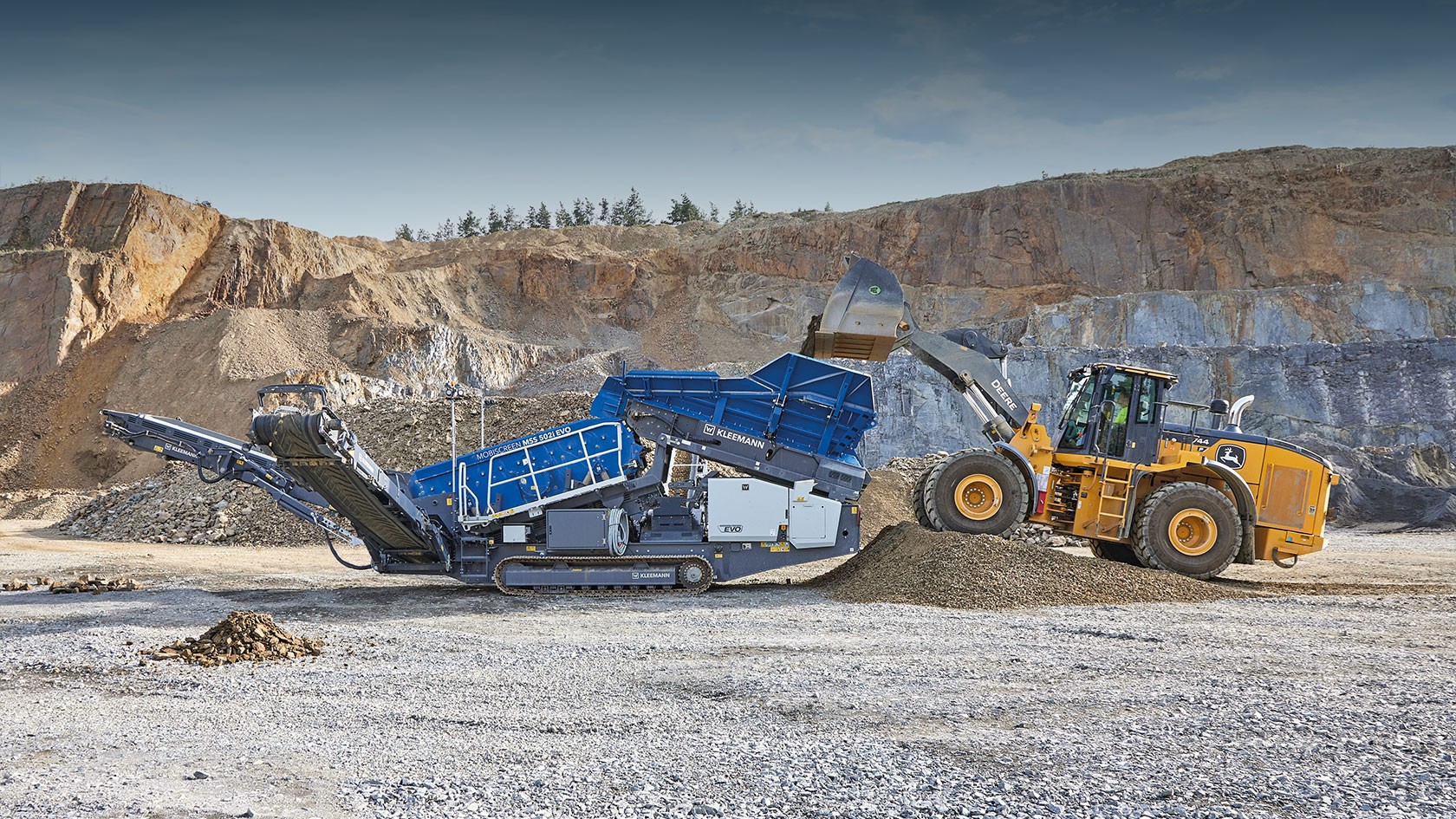
Compact plant extends the product portfolio of screening plants:
with the new MOBISCREEN MSS 502(i) EVO Kleemann extends the portfolio of scalpers among the established MOBISCREEN MSS 802(i) EVO. The focus is also on flexibility, operability and ergonomics.
With its compactness the MOBISCREEN MSS 502(i) EVO is optimised for lower feed capacities up to 350 t/h. A generously dimensioned feed hopper, screening surface of 5.4 m² and a wide crusher discharge conveyor guarantee excellent material guidance.
For high flexibility in the application, the speed of all conveyor belts is steplessly adjustable and a simple conversion from two to three final grain sizes is possible. The wide setting range of the screen casing angle (15.4–20°) makes a high screening capacity combined with very high product quality possible. The large selection of screening media also contributes to this.
Whether these are finger decks for clayey excavated earth or square mesh for classifying decorative grit – from a large selection of screen media, the screen decks of the MOBISCREEN MSS 502(i) EVO can be covered to match the individual application case. Mixed covering of the screen decks is also possible. Overall, the new plant offers comprehensive configuration diversity to impress as a standalone machine or in conjunction with further Kleemann plants.
The new MSS 502(i) EVO was tested in hard rock, recycling, excavation and iron ore – loaded by an excavator or wheel loader.
Before Kleemann crushing and screening plants are launched on the market, they are subjected to rigorous tests in different applications under real conditions by our customers. There are clear guidelines on the number of hours and range of applications. Diverse measurement and operating data is logged during the operation of the prototypes, meaning conclusions can be quickly drawn about any need for optimisation.
"We test all our plants under real conditions and deliberately push them to their technical limits and sometimes beyond. Only then are we able to get a full picture of their performance. During the entire development phase and especially in the tests of our prototypes, there is an intensive exchange of information and ideas at Kleemann between development, design, technology and product management. The new scalper has already made a very good impression after its first few hours of testing – and up to now has proved to be ready for market launch", reports Aiko Fischer, Product Manager for mobile screening plants at Kleemann.
"The new scalper has already made a very good impression after its first few hours of testing – and up to now has proved to be ready for market launch."
Aiko Fischer, Product Manager for mobile screening plants at Kleemann
Intuitive plant control reduces the risk of operating errors and saves training time. In addition, all relevant functions of the MSS 502(i) EVO can be operated and viewed from a safe distance. Apart from the increased work safety, the set-up and dismantling of the plant is also accelerated with the mobile operating device, because, for example, there is no longer any unnecessary travel between the control and desired pinning position of a discharge conveyor. The operator ultimately holds the "control" in his hands.
Fact: The quicker the plant is ready for operation, the quicker it can earn money for the customer.
"Automatic mode is standard in our EVO screening plants. It ensures that all subsections and belts of the screening plant are automatically started in the correct sequence when the diesel engine is switched on at the touch of a button, and switched off again in reverse order once the work is completed. Accidental misuse is ruled out. After the actuation of automatic mode the operator can already make their way to the wheel loader or excavator to start work quickly – the plant is ready for operation as soon as the operator takes his seat", explains Aiko Fischer.
Sustainability plays a decisive role at Kleemann even in the development and design phase. In the MOBISCREEN MSS 502(i) EVO this is demonstrated with the option of an electro-hydraulic Dual Power drive for on-site CO₂ emission-free work. If a mains connection is available, the machine can be operated in all-electric mode. If there is no power supply available, the MSS 502i EVO can still be used flexibly with its diesel drive. The load-controlled fan guarantees a reduction of the noise level and diesel consumption. Water spraying at the discharge conveyors reduces the dust emissions, and therefore ensures better working conditions for machine operators and higher levels of acceptance of local residents.