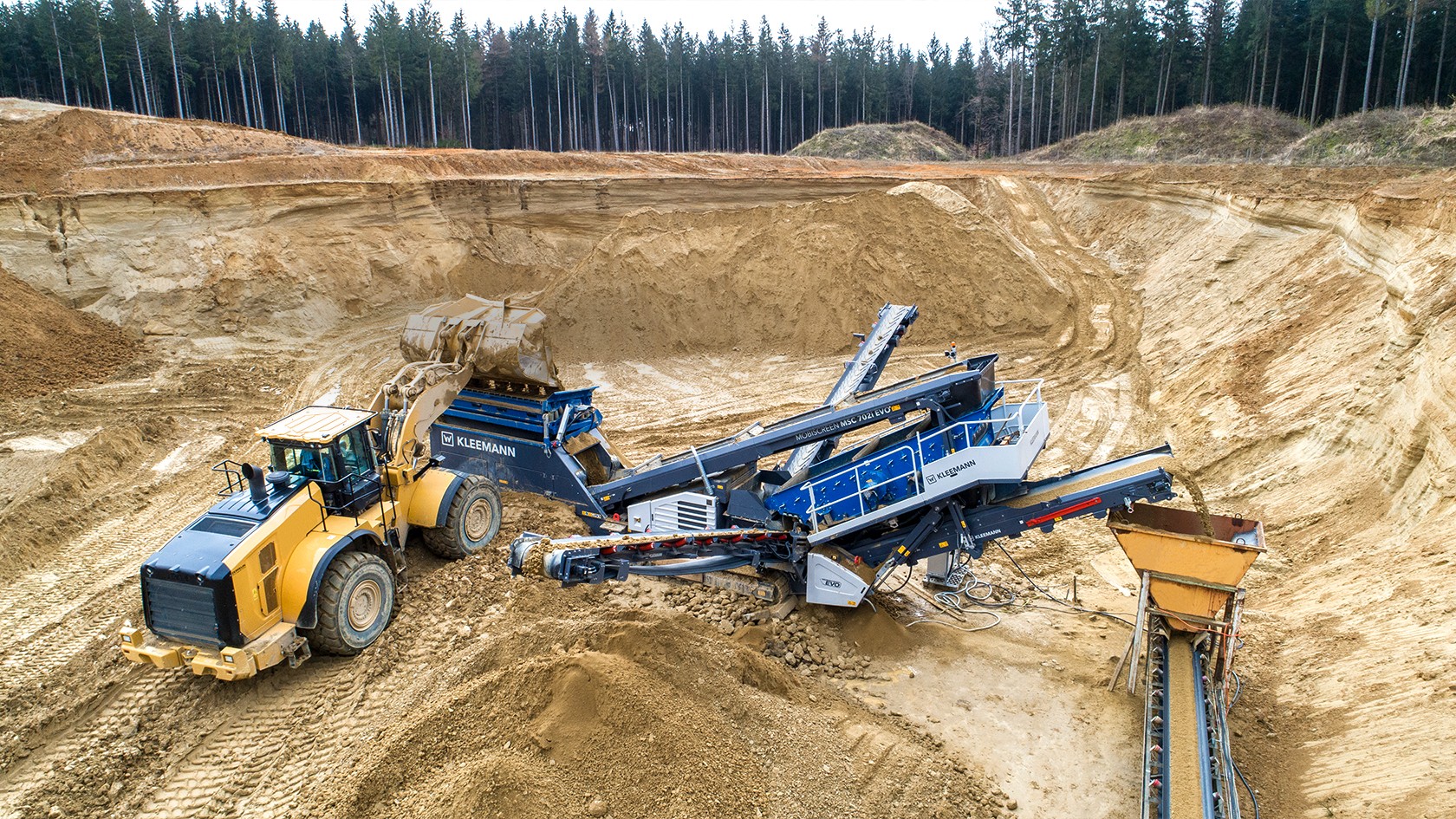
Screening of high-grade quartz sand with the mobile screening plant MOBISCREEN MSC 702i EVO with Dual Power
With the mobile classifying screen MOBISCREEN MSC 702i EVO with Dual Power, Emil Steidle GmbH & Co. KG from Sigmaringen is breaking new ground. It is the first all-electric plant in the fleet and the first plant from Kleemann.
Emil Steidle GmbH & Co. KG is a 200-year old family enterprise that operates in five different business lines. The current business areas include building construction and civil engineering, production of concrete prefabricated garages and modules, glued laminated timber production and industrial carpentry, production of wood pellets and also, for over 50 years, the extraction and processing of quartz sand. The quartz sand is extracted by Steidle in their quartz sand pit in Meßkirch-Rengetsweiler. The extracted material is partly sold directly ex works after preliminary processing and is used, among other things, for sports ground construction. The greater share is further processed in another plant and then used, for example, in glass production or for building materials such as plaster or adhesives.
Customer's request: an efficient solution for separating grain sizes. "We held talks with different suppliers and manufacturers of screening plants where numerous options were considered", explains Michell Blasczyk, Sales in Kleemann Southern Germany. "With the MOBISCREEN MSC 702i EVO with Dual Power, we have a screening plant that meets numerous requirements", says the Kleemann expert. On the one hand, they have a very wide, large screening surface that can deliver a very high output. On the other hand, Kleemann provides an option for all-electric operation of the plant – a future-oriented drive system that works on site without CO₂ emissions: a positive feature for the environmental balance and quality assurance. Steidle thus makes a contribution to climate protection and can count on acquisition subsidies from theFederal Office of Economics and Export Control (BAFA). To guarantee the power supply on site, the company built a transformer station that accompanies the machine, which is moved 2–3 times a year.
Good to know:
The Dual Power option
The Dual Power option makes it possible to use an external power supply. The plant can thus be operated locally free of emissions. For this purpose, the company invested in the infrastructure and created a transformer station that guarantees the supply continuously.
Kleemann was able to impress on several levels with the delivery of the MOBISCREEN MSC 702i EVO with Dual Power. On the one hand, the plant provides a very high output with maximum energy efficiency and, on the other hand, the professional support by the Kleemann employees was a decisive factor.
This new acquisition is not only the first plant at Steidle with an electric drive, it is also the first collaboration project with Kleemann. Several factors impressed the Swabian company: "It was simply very professional how the Kleemann team made a great effort to find the correct settings and optimised the inclination angle or the covering of the screens." The delivery was also fast. You can just sense the presence of committed, experienced employees who know what they are doing", says Achim Haßdenteufel, Section Manager at Steidle. Haßdenteufel added that the plant performance convinced his team during the first trial run. "The machine has an impressive output. Everything can be operated very conveniently by remote control. Although our employees, who have been used to control via hydraulic levers up to now, had to reorientate, they quickly managed to cope with the digital display. It has a clearly arranged and intuitive design," reports Walter Kieper, Facility Manager at Steidle. The customer was also impressed by the fact that production of the John Deere drive and plant takes place in the same company, which guarantees smooth interaction.
"It was simply very professional how the Kleemann team made a great effort to find the correct settings and optimised the inclination angle or the covering of the screens."
Achim Haßdenteufel, Section Manager at Steidle
The demands made on the material and thus the machine at Steidle are high. These requirements are met by the many technically well developed and thought-out details of the MSC 702i EVO. The configuration of the belts, for example, can be mirrored. The fine grain conveyor and middle grain conveyor can be installed either on the right or left. The travel path of the wheel loader can be kept to a minimum, which optimises the power consumption and wear of the vehicles.
The MOBISCREEN MSC 702i EVO is equipped with a vibrating slotted grate. Large sand stones can thus be separated in advance and the machine can be loaded with a 0–100 mm feed size. The upper deck is used as a relief deck; the second deck therefore defines the target grain size.
The stepless setting option of the belt speed contributes to energy efficiency: As the screening process at Steidle merges the discharge of the middle grain conveyor and fine grain conveyor, only one side discharge conveyor is actively operated. The speed of the second belt is throttled to save energy. This throttling option is also an advantage when the feed material is very wet. "Sand is not always the same. Depending on moisture content and properties, the covering, inclination angle, speed and many other factors must match exactly", says Michell Blasczyk.
"The machine has an impressive output. Everything can be operated very conveniently by remote control."
Walter Kieper, Facility Manager at Steidle
It was not only the very well prepared demonstration and the highlights of the machine that impressed the people in charge at Steidle, but also what went on behind the scenes. "On the one hand, we have experience at Kleemann and, on the other hand, specialist departments who prepare precise flow charts or a laboratory that examines the material exactly in advance. This is really helpful and is reflected in the result."
Highlights of the MOBISCREEN MSC 702(i) EVO with Dual Power
Press/media kit
Click here to download a ZIP file containing the press release in the available languages in Microsoft Word format and the images in 300 dpi resolution.
Download