PRO line
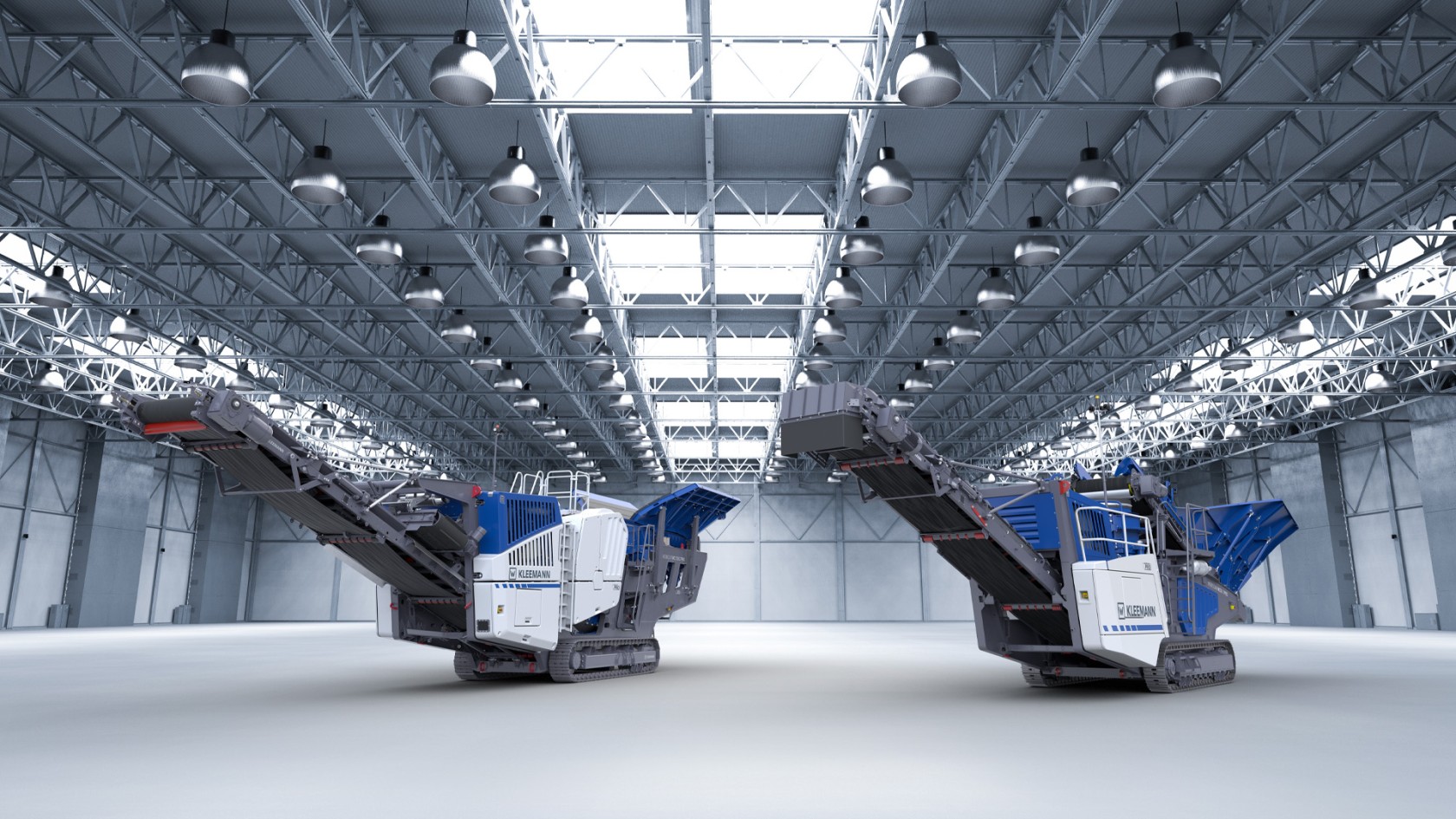
Crushing large piece of rocks, production of precise grain sizes and shapes, efficient use of energy: the KLEEMANN PRO Line.
The technology and design of the MOBICAT MC 120(i) PRO jaw crusher, the MOBICONE MCO 110(i) PRO cone crusher and the MOBIREX MR 130(i) PRO impact crusher have a uncompromisingly robust design and are therefore perfectly suitable for continuous use in a quarry. The plants are characterised by low-maintenance operation and high availability. The possibility of operating all three machines in a group via line coupling and thus to automate the crushing process, makes the plants the ideal team players.
Designed for high output in quarry operations: Die MOBICAT MC 120(i) PRO impresses with an output of up to 650 t/h in natural stone applications.
The high performance of the jaw crushing plant is also attributable to the dimensions of the crusher inlet of 1,200 x 800 mm and the extra-long design of the articulated crusher jaw. Even large stones can thus be drawn in.
In spite of its impressive size, the machine can still be transported in one piece. Components such as the foldable side discharge conveyor, the feeding unit and the rock chisel are equipped with hydraulic functions and can remain on the machine for transport.
The cone crusher MOBICONE MCO 110(i) PRO is the perfect partner for linked operation with the jaw crusher MOBICAT MC 120(i) PRO. The machine was developed specially for the second crushing stage to meet the high requirements in natural stone processing in a quarry and thus, similarly, comply with the high quality and quantity requirements.
The machine can be transported as a single unit (apart from return conveyor) on a low-loader. The simple slide mechanism of the feeding unit moves the machine into a compact transport position – making a fast set-up possible. The slide mechanism has a further positive feature: it permits easy adaptation of the material discharge pattern into the crusher. As a result, optimal loading is possible.
The MOBIREX MR 130(i) PRO covers a very wide range of applications in natural stone and recycling. Thanks to its all-electric drive concept with the option of external power supply, the system scores highly. The CO2-free operation ensures low energy consumption per ton of end product.
Very good product quality is expected from an impact crusher - and is delivered by the MR 130(i) PRO, including a very high production output. This is ensured not only by the proven, robust crushing unit with its two impact rockers and versatile blow bar options, but also by the 8.4 m2 optional double-deck secondary screen. This makes it possible to produce two classified final grain sizes with just one plant, without the need for an additional screening plant.
They are optimally equipped for the tough demands in the daily routine in the quarry. They can also be fitted with another electrical connection to supply power to downstream machines such as a stockpile conveyor or a screening plant (only MC 120(i) PRO).
The option for an external power supply is another more economic and environmentally friendly solution. In this manner, plants can be driven purely electrically independently of the diesel fuel – which reduces energy costs and exhaust emissions.
To guarantee trouble-free and simple operation and fast service, all machine components are particularly easily accessible.
The useful additional options for the plants increase user comfort even more – spray systems are included at different transfer points and LED lighting of the plant is available even in the basis plant. Optionally available premium lighting provides even better illumination of all important operating positions. Refuelling of the machine can be carried out conveniently from the ground – with the MC 120(i) PRO, with the help of a refuelling pump.
The plants in the PRO Line are also ideally equipped with regard to safety. All cylinders related to functions and safety are equipped with safety valves (lowering/brake holding valves). Each cylinder stays in its current position in event of deactivation or failure to protect the operator and the machine.
With regard to their output, dimensions and material flow concept, the machines in the PRO Line perfectly tuned to one another.
The line coupling option allows PRO plants to be coupled with one another. The crushing process between the crushing plants is then optimised automatically so that material is always conveyed with maximum efficiency through the machines.
Mobile jaw crusher
Drive concept | E-DRIVE (Diesel-electric) |
Max. feed size | 1,080 mm x 680 mm x 410 mm |
Feed capacity up to approx. | 650 t/h |
Mobile cone crusher
Drive concept | E-DRIVE (Diesel-electric) |
Max. feed size | 240 mm |
Feed capacity up to approx. | 470 t/h |
Mobile impact crusher
Drive concept | E-DRIVE (Diesel-electric) |
Max. feed size | 1,040 mm x 650 mm x 390 mm |
Feed capacity up to approx. | 600 t/h |