Kleemann uses GARANT Tool24 cabinets and software. The drawers and vertical cabinets make simple and effective removal and storage of tools and keys possible. At any one time it is possible to determine who removed which object.
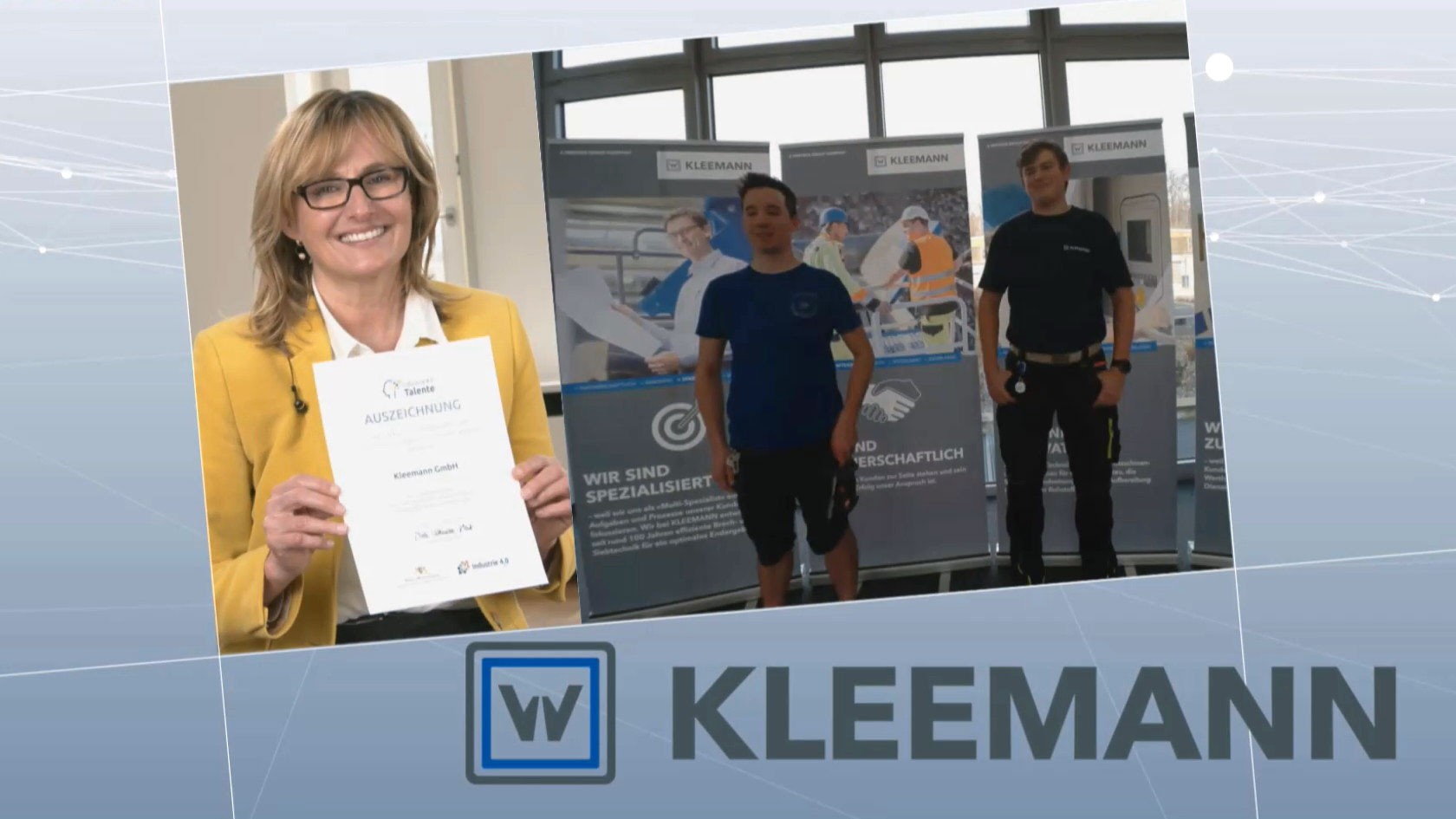
Kleemann GmbH / Stuttgart/Göppingen, Baden-Württemberg
With its continuous competition "Industrie 4.0-Talente", Allianz Industrie 4.0 Baden-Württemberg places the focus on the implementation of Industry 4.0 projects in training systems in industrial companies. The winners in the first award round in 2021 also include members of the Wirtgen Group. For the innovative project Digital Youngsters – Digitalisation in the Training Workshop, the Allianz awarded a prize to trainees from Kleemann.
In the course of the competition "Industrie 4.0-Talente", a search was carried out for excellent implementation examples of Industry 4.0 during training. The first seven projects have now received awards. One of them: the training workshop of the Digital Youngsters, was described by Katrin Schütz, parliamentary under-secretary in the Ministry of Economic Affairs, Labour and Tourism, Baden-Württemberg, not only as an "exciting project that has absolutely earned the title 'Industrie 4.0 Talent'" but also as an "outstanding concept". With this award, the Kleemann trainees receive a certificate of honour and insignia of the Federal Land Baden-Württemberg and an individually Industry 4.0 special prize. In the framework of the award ceremony, they were also given the opportunity to present the project to the eminent specialist audience.
"Kleemann GmbH has developed an excellent training workshop concept for their Digital Youngsters."
Katrin Schütz, parliamentary under-secretary in the Ministry of Economic Affairs, Labour and Tourism, Baden-Württemberg
Industry 4.0 is the name given to the modern technology and production in the age of the digital revolution. The term also covers new technologies that permit humans and machine to network via the Internet – even basic commodities and packaging, for example, are connected to the network via QR or barcodes. This networking takes place in real-time and beyond company limits. The digital transformation also requires the adaptation of competencies as well as learning methods and content for junior staff members. This further developed form of training is referred to today as Training 4.0. The use of smartphones, tablets or laptops for training is part of the daily routine. They can be used, for example, to call up learning platforms with digital learning contents as well as the digital training folder. However, lots of companies go even further and integrate virtual content for example.
Three main areas form the core of the project of the digitalised training workshop: the digital tool management system, a digital learning platform and a digital instruction management system.
Kleemann uses GARANT Tool24 cabinets and software. The drawers and vertical cabinets make simple and effective removal and storage of tools and keys possible. At any one time it is possible to determine who removed which object.
VOCANTO is an eLearning platform for business and industrial-technical training. The platform makes it possible to explain complex subject matter in a comprehensible and practical manner with detailed 3D animations, simulations and descriptive videos.
Info films prepared by the trainees in close co-operation with the instructors explain the machines and allow trainees to operate them subsequently without the assistance of foremen. QR codes on the machines make reference to a special video in the network.
Tim Heiler, apprentice mechanic, and Johannes Lauer, apprentice electronic technician, present the three digitalization tools from their training course in the framework of Industry 4.0 Talent. We were able to visit the two of them at their training place and asked them about the subject of digitalisation.
Hello Tim, hello Johannes, thanks for taking the time to talk to us. How are things going just now with your training?
J: Everything's fine. I learnt a lot in the last year. In the meantime I'm in my third year of training. At the moment we're preparing for our exams and of course I hope that everything works out well. When I'm finished, I want to continue working at Kleemann.
T: It certainly won't be boring. Time passed really quickly at Kleemann! I'm now in my second year of the course and recently had my intermediate examination.
How did the Digital Youngsters project come about?
J: Actually, the project has been around for a long time. Kleemann didn't just start with digitalisation yesterday. And it wasn't only us trainees who started it, but before Tim and I came on board – and of course also in close co-operation with the trainers and teachers. However, we always have the right to say our mind. It's precisely input from young people that is appreciated. Some of us are familiar with completely different technologies and have other skills than older colleagues. And Kleemann knows that they can also benefit from us. It's not just a one-way street. A good example of this are the films from digital instruction management system.
What is the purpose of the films? How did they come about?
T: The instruction videos were planned and prepared completely by the trainees. The first task was to decide which machines would be suitable for the videos – and then the order in which the clips are prepared. We then worked out how the training contents are to be conveyed. At Kleemann, for example, we start with drilling and then move on to mill cutting. And this is how we proceeded. A plan was first drawn up as to how the videos could be structured. Of course this was discussed with the foremen and also the Marketing department.
J: When preparing the videos, it was necessary to dig deep into the subject matter. This means that we benefited in two ways: on the one hand, the videos make the introduction to the respective subject easier and, on the other hand, we were able to deepen our knowledge of the machines and reinforce our know-how.
Another part of the project is the digital key and tool management system. What can you tell us about this?
T: It was the trainees themselves who suggested setting up the system. We decided on the tools that we wished to place in storage and used this as the basis of our system – including the integration of our electronic key cards.
J: Basically, our intention was to simplify the tool and key management system. If I need a cordless screwdriver, for example, and determine that it's not in the cabinet at the moment, I can look in the system and see who borrowed the screwdriver and can approach the relevant person directly. This also reduces property loss because the system ensures that it is more likely that removed objects are placed back in storage correctly.
And what's the learning platform all about? How do you use it?
T: The eLearning platform with its well-structured subject preparation and detailed 3D models helps us to understand complex contents. It also includes a point system. This is fun because it, more or less, allows us to "battle" against other trainees. The platform allows trainers to see at a glance which individual trainees have room for improvement and can convey the content to those who are struggling a bit in a targeted manner.
J: Another special mode is used before the exams to prepare us specifically for the relevant exam. This is very practical! And it was a particularly helpful tool during the Covid-19 pandemic because we were able to prepare everything well and in safety at home in self-study.
T: But of course we do not use all of this only in home office. At work we attached QR codes to the machines. When we scan them, we receive questions on the respective machine directly. Another very practical feature!
Are you - as trainees - also involved in other digitalisation measures?
J: We are currently digitalising the complete training organisation. This means, for example, we will be able to see in our flow charts when, where and what we are learning in the company. We want to create an app for this purpose.
What was it like for you to receive an award for the project?
J: In a video interview, the presenter Volker Groß joked that he could hardly concentrate on the presentation of our content because Ms. Schütz was so enthusiastic and was always saying "that's fantastic. That's a great idea!"
T: Of course that pleased both of us and the other Kleemann trainees as well and also made us a bit proud. The award is really a great honour because, after all, it's the biggest industrial association in the region.
J: The award showed us that we can keep up with considerably larger companies. And that makes us very proud at Kleemann!
What makes digitalisation and Industry 4.0 so important for the future?
T: Digitalisation is good and important! Times are changing. There's no way to avoid new technologies and digital support. Of course this also applies to industry. However, not all companies have recognised this transformation. And continue to work according to the motto "What worked in the past will work in the future". That is not quite right.
J: With such an attitude, they will fall by the wayside sooner or later. This is why it is extremely positive for us to complete our training in a company like Kleemann that moves with the times.
"I remember about a year ago on a foreign trip that an entrepreneur told me she needed something like this. And they put it into practice. Great!"
Katrin Schütz, parliamentary under-secretary in the Ministry of Economic Affairs, Labour and Tourism, Baden-Württemberg, on the Digital Youngsters project