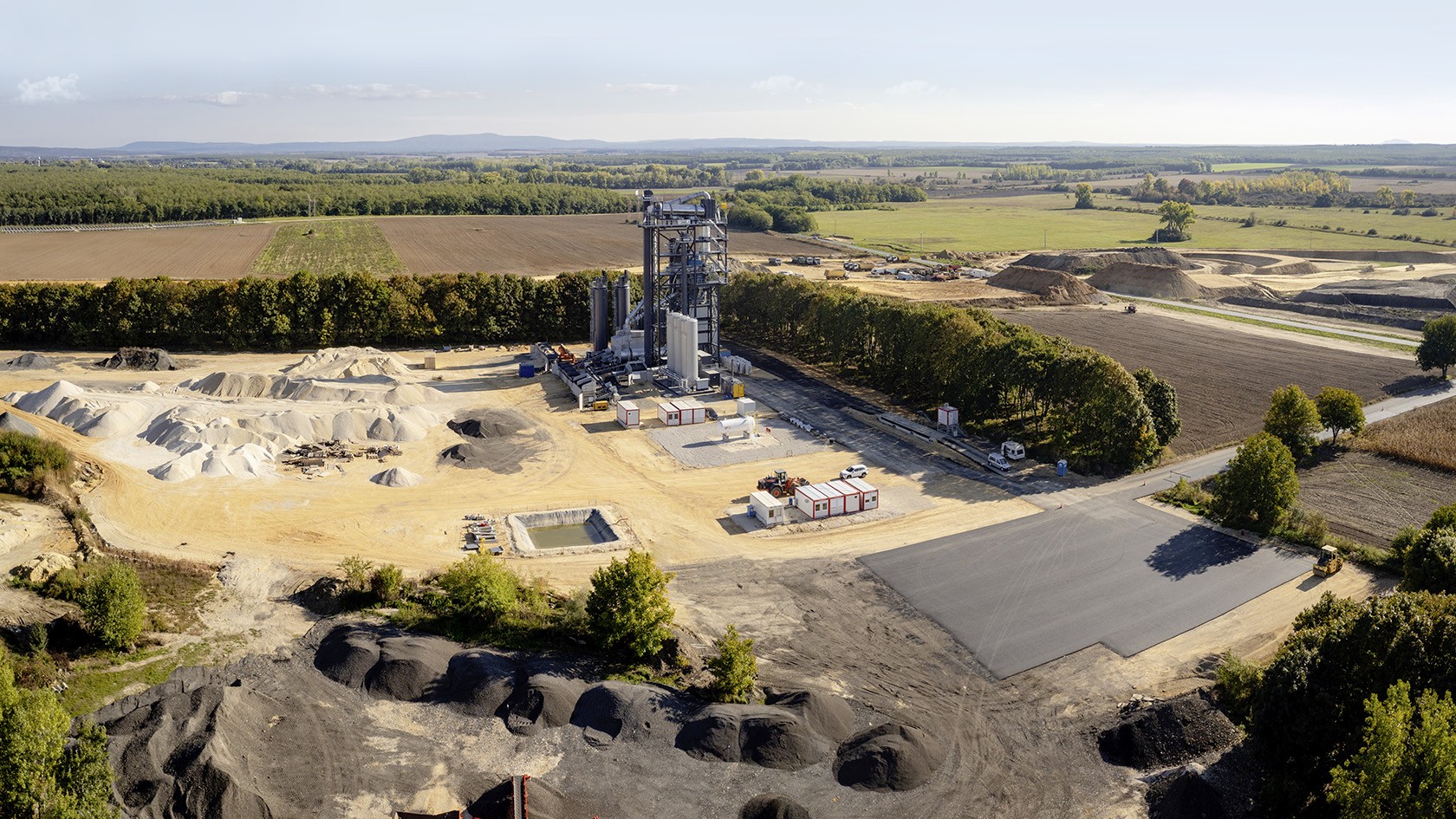
The Hungarian construction company Hódút Kft. have commissioned a Benninghoven TBA 3000 asphalt mixing plant. Thanks to the country’s first parallel drum, the plant can produce fresh asphaltic mixtures containing up to 70 % reclaimed asphalt. The maximum possible recycling content in Hungary is currently 20 % for cold recycling and 40 % for hot recycling. The Benninghoven hot recycling system therefore leads the way to more sustainable road construction while strengthening the company’s position for the future.
“In Hungary as well, there are now more roads being refurbished than built new. This creates an increasing volume of reclaimed, milled material. In future, we will be able to produce high-quality asphalt mixtures from this, and it can be used for more than just base courses. Because asphalt belongs on the road – and not underneath.”
Zsolt Surnyák, Chief Production Engineer at Hódút Freeway Kft.
Photo:
www.magyarepitok.hu – Dernovics Tamás
Asphalt production with a high content of recycled material, such as milled asphalt, is drawing the interest of road construction authorities and operators in more and more countries. The same also applies in Hungary. Hódút Freeway Kft. at its site in the municipality of Tét near the city of Győr has invested in a TBA 3000. The Benninghoven asphalt mixing plant is the first plant in Hungary with the proven hot recycling feed system with a parallel drum that can produce asphaltic mixtures with up to 70 % milled material. Until now, Hungarian asphalt producers typically added a maximum of 10 – 15 % recycling material to the mixing process.
The TBA 3000 with parallel drum is of crucial importance to the entire Hungarian road construction sector. The Benninghoven plant allows the authorities to verify how mixtures with a higher recycling content hold up in practical application. “For us, the key aspect of this investment was to think about the future. The trend is going towards an ever higher recycling content. That saves virgin mineral while avoiding waste, and of course we like that,” says Szabolcs Rosta, Chief Engineer for Innovation at Duna Aszfalt Zrt, the parent company of Hódút Freeway Kft.
Up to 70 %: The TBA 3000 with parallel drum is the first new asphalt mixing plant in Hungary to deliver asphaltic mixtures with more than 20 % recycling content.
“We are honoured that Hódút have placed their trust in our technology for the hot recycling premiere in Hungary,” says Steven Mac Nelly, Head of Development & Engineering at Benninghoven. And there is a good reason for that: “Benninghoven already developed the hot recycling technology of the recycling drum or parallel drum for 70 % recycling content to maturity many years ago.”
The new plant in Tét is already the fourth Benninghoven plant operated by Hódút. “This is in large part due to how much we appreciate the good customer service provided by Benninghoven and the entire Wirtgen Group. We have a fixed contact who always reacts to our issues promptly and is a great partner when we need spare parts or support,” says András Matvon, Chief Engineer.
“We are honoured that Hódút have placed their trust in our technology for the hot recycling premiere in Hungary.”
Steven Mac Nelly, Head of Development & Engineering
Benninghoven
Highlights of the hot recycling feed system with parallel drum
In addition to a separate parallel drum for heating the recycling material, the TBA 3000 also integrates the cold recycling technology with multi-variable feed. This allows Hódút to add up to 40 % of asphalt directly into the mixer cold. “This increases our flexibility. For formulations with a relatively low recycling content, we use the multi-variable feed and save energy,” says Zsolt Surnyák. Base materials with a high fine particle content are dosed into the mixing process through the multi-variable feed. That means they cannot clog up the parallel drum. This hot recycling feed system will be used whenever larger volumes with a high content of recycling material have to be produced.
Hódút have been working intensively in the field of hot recycling for many years. The decision to use recycling technology, which makes the construction company a pioneer in Hungary, was carefully prepared by the management at Hódút together with their contacts at the Wirtgen Group. “Before anything else, we wanted to have an exchange on asphalt production with a parallel drum. Benninghoven made that possible,” explains Szabolcs Rosta, the largest Hungarian construction company Duna Aszfalt. Hódút employees shadowed the production at two plant sites in Bavaria over the course of three days. The Hódút delegation were able to clarify a great number of questions at the Benninghoven customers Karl Bachl GmbH & Co. KG in Wotzdorf and Grossmann Bau GmbH & Co. KG in Söchtenau.
This was particularly valuable because there is still very little experience with hot recycling technologies in road construction in Hungary. In Germany, on the other hand, this manufacturing process has been long established. “We really benefited from the exchange with the owners and users in Bavaria. Everyone involved was happy to share their great store of knowledge with us,” says András Matvon. One key training aspect was recycling management, i.e. procuring milled material from refurbishment projects, correctly storing the materials with a roof for protection against moisture and handling the reclaimed asphalt in the plant.
Product trainers from Benninghoven had established the contacts and accompanied the Hódút team to Bavaria, where they trained the Hungarian employees extensively. “They instructed us in all the special aspects that have to be taken into account for hot recycling of reclaimed asphalt,” says Zsolt Surnyák. “Our partners showed us everything from storing the milled material and establishing formulations with the recycling generator in the Benninghoven control unit to servicing the recycling section. That has enabled us to work with our new TBA 3000 with parallel drum successfully from the outset, which was very important to us. In addition, we were able to experience the cooperative spirit of the Wirtgen Group first hand. The high level of reliability played an important role in our decision to purchase the Benninghoven plant.”
“We really benefited from the knowledge transfer and the exchange with the Benninghoven experts and mixing plant owners.“
Szabolcs Rosta, Chief Engineer for Innovation
Duna Aszfalt
Hódút selected the site in Tét strategically so that the Benninghoven hot recycling feed system could be utilized to its full capacity from the outset. Here, near the city of Győr in the northwest of Hungary, the M 83 motorway is currently being built. The road construction company were awarded the contract for building a section of the new motorway and for resurfacing the old section of the M 83. The M 1 motorway that connects the capital Budapest with Győr and Vienna is also located close to the asphalt mixing plant. There are plans to resurface and expand this connection as well. The asphalt mixing plant with parallel drum could play an important role in this project. In any case, Hódút Freeway Kft. are pushing full steam ahead to be ready for future projects and will be able to use 40 – 60 % recycling material in the mixing process.
TBA 3000 with parallel drum at their site in Tét, Hungary: The Plug & Work concept allows Hódút to relocate this complex asphalt mixing plant to a different site relatively quickly and easily if required.