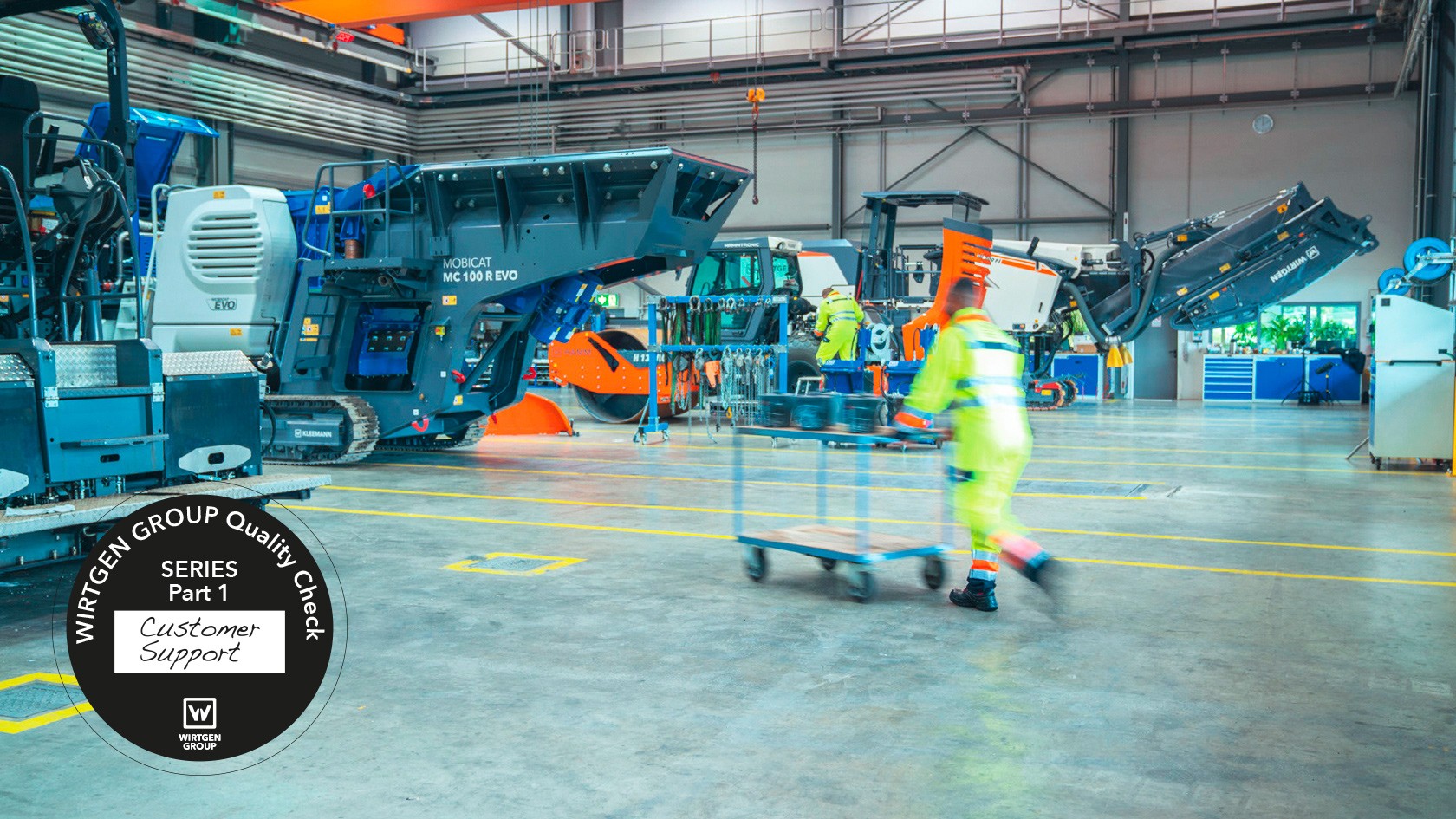
The Wirtgen Group’s service philosophy offers maximum customer proximity – and this means that the experts from Wirtgen Group Service will very soon be on the spot to clear up any issues customers may be having with their machines. A large number of subsidiaries and numerous authorized dealers ensure that we are never too far away in markets around the world.
Customer Support is where skilled craftsmanship meets advanced technology. ‘In critical situations, our service team is on call 24/7 and ready to deliver rapid solutions’, says Jochen Kohl, Workshop Manager Wirtgen Group Sales and Service Germany, at the Group’s headquarters in Windhagen. ‘Close to our customers’ also applies to our highly professional workshop service. State-of-the art workshops around the globe offer the entire spectrum of reliable workshop services. Inspection, maintenance and overhauling of machines are just as much a part of the service package as servicing and repairs. The workshops also ensure that auxiliary equipment is correctly fitted in compliance with the manufacturer’s specifications.
Thanks to efficient and effective organization and preparation, Workshop Service can also handle complex and challenging jobs.
‘As Wirtgen Group Workshop Service, we have the enormous advantage of being specialists for our own product range’, Kohl explains. Professional maintenance and repair of technically advanced machines requires qualified and specialised experts. That’s why the Wirtgen Group has installed a dynamic training system that is constantly updated to take account of the latest developments. This means that the workshop teams at Wirtgen Group subsidiaries and dealers are given regular training at our brand’s headquarters to ensure that they can offer customers in their markets highest quality across the entire service spectrum.
When new Wirtgen Group machines come onto the market, the response is immediate. ‘Together with our WIDOS information system and WIDIAG diagnostic software, we have the ideal tools for ensuring that machines get back on the road right away.’ What’s more, the subsidiaries and dealers can rely on support from the German brand headquarters in the event of more complex problems.
Decades of experience and a high number of machines in the market ensure a high level of expertise in service issues. Every employee of the Wirtgen Group Workshop Service organisation has direct access to the entire know-how of the group at any time. ‘This knowledge grows from day to day as new findings from the field are systematically documented and made available to all employees’, Kohl explains.
‘Regular workshop visits bring the benefits of high machine availability and lower operating costs.’
Jochen Kohl, Workshop Manager Wirtgen Germany, Windhagen
Thanks to special tools, faults and malfunctions can be rapidly identified and localized.
Heavy duty overhead cranes in the four 25-meter workshop bays and a well-lit inspection pit enable work to be performed quickly and safely, even on large machines such as Kleemann crushers or Wirtgen large milling machines. The workshops also have the very best equipment for repairs to electronic or precision engineered components. Diagnostic computers and measuring instruments designed especially for Wirtgen Group machines help to identify and localize faults. The vibration frequency and amplitude of vibratory rollers can, for instance, be checked using the Hamm frequency and amplitude measuring device. Such special tools not only make it easier to locate faults, but also help with subsequent adjustments and calibration.
The range of tasks extends from thorough inspections and immediate repairs to general overhauls. New optional equipment can also be integrated into machines while in the workshop – for instance, retrofitting the AutoPilot Field Rover in anSP 25i slipform paver.All necessary components are expertly installed and checked. Once the work has been completed, the specialists subject the machine to rigorous quality checks.
We contribute to the success of our customers with a comprehensive range of service agreements.
When servicing the premium products, the workshops install only genuine Wirtgen Group spare and wearing parts. These are optimally tailored to each machine to prevent potential fitting imprecision. The decades of experience in the field are also reflected in the high quality and long life of the original parts. Oils and lubricants are no exception.
The lubricants are specially formulated for the key components of the machine. Together with high-grade basic oils and sophisticated additive technology, they improve efficiency and prolong the service life of the machine by providing optimum protection against corrosion and wear. This means that machines can work at maximum performance, even in tough field conditions.
Tailor-made: repair, care and maintenance for all Wirtgen Group machines.
Genuine Wirtgen Group spare parts and lubricants sustainably increase the efficiency and service life of the machine while permanently reducing operating costs. ‘In this respect, we also recommend the use of WIDOS’, Kohl adds. WIDOS provides comprehensive electronic documentation for all machines of the Wirtgen, Vögele, Hamm and Kleemann product lines in a single system. Regularly updated, the digital documentation includes the complete Parts and More spare parts catalogue, instruction manuals, electrical, hydraulic and hosing diagrams, machine data and the safety manual. One of its key benefits is that components can be identified quickly and easily, and ordered at the press of a button. All this makes WIDOS an indispensable tool for workshop personnel, service engineers, buyers and technical managers.
With SmartService, the Wirtgen Group also offers a flexible service agreement tailored to individual needs. This includes maintenance in the workshops of the sales and service organisations, visual inspections, checks for wear and tear, technical inspections and software updates, measures that all help to avoid unexpected and costly machine downtimes. ‘A further advantage is that the sales and service organisations handle all process-relevant administrative and organisational matters, leaving customers free to concentrate exclusively on their core business.’ But that’s not all: Different requirements demand different solutions. ‘That’s why SmartService has a modular structure and is tailored entirely to personal wishes’, Jochen Kohl adds.
Other topics in our Customer Support series:
Part 4: Application Consulting
Part 8: Chrome Steel Blow Bars
Part 12: Tool Change for Impact Crusher
AT WIRTGEN GROUP