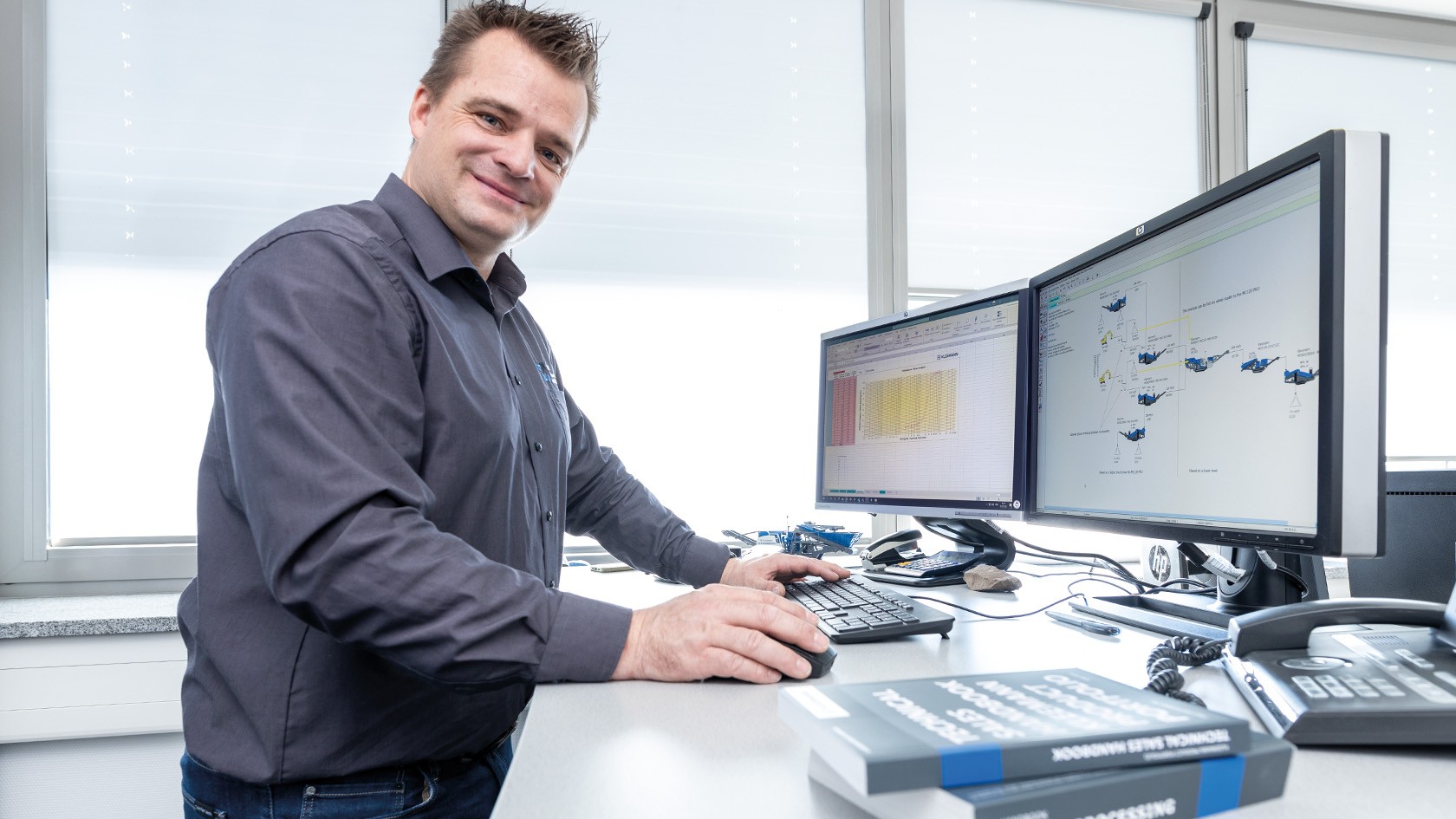
Application experts impress with their high competence and the use of modern planning software such as AggFlow
What end result does a plant deliver? What output level can be expected? Are the individual elements of a plant train perfectly tuned to one another? A new plant has to be well planned and forms the basis of productive work. To find the correct answers to this is the core competence of Kleemann Application and Process Engineering.
For many years the Kleemann team has been in demand for field missions and was able to gain experience in a very wide variety of customer projects. This is know-how that helps our technicians today in the planning of mobile plant trains: "In Application Technology at Kleemann we possess the basic process and application know-how. If someone wants to know whether a certain product can be produced with a certain machine, they have to ask us."
"In Application Technology at Kleemann we possess the basic process and application know-how."
Application and Process Engineering team, Kleemann
"On the one hand, we need details on the desired final product. Which volume and specifications are desired? On the other hand, we need information on the raw material. What type of stone is it, what is the degree of contamination, do we already have material parameters?"
Starting material and final product – planning the process between these two parameters as exactly as possible is the job of the Kleemann application technicians. "In practice, by the way, customers often don't know exactly which material parameters their stone has that are relevant to crushing. We offer an examination of stone samples in our laboratory", says Frank Lebender.
The stone is on the test bench in the Kleemann laboratory. The test procedure used by Kleemann Application and Process Engineering to examine the material properties can be found in the magazine article "Service for Kleemann Customers".
The basis for the development of new plants is a flow chart worked out on a sound footing, a so-called "AggFlow". An AggFlow demonstrates what the plant can produce by means of simulation. This is an extensive process, above all, with large plant trains. After all, cost-effective processing requires the interaction of numerous components: the selection of the crushers is decisive, screening plants must have the correct dimensions and configuration and stackers must have an output tuned to the complete plant.
The latest planning software: the AggFlow simulates what the plant ultimately produces.
Tailor-made planning of a plant train requires good planning software, but also a lot of experience and a sure instinct. After all, even if the software supports the application technician and the Kleemann laboratory supplies reliable values on the properties of the raw material – the bottom line is it's a lot of manual work. "Basically, each unit has to be assembled separately, but we have to keep an eye on the complete plant at the same time", say the experts. "Which crushing tool produces the required output with as little wear as possible? Which crusher is used in the circuit with which screening plant? A lot of experience is needed to ensure that it really works in the end."
"Basically, I have to assemble each unit separately, but also have to keep an eye on the complete plant."
Frank Lebender, team member of Application and Process Engineering
To guarantee an optimum process, the application technicians are also on site if necessary to perform work on coupled plants. "We've already had a lot of real surprises there", relates the technician. "My colleague, Jens Behn, for example, was in a basalt quarry in Cambodia where the machinery behaved in a manner completely unknown to us. An unbelievably high level of wear was observed on the cone crusher, whereas the impact crusher held out for an unusually long time. Jens then altered the plant configuration completely, ordered new parts and worked on the settings. Today the plant is running perfectly."
Kleemann regards good tuning of the plant as a natural element of service. Existing machines can also be incorporated in the planning. "Of course the customer has to be able to count on the plant functioning as agreed. This is why we test and optimise until everything is running as it should", says Frank Lebender.
Frank Lebender (left) and Anatolij Schlegel (right) present at the stone sample examination.
During the new and further development of machines
Based on their expertise and extensive practical experience, the application and process technicians are also contact partners in the company when the new and further development of machines are involved. They know the crucial issues, which are often very detailed, and can advise the developers.
At the local dealers and branches
The first contact partners for customers are the local subsidiaries and dealers. Here, you can also rely on competent experts who can provide comprehensive advice. In some of the subsidiaries, AggFlows can also be prepared. When detailed planning, checking and optimisation is required, customers can count on the expertise and commitment of Kleemann Application and Process Engineering.