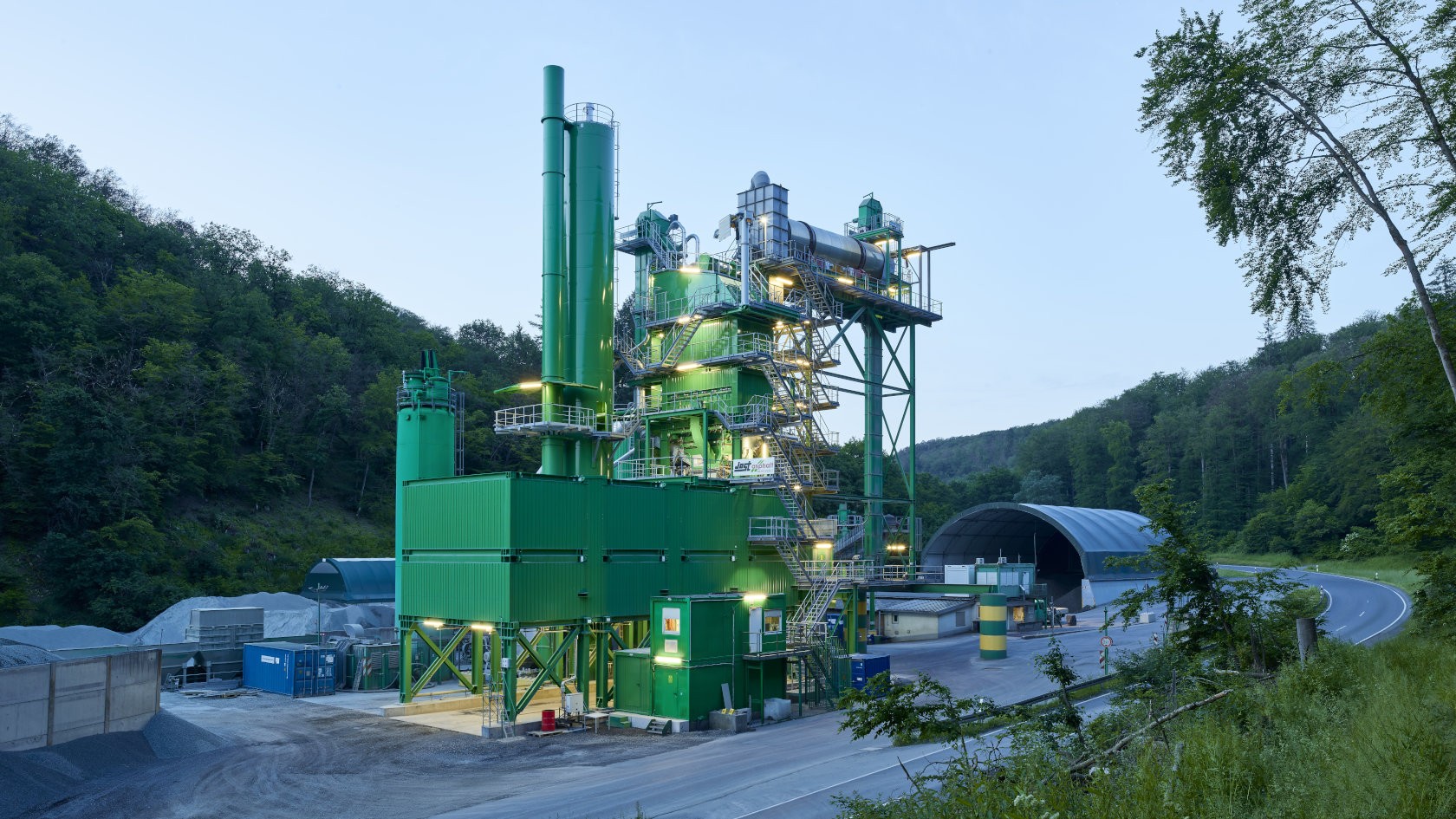
Braunfels (Taunus) | Germany
Retrofit solutions from Benninghoven can meet a very wide range of requirements. This has been clearly shown by a project in Taunus, which involved the complete replacement of two core parts of the plant, despite cramped working conditions and existing systems to be worked around. The parts in question were the mixing tower and drying line. The recycling plant and other units were to be left untouched, however. This type of ‘open-heart surgery’, which presented a major challenge as regards planning, logistics and installation, was met by a seasoned team from Benninghoven in close consultation with the customer.
Benninghoven was approached by a team from Wilhelm Jost GmbH & Co. KG, who explained they were looking to boost their production output from the current 200 t/h. In this initial situation, the existing mixing tower in particular was increasingly becoming a bottleneck. This road construction contractor from Taunus had been successfully building its business over the last 20 years. The company’s own laying fleet installed 80% of the asphaltic mixture from the Braunfels plant itself, with only a fifth being sold.
Even though the original plant was from a competitor, Jost decided to work with Benninghoven for the new project. “We do have a long-standing business relationship, however,” explains Managing Director Bernd Jost, “which started 15 years ago with the retrofit of an EVO JET burner. This burner has been running perfectly ever since. This simply confirmed Benninghoven’s famously good reputation, and I’ve never regretted working with them in the past.” The long list of joint projects completed so far includes retrofitted bitumen tanks, the incorporation of cold and hot recycling feed systems, and the replacement of a plant control with a Benninghoven BLS 3000. “This is why we had every confidence that our partner would also meet all of our expectations in full for this project,” explains Bernd Jost.
“Past projects have further confirmed Benninghoven’s famously good reputation, and I’ve never regretted working with them in the past.”
Bernd Jost, Managing Director, Wilhelm Jost GmbH & Co. KG
Old components intelligently integrated: a look at the newly renovated mixing plant at Wilhelm Jost GmbH & Co. KG in Braunfels im Taunus.
During initial discussions with Jost on site, it became clear that the drying line would need to be replaced along with the mixing tower in order to really boost production output. This was because the capacity of the old hot bin section for storing heated virgin mineral was only 80 t. With the new Benninghoven system based on the TBA 4000 series, this has now risen to 130 t in seven bins, with screening plant capacity of 290 t/h. Jost has doubled its loading silo capacity to 440 t. Up to eight separate types of asphaltic mixture can now be stockpiled here, with two chambers also offering long-term storage. This increases delivery flexibility.
A decision was also made to pick a new mixing tower from the TBA 4000 plant type. Thanks to a 4-tonne mixer, Jost can now produce up to 320 t/h of asphaltic mixture from a wide range of recipes – as typical for a Benninghoven system. And, thanks to the retention of the existing Benninghoven parallel drum hot feed system, a recycling rate of up to 70% will also be possible. With the cold recycling system mixer feed, a rate as high as 30% is also possible.
Photo: High-precision work – one of the biggest challenges faced by the Benninghoven team was the sheer lack of space. The plant lies in a valley and directly adjacent to a public highway.
Jost lost no time in picking out the new components needed. This was ensured by a visit from the plant team and project team to Benninghoven’s main factory in Wittlich, where the guests were able to check everything out and have any questions answered. Expert advice was provided here by the planning experts from Bennighoven’s Technical Office.
Planning was not such a simple matter, however. As existing components and sections of the plant had to be retained, there were a lot of ‘fixed aspects’ to keep in mind: structural elements that could not be modified, and which engineers had to ‘plan around’ with their new mixing tower and drying line. For this extremely confined installation space, Benninghoven also completed a structural analysis for the mixing plant and loading silo steelwork, which included calculating the supporting loads for the on-site concrete foundations and the required steel sections.
The recycling plant, with its parallel drum some 30 m high was of course the biggest obstacle of all. Yet integrating the other components such as the cold feed unit, the EVO JET burner, the coal dust silo and the bitumen tanks plus piping was also demanding – and not just for planning but also during the later installation. One unique challenge was also offered by the need to keep the control cabinet plus its container in place while also integrating another container. This second container was used to install the new component control cabinets for the mixing tower, loading silo, dryer drum and dust extractor. The frequency converters for the exhaustor and the dryer drum were housed in an additional control cabinet container.
“For our Retrofit business unit, the recipe for success is a ‘peace of mind’ package for the client – so we handle everything, from planning through to commissioning.”
Achim Keller, Sales, Benninghoven
With such a large and demanding retrofit project as this one, there is no guarantee that everything will go smoothly, as there are quite a few unknowns. Onsite, some things turn out differently than as planned in the office. A knack for improvising while focusing on the ultimate goal is what is then needed. Most important, however: “It’s really crucial that you have a partner you can trust 100%, especially on a major investment project like this one,” comments Kai Phillips, Project Manager at Jost.
And in this case, Benninghoven’s team certainly earned that trust, given the sheer complexity of the job in hand: “We started dismantling the legacy components in winter. The aim here was to have the new technical systems up and running within six months. And that’s what we more or less delivered – we finished just a few days later,” says Christian Bode, Project Manager at Benninghoven. “For our Retrofit business unit, the recipe for success is a ‘peace of mind’ package for the client – so we handle everything for the customer, from planning, dismantling and installation through to commissioning. We’re old hands at this by now – as the project in Braunfels has demonstrated once again.”
Jost’s Mixing Supervisor Frithjof Löhr was certainly impressed: “Well, as with any major project, there are moments when things don’t go to plan and you get that sinking feeling... But at the end of the day, the boys from Benninghoven really did do a great job. Once all of the commissioning tests were complete, the time had finally come: the first asphaltic mixture trucks from Wilhelm Jost GmbH & Co. KG set off for the building site.
Photo: Asphaltic mixture feed point – commissioning of the newly renovated asphalt mixing plant is completed successfully.
“It’s really crucial that you have a partner you can trust 100%, especially on a major investment project like this one.”
Bernd Jost, Managing Director, Wilhelm Jost GmbH & Co. KG