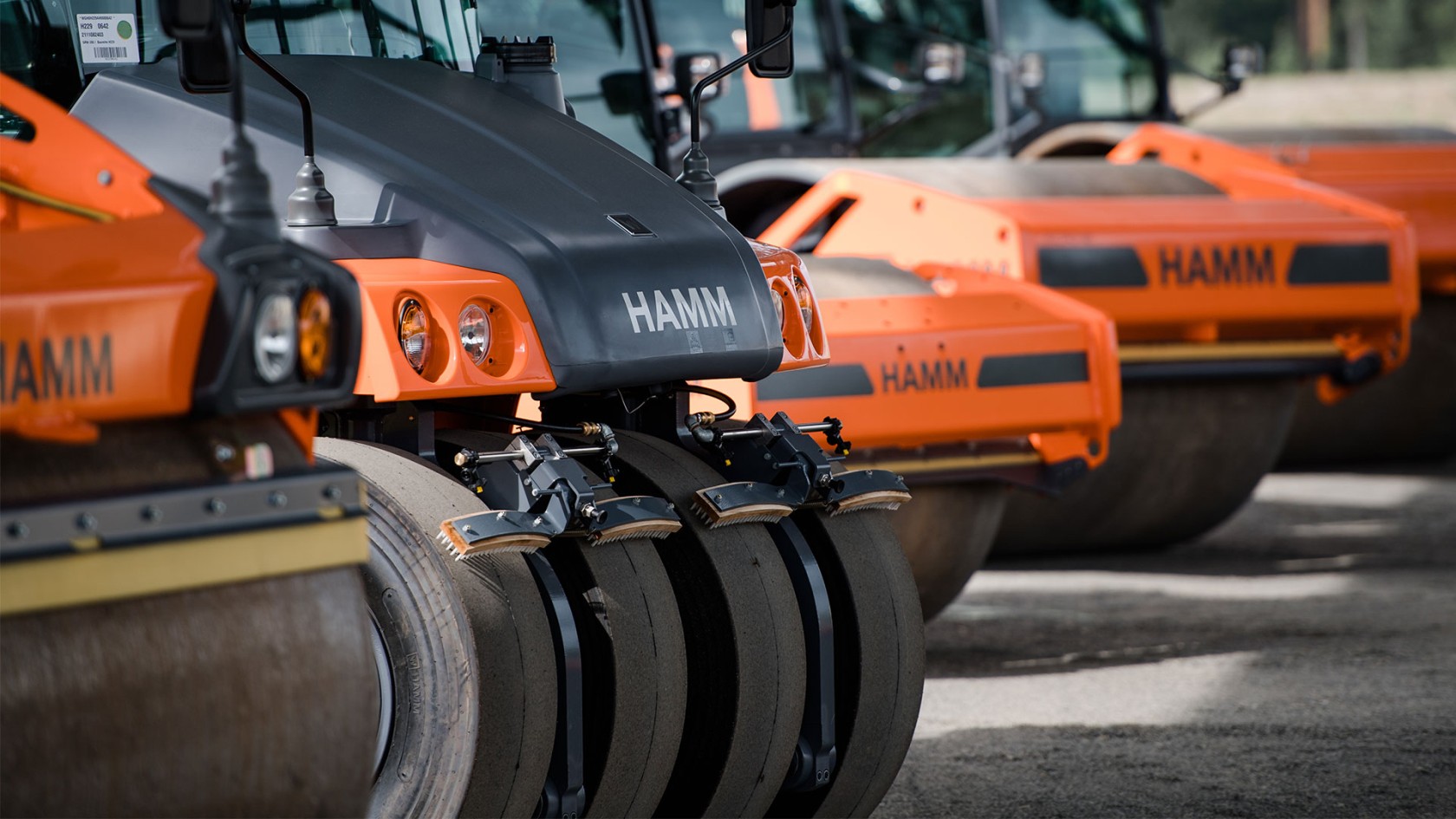
Research and development always play a central role at HAMM, just as the consideration of future trends already plays a role in the development process for new machines. The future of compaction may no longer be all that distant – and HAMM had it in its sights when developing a study on autonomously driven rollers. A second test track was commissioned in parallel in Tirschenreuth, on which rollers drive autonomously in continuous operation, which contributes significantly to accelerating product development in all areas. Last but not least, HAMM has considerably expanded its product range in the past three years. Thanks to new models and options, HAMM serves all markets across the world with regionally appropriate rollers and compaction solutions. Naturally, the continually growing requirements of exhaust gas cleaning and safety are observed here.
On the road to autonomous compaction
As part of a research project on automation in compaction technology, a trendsetting design study emerged at HAMM with the "F1 autonomous roller". It shows, for example, that an autonomously driving, electrified and GNSS-controlled roller could be equipped with markedly larger drums than today's rollers – a substantial advantage in terms of compaction quality. A modified design also leads to greater water-carrying capacity and plenty of space for future-oriented drive concepts. Moreover, the design opens up new opportunities for aspects such as transport and ballasting. HAMM is further developing the existing assistance systems based on this study. The journey takes you from today's machines with numerous assistance functions, through partially autonomous systems, and right up to rollers driven totally autonomously, as will probably be used in future.
Test track: Already been going autonomously for over 20,000 hours
An endurance test track has been in operation since 2014 at HAMM AG's main plant. The developers test prototypes there and allow new machines and models with new components to run night and day for several weeks in test operation – with no driver at all. All typical situations from everyday construction site work are simulated on these endurance test tracks. There is an inclined section, there is a zone for hardness tests of the articulated joint on earthwork rollers and a jump operation plate, a passage with many uneven spots and an additional vibration area. An appropriate programme is determined depending on the machine type and test objective. The roller completes this programme autonomously, goes for refuelling on its own and switches itself off independently after tests have finished. In this test operation, the rollers must fulfil all requirements that autonomous driving also entails. This applies all the more since HAMM installed another test track in 2019 directly beside the first. Given that, since then, two rollers could be driven in the same area at precisely the same time, HAMM developed a collision-monitoring system, yet another significant step towards autonomous driving.
Rollers in permanent use
Various rollers have already been autonomously driven for more than 20,000 hours on both endurance test tracks at the plant in Tirschenreuth. Before beginning series production, GPS-monitored prototypes in continuous driving complete an intensive testing programme here.
Two rollers simulate the construction site situation
As soon as two rollers are driving simultaneously on the test track, a typical construction site situation is automatically simulated. Important findings are drawn from this, which may provide the basis for assistance systems and autonomous driving.
Range of 170 models
HAMM always offers a finely tuned range of models, and many options and solutions for all markets. This range has been continuously further developed in the past three years. The range therefore currently includes over 70 different compactors and over 90 tandem and pneumatic-tyre rollers for earthworks. The HD 9 VV tandem roller and HD 9 VT combination roller with a 900 mm drum width, and the compact, articulated HD 14i TT pneumatic-tyre roller, have recently been supplemented. HAMM has put the HP 180i on the market to join the HP series pneumatic-tyre roller segment. It weighs between 8.2 t and 17 t depending on the ballasting, and fulfils the requirements of the markets in Europe and North America. Furthermore, additive sprinkling has been further optimised for all machines. With separate series and models of tandem rollers and compactors for local markets, HAMM caters precisely to requirements from North and South America, the Arabic-speaking world, India, China and Southeast Asia. There are currently around 30 roller types in the range for these local markets. The regional legal specifications and the increasingly strict requirements of exhaust gas cleaning are likewise observed here, as well as the demand for special equipment and spare part availability. Numerous options are also taken into account accordingly in the approval process – especially in the fields of safety, operation and lighting. There is also equipment with which the application possibilities of the rollers are expanded. This includes the split oscillation drum, the chip spreader, the diesel-driven tyre heating and the dozer blade. Amenities such as heating and air-conditioning systems are available for the comfort of the driver, as well as various seats and storage options. Finally, HAMM also offers many "green" functions and options that reduce fuel consumption and consequently CO2 emissions, as well as reducing noise emissions.
Compact pneumatic-tyre roller
The HD 14i TT from HAMM, the new pneumatic-tyre roller in the compact segment, weighs 3.5 t (operating weight with ROPS) and has a working width of 1.28 m. It fulfils the new, strict requirements of the DIN EN 474 "Field of view standard", and therefore offers even greater safety on the construction site.
HD 14i TT:
Power: 37.4 kW
Max. working width: 1276 mm
Max. operating weight: 4400 kg
Exhaust emission standard: EU Stage V/EPA Tier 4
HP series pneumatic-tyre roller
The HAMM HP series pneumatic-tyre rollers offer a modern, spacious driver's platform or panoramic cab with maximum visibility over the machine and the construction site. In this respect, all models comply with the new ISO 5006-2017 "Field of view standard" which is markedly stricter than the previous provisions.
HP series:
Power: 55.4 kW (HP 180i), 85 kW (HP 240, HP 280i), 89 kW (HP 280)
Max. working width: 2084 mm
Fuel tank: 235 l
Water tank: 650 l
HD 9 VV and HD 9 VT – drum width 900 mm
In Germany, Belgium, Austria, Sweden, Denmark, Finland, the Netherlands, Norway and Switzerland, HAMM has recently satisfied the demand for a compact roller with a drum width of 900 mm with the HD 9 VV and the HD 9 VT.
HD 9 VV, HD 9 VT:
Power: 16.1 kW
Vibration frequency: 61/48 Hz
Centrifugal force: 17/11 kN
Amplitude: 0.38 mm
High frequency for North America
HAMM also produces double vibration tandem rollers from the HD+ series with a higher vibration frequency (45/67 Hz) for the American market.
Operating weight with ROPS:
HD+ 70i VV-HF: 7180 kg
HD+ 80i VV-HF: 7540 kg
HD+ 90i VV-HF: 9210 kg
HD+ 110i VV-HF: 10,260 kg
HD+ 120i VV-HF: 12,685 kg
HD+ 140i VV-HF: 13,145 kg
New models for India
The models of the HD series and the HC series for the Indian subcontinent satisfy the local specifications in all details – from lighting to the weight classes typically demanded there.
Models:
Compactors: HC 119i, HC 119iD
Tandem rollers: HD 99i VV, HD 109i VV
Exhaust emission standard: CEV Stage IV