Paving thin layers hot
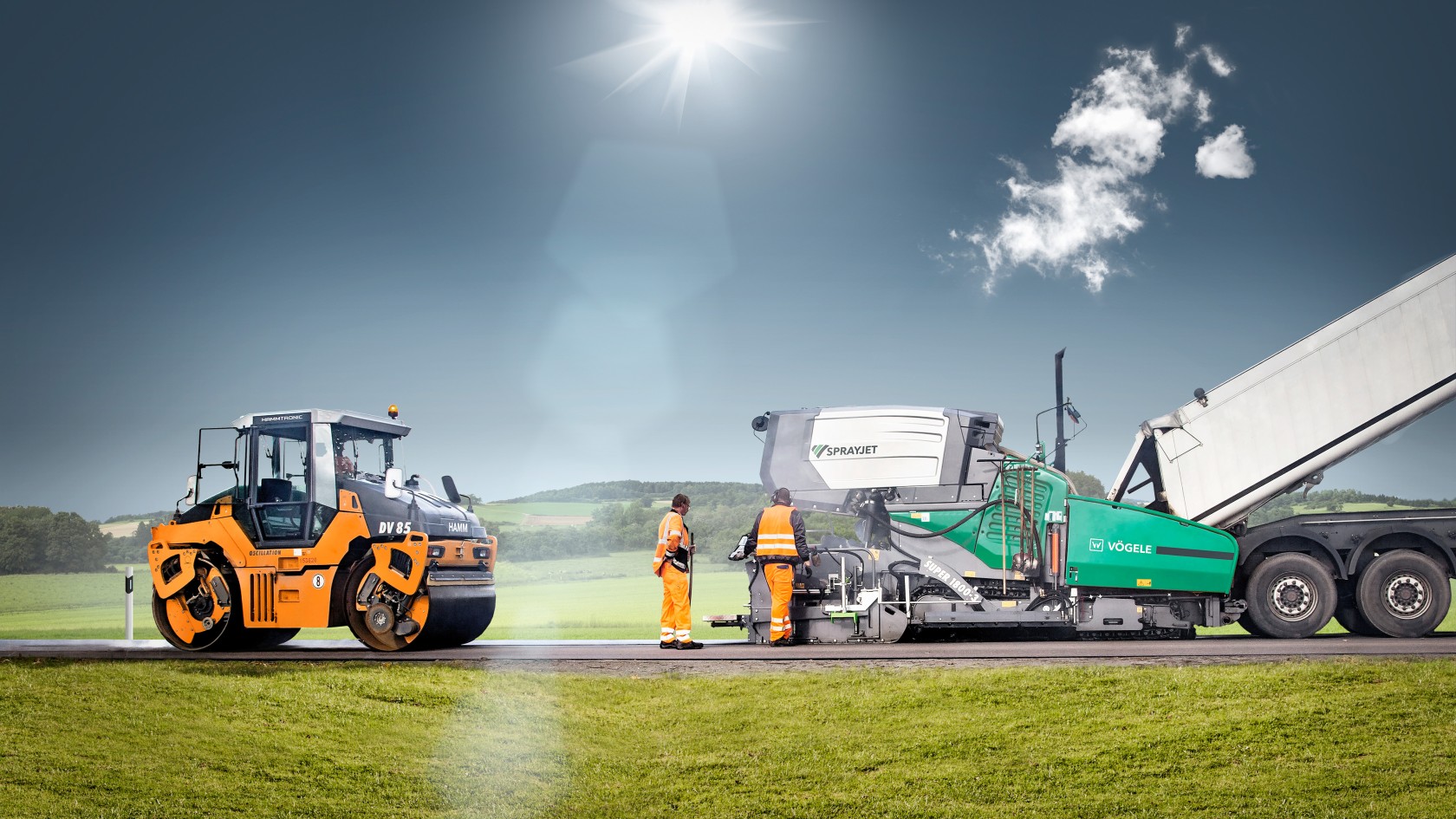
If only the top layer of a road is damaged, you don’t have to replace the entire road surface. A particularly cost-effective and environmentally friendly alternative is the process of “paving thin overlay hot onto a sprayed seal.”
Rehabilitation methods that can be carried out both quickly and with economic efficiency are becoming increasingly important worldwide. Paving thin layers in hot application is such a method, offering an exceptionally economical alternative to full pavement rehabilitation.
This makes it possible to significantly improve the surface properties of a deteriorating road, such as grip, evenness, and noise reduction, over a longer period of time. First, cold milling machines with fine milling drums are used to remove surface deformations and create an even, slightly roughened road surface.
"With the SUPER 1800-3i SprayJet/SUPER 1800-3 SprayJet, VÖGELE now presents the latest generation of spray pavers."
VÖGELE spray paverThis surface texture has the ideal properties to ensure an excellent bond with the thin layer of asphalt to be applied. The sub-base must be thoroughly cleaned before further processing. A paver with a built-in spray module is the preferred choice for paving thin layers hot. It automatically applies a tack coat of polymer-modified bitumen emulsion to seal the base. At the same time, it paves a thin asphalt surface layer just 1.2 to 2.0 cm thick.
The SUPER 1800-3i SprayJet is ideally suited to paving thin layers on spray seal or for any kind of conventional paving on tack coat.
Compaction is a major challenge when paving thin layers hot, as it requires the layers to be compacted uniformly but without causing surface unevenness. Dynamic compaction with oscillation is ideal to prevent damage to the underlying cold layer during compaction. Static compaction is another alternative, but should be carried out without vibration.
Interview with Friedhelm Pahlke Head of Sales, Germany at VÖGELE
To the Interview