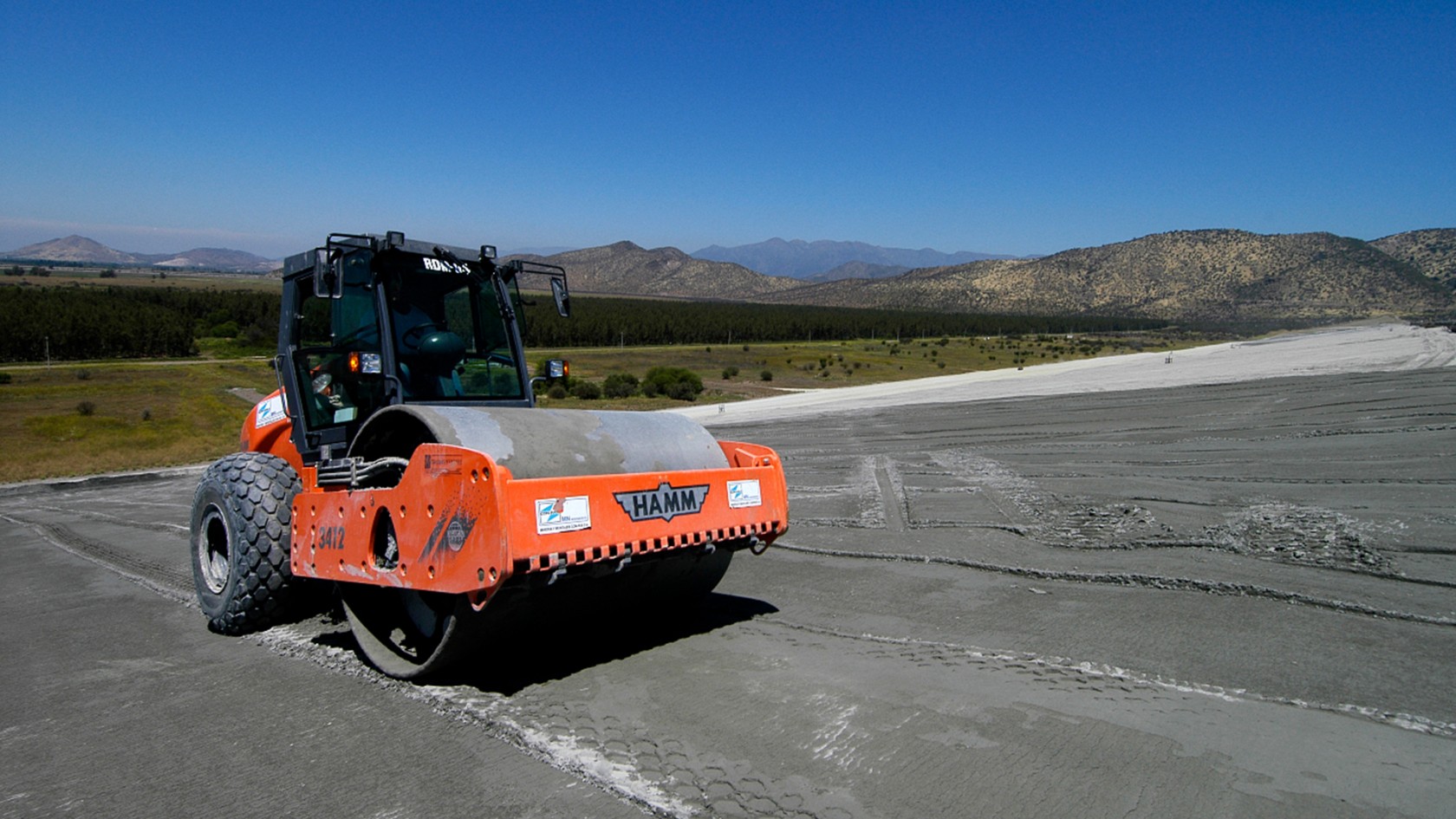
They have been used in the Río Blanco valley for months – day after day, two HAMM 3412 compactors tirelessly do their jobs, lending an impressive structure the necessary stability. This is the southern border of the 5 km² reservoir of Ovejería, near the village of Til-Til. The Chilean company Minería y Montajes Con-Pax S.A. is building a gigantic wall of almost 3 kilometres here, made almost entirely out of sand.
The slag that comes from copper production is collected in the reservoir. The shiny red metal is mined on a large scale here, because Chile has by far the largest deposits of copper in the world. The state-owned company Codelco produces the metal from the copper ore in a complex mechanical/chemical process. Slag is created by this process as a waste product, and is collected in reservoirs and later undergoes further treatment. The dimensions being thought in and worked in here are huge. Around 72,000 tonnes of ore are mined per day. Ninety-five per cent of this goes into the reservoir as slag. This basin is bordered on three sides by mountains. On the southern side, the new wall encloses the artificial lake. Likewise, much of the material for this wall comes from copper production, because the sand is extracted from the slag. The Ovejería valley has already been filled with slag for nine years now. The resulting "lake" is now 42 metres deep. Building the dam significantly increases the capacity of the natural basin – when the wall is complete, enough space will be available to house the slag for the next 50 years.
The challenge: Compacting a dam made from sand
Currently, the wall is growing day after day – or rather, night after night. Because, every night, sand with a moisture content of 16 to 20% is heaped onto the crest of the dam, distributed by a bulldozer the next day and then compacted in layers 20 cm thick. This process will be continued until the intended dam height and width is achieved. When the 32-metre-high dam is complete, its ramp will extend from the crest to 130 metres into the bordering valley. This results in an increase of between 22% and 30%. Initially, the Chileans tried compacting the sand using the traditional method, with a bulldozer towing a trailer-type roller. The disadvantage of this method is that, when driving backwards across the compacted area, the chain of the bulldozer buries itself in the sand and loosens the material once more. That is why the Con-Pax engineers were looking for a roller that compacted the non-cohesive sand sufficiently well and still offered full traction even at an incline of 30°. This search inevitably led them to the HAMM compactors of the 3000 series with Hammtronic.
The solution: 3412 compactor with Hammtronic
You can confidently designate these compactors as the "mountain goats" among the latest compaction machines. Hammtronic, an operating and control system regulated by a microprocessor, monitors all engine and driving functions. It controls start-up, braking and speed. The limit-load regulation is also effective at protecting the engine against overload. For the work in Chile, it is important that the intelligent Hammtronic also takes on automatic anti-slip control, constantly monitors the wheels and drums and continuously adjusts the available torque of the drive engines. In this way, traction is optimal at all times and the wheels are effectively prevented from spinning, no matter the type, profile or incline of the soil to be compacted.
The first tests in autumn 2004 immediately convinced the engineers. Impressed by the effectiveness of the compactors, they decided to purchase two machines with a working weight of 12 tonnes. Since then, they have compacted around 7400 cubic metres of sand day after day. The rolling pattern stipulates six passes, with one pass including one ascent and one descent.
Quality doubled, emissions halved
Civil engineer and project leader Eduardo Araos is impressed by the compaction quality. With the bulldozer, compaction was very irregular, particularly on steeper surfaces. HAMM technology provides the perfect solution to this problem. Samples and tests repeatedly confirm that the wall displays the required density and strength all the way across. But those responsible at Con-Pax are also highly satisfied because the rollers from Germany are extremely environmentally friendly and simultaneously reduce their operating costs. With their extremely low fuel consumption, each of the two Hammtronic compactors has replaced two machines with "thirsty" engines. In addition, the compactors can also compact when driving backwards, in contrast to a bulldozer with a trailer-type roller. Therefore, fewer passes are required. Overall, these effects have led to CO2 emissions being halved in one fell swoop.
Maximum uptime
The compactors have now been working continuously on this project for three years. With 5000 operating hours per machine per year, they can achieve incredibly high uptime here. Three points are decisive for this. Firstly, the solid and precise processing offered by HAMM rollers. Secondly, regular maintenance and inspection by operator Con-Pax. And thirdly, outstanding support in terms of expertise and spare parts from Alejandro Saballa, service manager at Salinas y Fabres, the Chilean HAMM distributor based in Santiago de Chile.
New application identified for dam construction
Con-Pax has recognised the potential of HAMM's extremely gradeable rollers and will also be relying on their effectiveness in other projects in future. The gradeability of the HAMM compactors allows the civil engineers to find new constructive solutions. Current planning for new dams highlights this, featuring greater inclines than were previously standard, due to the high gradeability of the rollers. HAMM technology makes this possible.