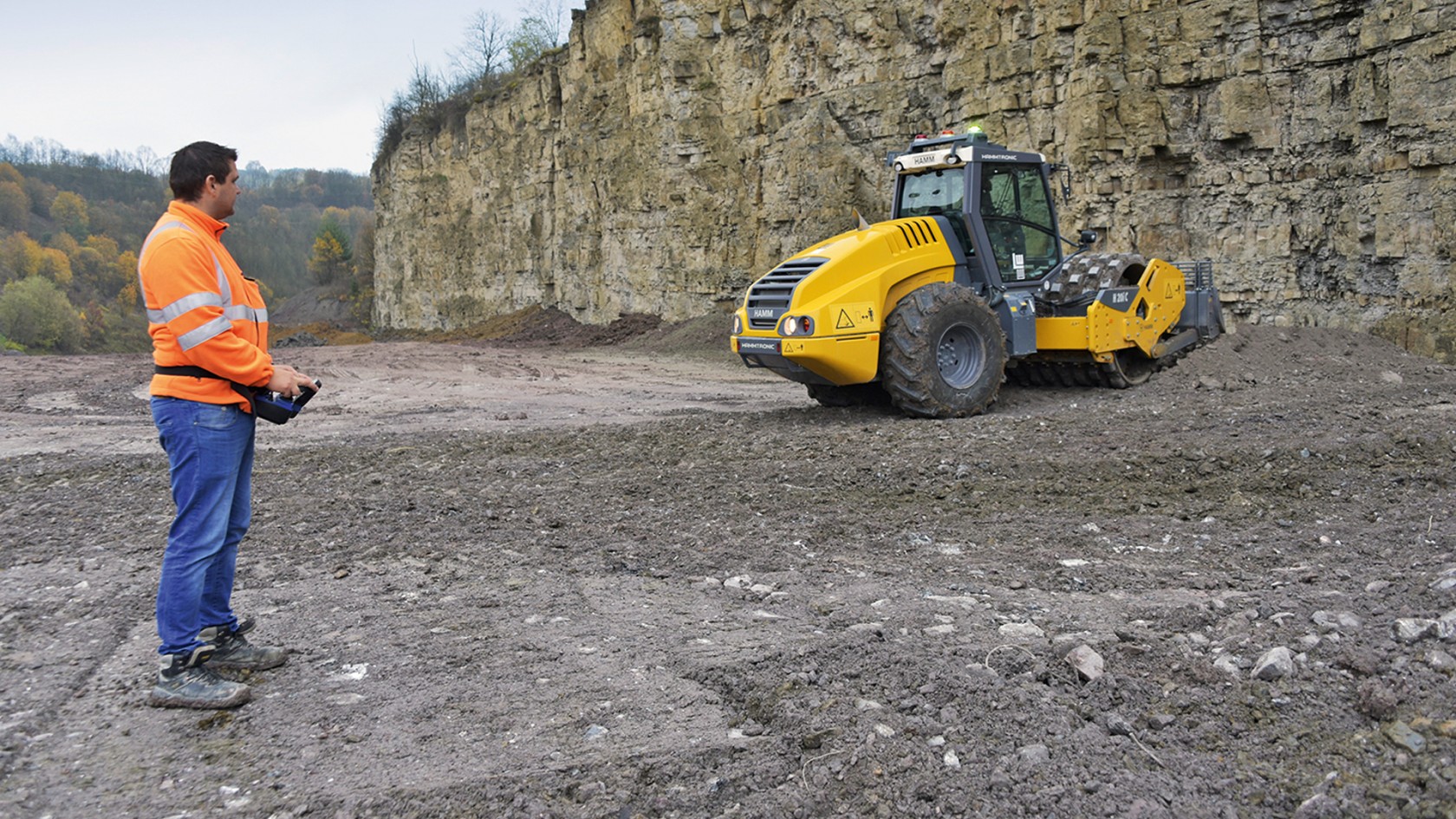
A highly specialised H 20i C P HAMM compactor was one of the key machines used when recultivating the Wilhelmsglück quarry. It backfilled and compacted the quarry with material that came from various construction projects in the region. HAMM equipped LEONHARD WEISS GmbH & Co. KG with two 20 t padfoot rollers with a special dozer blade for heavy-duty earthwork applications specifically for this purpose. Furthermore, HAMM developed a remote control for the rollers, since there is a risk in the quarry that the vibrations caused when compacting will cause stones from the rock face to come loose and fall onto the roller. The roller could also be remotely controlled to safely compact the area immediately in front of the break-off edge of up to 35 m without personnel having to remain in the cab and therefore in the danger zone.
Safely compacting in the quarry
The compactors with remote control were working for a long time in the Wilhelmsglück quarry, which is located close to Schwäbisch Hall. LEONHARD WEISS backfilled this quarry with material that came in large volumes from various construction projects in the region. The objective was the complete recultivation of the quarry with an impressive capacity of around 5 million tonnes while making optimal utilisation of the space. To do this, the backfilled material should be compacted in the best way possible so that it is covers a wide area – even as far as the peripheral areas. It is precisely this that represented a challenge since, when compacting with vibration close to the 35 m high break-off edge, it could not be ruled out that stones would break away from the edge, fall onto the roller and endanger the driver.
Partnership-based development process
"We adhere to strict safety regulations. For this reason, having personnel work right in front of the edge was not an option for us. Our Road Building team therefore worked together with their colleagues from the Special Technology department to look for alternatives in order to backfill and compact these critical areas," explains Site Manager Daniel Horcher. "After some research, using a remote-controlled compactor seemed to be the simplest yet most versatile solution." Employees from the Special Technology department at LEONHARD WEISS approached HAMM with this request. A team there developed a complete remote control for the H series compactors in just three months.
Operating the machine in this way is basically identical to doing so in the driver's platform: As soon as the remote control was activated, a specially developed lamp console above the cab indicated whether the roller was ready for operation. If the light was "green", the roller could be started, stopped and steered by remote control. Furthermore, the vibration frequency and working speed could be adjusted, and the dozer blade could be operated. "A large display on the remote control displays the driving direction and speed at all times. Furthermore, the operator can clearly see the operating data from the drum and engine, meaning that they can guarantee that the roller operates safely. Basically, with this remote control, we are moving the driver's platform outside," observed Hans-Peter Patzner, who is responsible for this special project at HAMM as an engineer for control technology. In the meantime, there were already additional applications for the remote-controlled compactor: From time to time, it is used on surfaces where mining or special geological cavities in the ground are to be expected.
Process optimisation thanks to a new dozer blade
However, the two H 20i C P compactors in the Wilhelmsglück quarry still had more to offer because HAMM also developed a new dozer blade for this project. The background: In peak times, up to 6500 t material is delivered to the quarry each day and spread using caterpillar vehicles. To cope with these enormous volumes, an additional caterpillar vehicle and an additional roller would have had to be procured. Two machines would also mean two drivers. But this would be problematic because, according to Sabine Voß, Procurement Manager for Compaction Technology in Construction Machine Technology at LEONHARD WEISS: "Qualified personnel are a rare commodity these days. In particular, it is difficult to find new people to operate special machines. It was therefore important to us to master the backfilling with one machine that can be operated by our current employees."
Developed for the job in hand, in dialogue
This therefore led to the idea of modifying the dozer blade from HAMM's product range for the new compactors. In particular, this involved increasing the dozing volume, and a shape that is adjusted to the heavy material. A prototype was built very quickly. LEONHARD WEISS tested it on various construction sites with different operators. "We have a lively, balanced dialogue with HAMM, in which the developer takes on board the feedback from the operators and the Logistics team, and incorporates this into the design. This ultimately led to the very machine that we need in our quarries," says the representative from the Special Technology department. "The roller drivers are satisfied. They are happy to work with the H 20i C P dozer roller."
Millions of tonnes of material have already been compacted
Both compactors with dozer blades have been in operation in the quarry for over two years. Site Manager Daniel Horcher summarises his experience as follows: "This combination unit can pave and compact smaller volumes of material without the need for an additional caterpillar vehicle. If the roller works on its own, a driver can spread and compact 500 to 1000 t per day. If larger volumes of 3000 t and more accrue per day, as is the case in Wilhelmsglück, the compactor with dozer blade supports the bulldozer that is already on-site. Furthermore, a compactor with smooth drum is then still in use – except in the area in front of the break-off edge. In this case, thanks to the special design, filling depths of between 50 cm and 1 m are possible without any problems." And he should know – his team previously used this roller compacted several million tonnes of material from different sources.
Switch from remote control to cabin operation in seconds
When asked how he would approach the task a second time, Site Manager Daniel Horcher answered immediately: "I would do it the same way again. The compactors with dozer blades make things much simpler for us because, in smaller quarries, we can reduce our fleet by one caterpillar vehicle per quarry. Where required for safety reasons, we use the machine with remote control. In all other areas, the second compactor without remote control is used from the start. And, of course, we always operate the remote-controllable compactor as normal from the cab when we are working far away from the edge. Switching between the two is incredibly easy. All it takes is the touch of a button."