The catalyst in asphalt production.
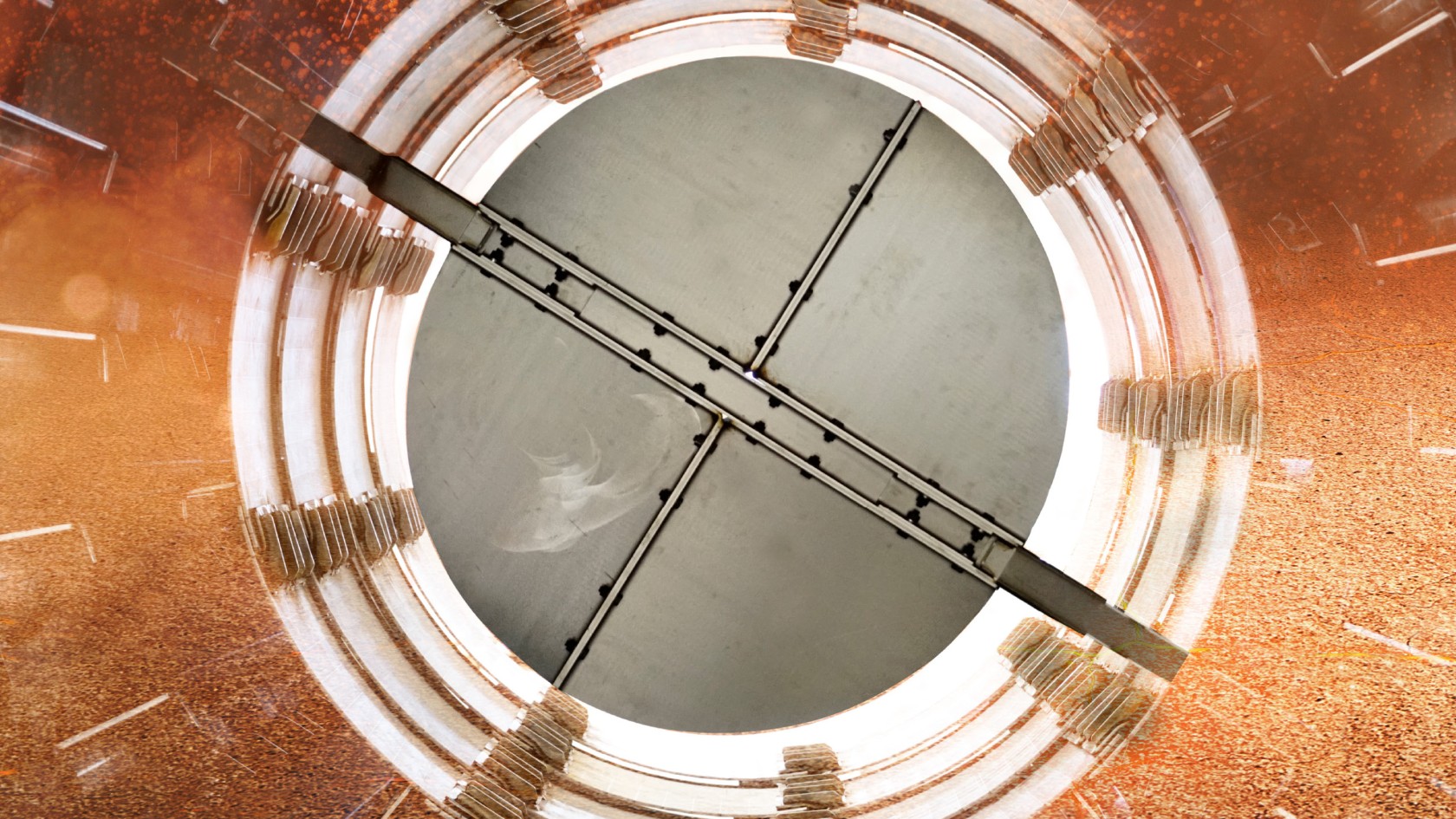
The Benninghoven REVOC system is a pioneering technology that gives plant owners the ability to achieve higher recycled material input rates while complying with stricter emissions limits.
The patented technology supplements existing cold and hot recycling systems in asphalt mixing plants and reduces total carbon emissions (VOC) with up tp 50 % recycling material added. The specified limits are not exceeded.
The permissible emissions limits are being tightened up in many regions worldwide. Complying with these during asphalt production with recycling material is a challenge that plant owners have to tackle.
As soon as recycling material has to be added to the mixing process, complying with the permissible limits for total carbon (TC/VOC) from the volatile organic compounds becomes a complex task. These VOCs are more potent greenhouse gases than CO₂ and are also hazardous to health at higher concentrations. In future, these emissions will have to be reduced as much as possible with the objective of securing both the future of the plant site and the operating license for existing asphalt mixing plants.
The key advantage of the REVOC system is that it can help to secure the future of asphalt mixing plants, because this added eddiciency, the use of recycling material and the emissions parameters allow plant owners to maintain the foundation of their business in the future.
In particular in light of the ever more restrictive requirements from government authorities, the REVOC system is the economical option for smooth operation.
The BENNINGHOVEN REVOC system is a complete process system. To reduce emissions and comply with standards and administrative regulations such as the German TA-Luft regulation, the entire process has to be considered: burner, fuel, recycling feed systems, dedusting, dimension of the dryer drum and the REVOC system.
The emissions can meet or fall below the required limits only if these factors are perfectly coordinated technically and the plant is run expertly and with the targets in mind.
First, the exhaust gases are actively extracted directly where they are generated, primarily from the mixer in the asphalt mixing plant – where heated mineral, the recycling material and the bitumen come together to be mixed into fresh asphalt. The vapours with high CT concentrations are then moved to the REVOC system for thermal processing.
The energy that is generated for drying and heating the virgin mineral (primary function) is used by the REVOC system to also burn off the overall carbon (secondary function), making operation of this innovation highly energy-efficient.
Working more efficiently with sustainable and economical technologies is the challenge of today and tomorrow. Benninghoven offers a variety of innovative solutions for increasing sustainability in asphalt production.
Learn moreAsphalt production, recycling systems, combustion technology, control systems and bitumen technology – with BENNINGHOVEN technologies, every customer can find the right solution for their location, according to the specific requirements and conditions.
To the technologies