Operating principle in situ
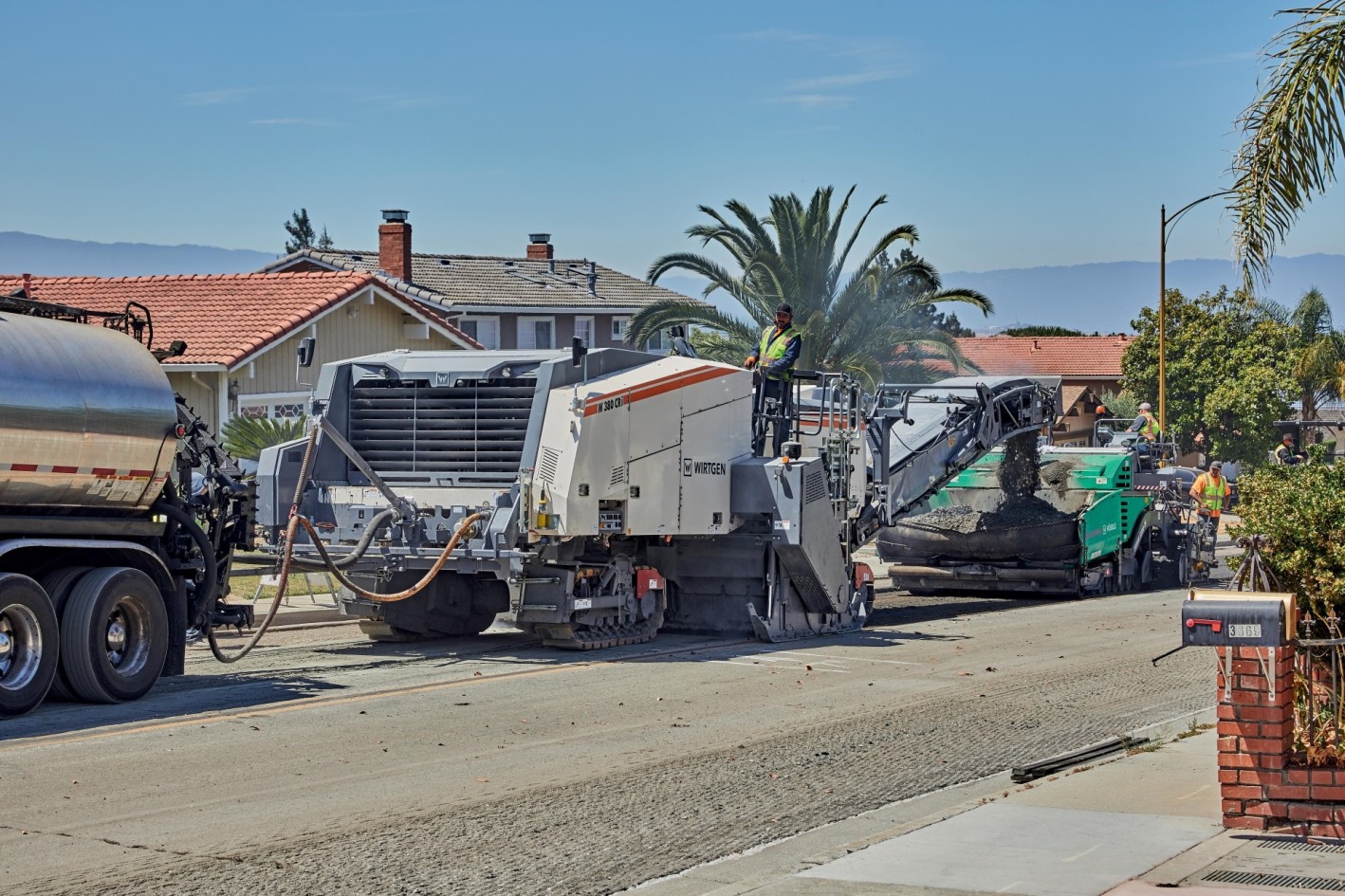
Where specified, cement is pre-spread by a STREUMASTER binder spreader which is followed by water and binder tanker trucks. The milling and mixing rotor installed in the W 240 CR / W 240 CRi granulates the asphalt layers. The pre-spread cement is mixed in at the same time while water and bitumen emulsion or foamed bitumen are injected into the mixing chamber via injection bars. The recycled construction material is transported to the rear of the machine via the primary conveyor and paved true to grade and slope by the VÖGELE paving screed with integrated spreading auger. Final compaction of the material is then effected by HAMM rollers.
The robust milling and mixing rotor granulates the damaged asphalt pavement. The granulated material is mixed with injected binders and water in the mixing chamber, thus creating a new homogeneous mix in an in-situ process.
Due to the helical design of the milling and mixing rotor, the recycled mix is conveyed towards the centre and subsequently transported to the paving unit via the primary conveyor. The spreading auger distributes the material evenly ahead of the variable paving screed which then paves it true to grade and slope.
Where specified, cement is pre-spread by a STREUMASTER binder spreader which is followed by water and binder tanker trucks. The milling and mixing rotor granulates the asphalt layers. The pre-spread cement is mixed in at the same time while water and bitumen emulsion or foamed bitumen are injected into the mixing chamber via injection bars. The recycled construction material is picked up by the conveyor system and transported right into the material hopper of the VÖGELE asphalt paver for placing. Final compaction of the material is then effected by HAMM rollers.
The robust milling and mixing rotor granulates the damaged asphalt pavement. The granulated material is mixed with injected binders and water in the mixing chamber, thus creating a new homogeneous mix in an in-situ process.
Due to the helical design of the milling and mixing rotor, the recycled mix is conveyed towards the centre and subsequently transported to the material hopper of the asphalt paver via the conveyor system comprising primary and discharge conveyor. The asphalt paver then paves the material true to grade and slope.
Lateral premilling and recycling with loading conveyor and paver
Cold milling with discharge conveyor and truck
As a pioneer in cold recycling, WIRTGEN is passionately committed to this environmentally-friendly and economically efficient method. The technological lead we have gained in this complex sector enables us to maintain the functional properties of roads in the long term.