Asphalt mixing plants
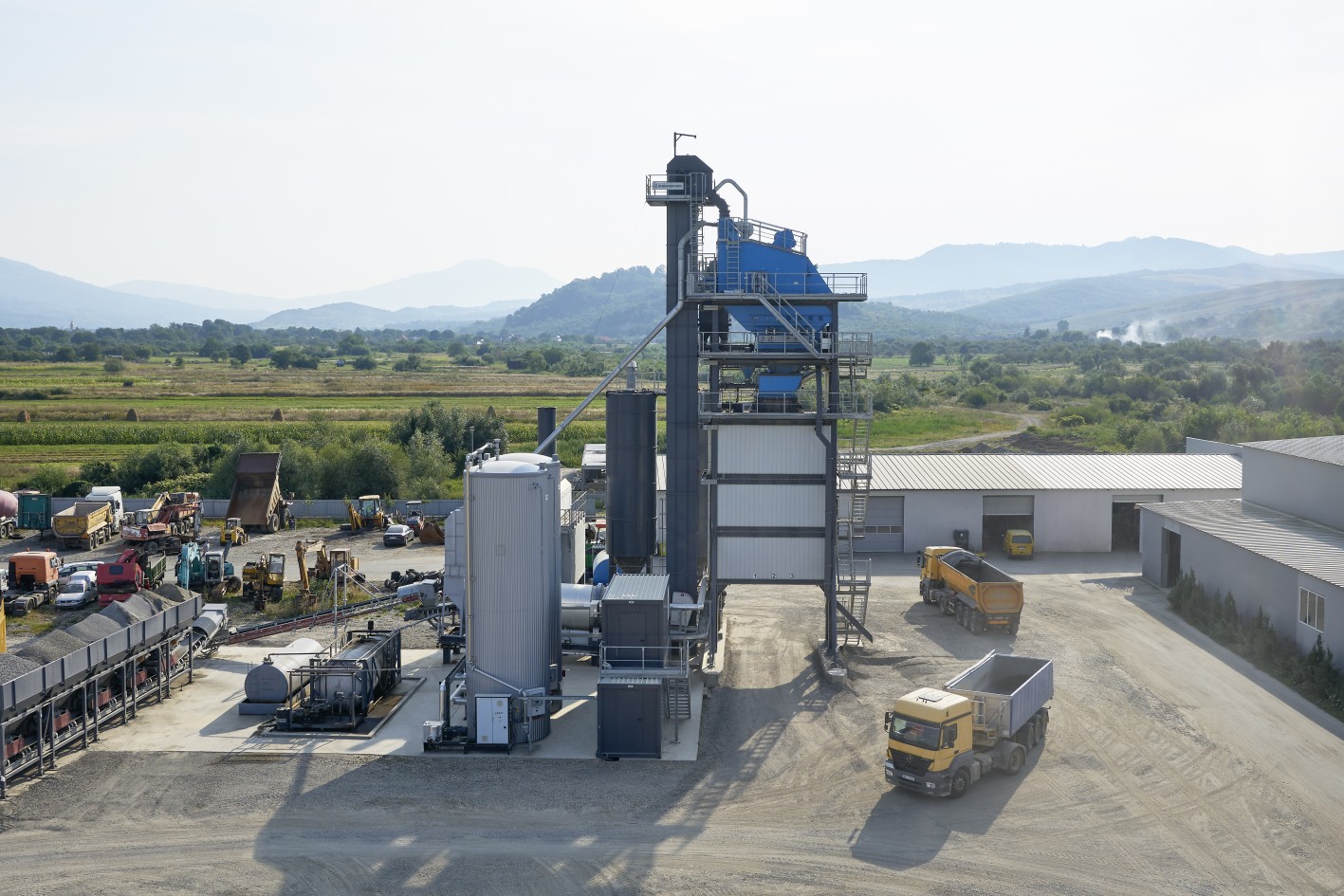
Commissioning of three ECO and TBA asphalt mixing plants
Three asphalt producers in Romania have invested in state-of-the-art technology from BENNINGHOVEN. The asphalt mixing plants are working at different locations in the country, but all are united by one great objective: to build and expand this EU member state’s long-distance road network. They decided to purchase ECO and TBA asphalt mixing plants – for convincing reasons.
Roads connect people, markets and countries. At the same time, they are a key factor in economic success. In Romania, these are important reasons to invest in expanding the motorway network - not least also to promote economic growth and in some cases, make it possible in the first place. An important pan-European goods route with the corresponding heavy traffic passes through this south-east European country, but these long-distance roads are in need of rehabilitation, even though at just 750 kilometres, the network is comparatively small.
Romania has set itself the goal of catching up Europe – and also of launching an infrastructure programme. Overall, the aim is to extend the country’s motorways to a total length of 2,710 kilometres. An impressive 223 kilometres are currently under construction.
In order to be able to benefit from this investment, a great many public and private road construction companies are positioning themselves as looking to the future. As part of this process, more and more asphalt mixing plant owners are relying on efficient, user-friendly technology from BENNINGHOVEN. Not without reason ... the WIRTGEN GROUP company has been involved in Romania for decades and is firmly anchored in the construction industry. In addition to quality and ruggedness, the customer proximity and user-focussed service which people experience play a key role in the company’s great market success.
In addition to plant technology, these options also cover the plant’s appearance. A specific colour can be required for different reasons, whether local authority specifications to integrate the plant more harmoniously in the environment or a customer’s requirement to implement specific corporate colours. The ECO 2000 in Timisoara is orange. These are the kinds of customer requirement which BENNINGHOVEN can easily satisfy because in its new factory, the WIRTGEN GROUP company has implemented high production standards – and commissioned a new powder-coating facility among other things.
Quality and ruggedness for surfaces: new BENNINGHOVEN powder-coating facility
More than a free choice of colour: the new powdercoating facility enables BENNINGHOVEN to create surfaces with maximum resistance to chemical and mechanical attack. The corrosion protection is especially durable, the surface also resistant to scratches and impact, weathering and abrasion. Furthermore, the surface is UV-resistant – all without any clear varnish finish. Now no need for concessions on colour, either.
A great many of the components in asphalt mixing plants are operated using compressed air. In terms of supply, BENNINGHOVEN leaves the choice to the customer: it is possible to choose between a compressor unit and a compressor container.
The premium solution is the compressor container – with clear benefits: in this case, the screw compressor is fitted inside a standard 20-foot container, opening up a further, useful workshop space for operators, including lighting and a power supply socket.
TBA plants are likewise quick to move, as primary components are designed in container form with plug-in cabling and transportable foundations.
High-tech facilitates rapid production of asphalt for direct loading
Two BENNINGHOVEN highlights are particularly valuable for completing direct loading as quickly as possible: the generous hot bin which can hold 80 t of white mineral and the BENNINGHOVEN BLS 3000 control system. The latter controls the TBA via an article-based formula and order system.
This means that as many formulas as the customer wishes can be entered and managed. When orders come in, the suitable formula then usually just needs calling up. The mixing supervisor of the TBA 2000 in Blejoi can react flexibly to delays in the day’s operations by splitting orders into part-orders or interrupting orders to give priority to others. The residual quantity is then stored automatically and taken into account when the order in question is resumed.
More than just new plants: retrofit solutions from BENNINGHOVEN
In addition to new asphalt mixing plants with all their benefits, BENNINGHOVEN also supplies retrofit solutions for existing plants. Adding power to existing asphalt mixing plants by retrofitting them with EVO JET burners, for example, is worthwhile in both economical and ecological terms.
BENNINGHOVEN accordingly offers the option, unique in the world, of being able to burn four different types of fuel. Depending on the burner model, and on which fuel currently has the lower price or better logistical availability in the market, anything from oil to natural and liquid gas all the way to solids like coal dust can be used as fuel. At the push of a button, EVO JET burners can easily and significantly minimize the high costs resulting from price fluctuations, delivery bottlenecks and downtimes.