Rehabilitation of a major road with the InLine Pave train
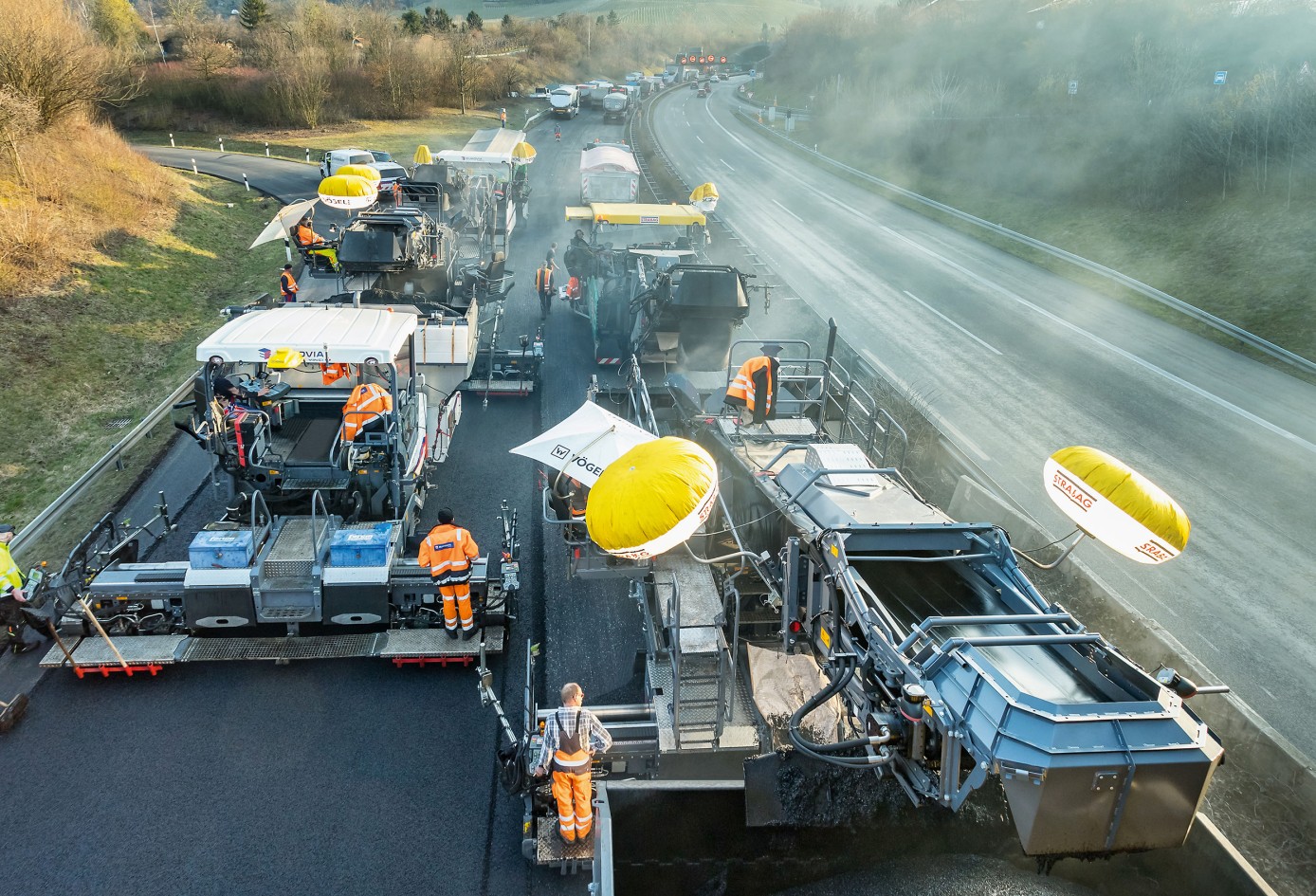
On a major road near Stuttgart, two VÖGELE InLine Pave trains took just two weekends to rehabilitate both carriageways of a 2.2km section of road.
Germany // Stuttgart
Increasingly complex criteria have to be met when rehabilitating roads, for instance minimization of traffic delays and maximization of efficiency. When the major B 14 road near Stuttgart – “Germany’s traffic jam capital” – was rehabilitated, VÖGELE’s InLine Pave technology scored on precisely these requirements. The process of building asphalt pavements “hot on hot” is ideally suited to rehabilitating roads by means of a moving job site so that these roads can be reopened to traffic quickly. The process also makes construction projects economical, because the most cost-intensive of the upper asphalt layers, the surface course, can be made thinner. This was another feature which allowed the rehabilitation to be completed over just two weekends - so without the kilometres of traffic jams which would have been inevitable during the weekday rush-hour.
Two InLine Pave trains rehabilitating a road outside Stuttgart, Germany’s “traffic jam capital”: one MT 3000-2i Offset material feeder, one SUPER 2100-3i IP paver and one SUPER 1800-3i paver on each carriageway completed high-quality rehabilitation of a major road.
Rehabilitation of the major B14 road with the InLine Pave train near Stuttgart, Germany
In a joint venture with Strabag AG, contractor Eurovia GmbH used two latest-generation InLine Pave trains to complete the rehabilitation work at top speed. Each paving train comprised a VÖGELE MT 3000-2i Offset PowerFeeder, a VÖGELE SUPER 2100-3i IP (InLine Pave) paver for binder course fitted with the AB 600 TP2 Plus High Compaction Screed and a SUPER 1800-3i paver for surface course. This allowed both the carriageways, along with their respective hard shoulders, to be paved both “hot on hot” and “hot to hot” across a total width of 10.8m. Each of the four machines paved a width of 5.4m. A total of four paving teams worked in two-shift operation so that the sections could be handed back to the region’s commuters punctually at 5 am on the Monday mornings after the works.
Needless to say, job site logistics were also perfectly planned: to ensure that the InLine Pave trains could work without interruption, the binder and surface course mixes needed to be supplied in turn – a total of 7,500t or 300 lorry loads per weekend. To ensure that there was always sufficient mix ready to transport, the asphalt mixing plant, too, was included in the planning process, allowing the pave speed of 3.5m/min to be maintained throughout.
SUPER 2100-3i IP: the most important innovation in the paver for binder course is the new transfer module for conveying the surface course mix to the downstream paver. The module has been extended by one metre. As with the MT 3000-2i Offset material feeder, a diesel heater now maintains the mix at a constant temperature, preventing it from sticking to the conveyor.
Also new is a second paver operator‘s platform with height-adjustable seats which can swivel 90° beyond the width of the paver. Functions of the paver and the transfer module can be controlled from here using the paver operator‘s ErgoPlus 3 console. Two freely positionable cameras ensuring optimum all-round visibility help enhance safety and quality. The process of removing the module for conventional use of the paver has been simplified.
SUPER 1800-3i: in the surface course paver, a new camera system improves the view into the extra material hopper, helping to avoid bottlenecks in the supply of mix. Like its predecessor model, the SUPER 1800-3i is fitted with a water spray system which prevents material sticking to the 40cm-wide crawler tracks. The machine can now be fuelled conveniently from the ground.
SUPER 2100-3i IPWhen paving with InLine Pave, the binder and surface courses interlock particularly intensively, creating a high-quality bond. After all, a perfect bond between layers is a fundamental requirement for the longevity of roads. With InLine Pave, the binder course is thicker, whilst the surface course is thinner at 2-3cm. The resulting pavement has higher degrees of compaction and fewer air voids following subsequent final compaction by rollers. The surface course is consequently impervious to water and protects the binder course from harmful effects. Resistance to deformation due to heat rises at the same time and this, in turn, helps counteract rutting during the summer months.
With RoadScan, VÖGELE’s temperature measurement system, contractors can make paving quality measurable and verifiable. The heart of the RoadScan system is an infrared camera which scans the whole of the asphalt pavement. What sets the system apart is its unrivalled measuring accuracy. The VÖGELE system captures a grid of squares measuring 25 x 25cm across a measuring width of 10m. Each of the squares contains up to 16 individual measuring points which are then used to calculate a mean value. This allows the system to capture the newly paved surface with no gaps, so no theoretical or computed values need to be added. RoadScan can measure a temperature range between 0°C and 250°C with a tolerance of just ±2°C.
The InLine Pave process delivers high quality, despite the fact that bitumen emulsion is not pre-sprayed between the binder and surface courses. This step can be omitted because the two pavers place the binder and surface courses “hot on hot” whilst operating “in line”, i.e. one behind the other, just a few metres apart. The process is consequently more environmentally-friendly and efficient, as well as cost-effective - to the benefit of contractor and client alike. This benefit is further enhanced by the fact that single-lane rehabilitations – a much more frequent approach in practice – can dispense with time-consuming road blocks.
Use of another technology underlines the priority given to quality in the construction project: RoadScan. VÖGELE’s non-contacting temperature measurement system was fitted to both the SUPER 1800-3i surface course pavers. RoadScan makes paving quality measurable and verifiable by measuring and documenting temperature across the entire pavement directly after paving. Temperature is known to have a key impact on paving quality: the mix can only be only compacted to the required degree if it is within the correct temperature range, if it is homogeneous and if it has the correct viscosity. “The RoadScan system is truly sophisticated and does not obstruct operations in any way. It is quick to install and operates very reliably, so it provides genuine support. Firstly, we are able to monitor whether the mix temperature is correct ourselves, and secondly, we always have verification to hand,” explains Dieter Keck, Senior Asphalt Foreman at Eurovia GmbH.
Tracked paver Special Class
Basic width | 2,98 m |
Pave width, max. | 8,5 m |
Maximum laydown rate | 1.100 t/h |
Extending screed
Compacting systems | TV, TP1, TP2, TP2 Plus |
Pave width | 2.55 m - 8.50 m |
Basic width | 2,55 m |
Extending screed
Compacting systems | TV, TP1, TP2, TP2 Plus |
Pave width | 3.00 m - 9.50 m |
Basic width | 3 m |